Six Essential Properties of an Efficient Cell Layout
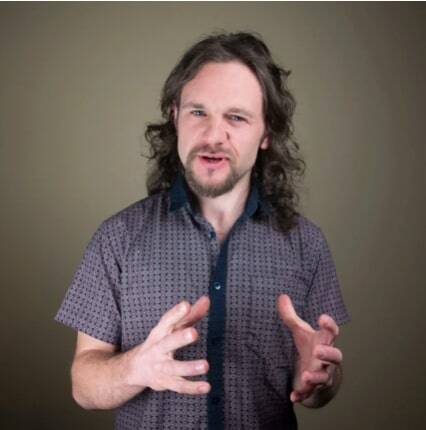
How can you ensure your robotic cell is efficient? A good place to start is to design a cell layout with these six essential properties.
When you've chosen to invest in a collaborative robotic cell, you want to make sure it's as productive as possible, right?
To achieve high productivity, you have to design your cell layout to be as efficient as possible. Small changes in cell layout can reduce the robot's cycle time, which in turn can lead to large productivity gains over the long term.
All this can be accomplished simply by setting up your cell to have these six essential properties, which are based on industrial robotics research and the fundamentals of Lean Robotics.
Six essential properties of an efficient cell layout
An efficient cell is one that minimizes the distances traveled and motions made by the robot, while allowing the robot to complete its task effectively.
1. Short motion times
The robot should spend as little time as possible moving around the workspace.
This is the most important property of a cell layout. The robot should not have to move any more than absolutely necessary. Every millisecond that the robot spends unnecessarily traveling around the workspace is wasted time.
Let's take an extreme example: imagine you program a UR5 to move 1 mm clockwise in a circle. However, instead of simply moving the base joint a fraction of a degree clockwise, your program makes the robot spin 359 degrees counter-clockwise before arriving at the point.
This mistake means that instead of taking less than 0.1 seconds, the whole movement takes over 5 seconds. That's 500% longer just because of a simple programming error!
Most problems you encounter will be much smaller than this, so they'll be harder to spot. Still, you should keep an eye out for any motions that could be taking longer than necessary.
The motion time is affected by both the robot's physical environment and the quality of your programming (as in our example). It's always worth looking over your program again and working out how you can keep motion time to a minimum.
2. A small cell footprint
Your cell should only be as big as necessary for the robot to effectively complete its task. Aim to use as little physical space as possible.
This has two benefits:
- A smaller cell means smaller distances for the robot to travel, which cuts down on unnecessary motion time.
- A smaller cell takes up less space in your business, giving you more space for other equipment and activities (important when floor space is a limited resource, as it pretty much always is!).
Of course, this doesn't mean you should cram your robot into a tiny area and hope nothing gets damaged. There's a happy medium. However, just thinking about how you can reduce the cell footprint is a good way to start improving your cell's efficiency.
3. Everything within reach
All objects and workspaces should be within easy reach of the robot.
Every robot model has a maximum distance it can reach. This property might be called its "reach," which refers to a 1-dimensional (1D) distance from the robot's base, or its "workspace," which is a 2D or 3D representation of the robot's reach in all directions.
Your cell layout should be designed in such a way that everything is easily within reach of the robot, as defined by its specifications. The closer everything is, the less the robot will have to move around the cell.
4. Optimal use of the robot's workspace
Another thing to optimize is the robot's workspace.
For instance, consider which parts of the robot's workspace are used for manipulation tasks, because some areas are better than others. Your goal should be to move any high-manipulability tasks (e.g., assembly) to areas of the workspace where the robot is most dexterous.
Researchers Izui et al from Kyoto University in Japan explain that manipulability is "a quantitative measure of the manipulating ability of robot arms." A point with high manipulability can be reached from many different orientations. A point with low manipulability can only be reached by one or two orientations.
In general, high-manipulability areas are located in the center of the robot's workspace. Low-manipulability areas tend to be concentrated around the edges of the workspace, near the robot's body, and around singularities. Keep those things in mind when evaluating your robot's workspace.
5. Neat and tidy
The workspace should be clean and organized. As Benjamin Franklin said, there should be "a place for everything, and everything in its place."
Untidy cells are a sign of inefficiency. This is related to one of the core principles from the 5S Approach to Lean manufacturing. In this context, tidiness doesn't just mean keeping the cell free from dirt; it means having clear systems in place to keep the cell working most efficiently.
You can read all about the 5S Approach to robotic cell design in this article: How to Create an Efficient Robot Cell with 5S.
6. Lean outputs and inputs
The outputs and inputs of the robotic cell should have precisely defined locations within the workspace.
According to the Lean Robotics framework, which guides you through the process of designing a robot cell, one of the first steps is to clearly define the cell's outputs. In terms of layout, you should decide where the outgoing objects will be located in the cell, and how they'll be transported from the robotic cell to the next stage in your manufacturing process.
The next step is defining the cell's inputs. In terms of layout design, you should decide where incoming objects will be placed and how they'll be presented to the robot. Typical part presentation methods include matrices, trays, conveyors, and unordered bins.
For a step-by-step guide to designing a robotic cell, check out the Lean Robotics book at leanrobotics.org.
Leave a comment