How to Create an Efficient Robot Cell with 5S
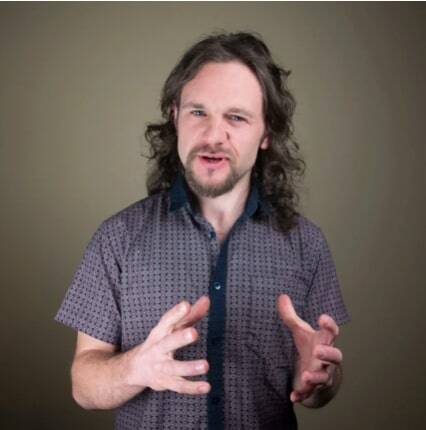
How can you ensure your robot cell will be effective and efficient? By applying the 5S Approach! It's just like cleaning your toolbox… sort of.
The 5S approach is a way to ensure that your work cell runs at maximum efficiency. It is a key concept in Lean Manufacturing and, by extension, in Lean Robotics too.
The basic idea of 5S is that a clean, organized work cell will run much more efficiently than a dirty, disorganized one. Makes sense, right? However, keeping your work cell organized is easier said than done. The 5S approach provides a formal process for making any space consistently clean and tidy.
In this article, we introduce the five S's of the 5S approach and then explain how you can apply them to any robot cell.
What is the 5S Approach?
The 5S approach is one of the original tools from the Toyota Production System, the precursor to Lean Manufacturing which you can find out about in our article What's the Difference Between Lean Robotics and Lean Manufacturing? It is simply a technique for maintaining an orderly work space.
The name "5S" refers to the five stages of the technique, each of which starts with the letter S.
To introduce these stages, I'm going to use an example from my own workshop.
Let's meet my toolbox…
I have a grey, plastic toolbox. It's flimsy, very disorganized and has only one main compartment. On top of all that, the whole thing falls apart every time I pick it up.
Not a very effective toolbox.
However, I shouldn't put all the blame on the box itself. The biggest problem is the way that I use it.
Whenever I want to find a tool, I can't because all the tools are piled on top of each other. I have to empty the whole box all over the floor to find it. Then I think, "I'll probably need another tool in a minute, so it doesn't make sense to put them all back again." For the rest of the day there are tools spread all over the floor. The more work I do, the more the tools migrate all over my flat.
This is exactly the problem that the 5S approach was designed to combat.
How to Apply the 5S Approach to a Toolbox and a Robot Cell
Let's look the five stages of 5S and how I could apply them to my toolbox. For each stage, I'll also show how this applies to: a robot cell and robot programming.
Applying 5S to a robotic cell is much the same as applying it to a toolbox. Programming is a little different, because you are applying 5S to a non-physical space, but the theory is the same.
If you are new to robotics, you also have an advantage that everything about the robot cell is new. It's a perfect time to implement a 5S work cell. Your team won't have had had time to develop bad habits — like I have with my toolbox.
1. 整理 (Seiri) — Sort
The main goal of this stage is to remove unnecessary objects and waste from the workspace. Depending on the amount of things, this can take some time. In shared spaces, as most manufacturing cells are, the stage should involve everyone who uses the workspace. Often, red tags are used to mark items which are planned for removal. Unless someone can raise a good reason for keeping an item, everything with a red tag is removed.
In all five of the stages, it is important to keep asking questions about items. This makes people really think about whether or not they are necessary.
- In the case of my toolbox, I would go through the box and get rid of any tools or items that I don't need any more. Are those plastic washers hanging around at the bottom of really necessary? What about those tubes of hardened superglue?
- For a robot cell, think about what is absolutely necessary in the cell. Identify the essentials and remove everything else. Part of this stage may involve repair. For example, if you keep a spanner in there because the CNC machine has a bolt that keeps coming loose, aim to properly repair the machine instead of tightening the bolt every other shift.
- For robot programming, get rid of obsolete program functions, confusing version numbers and unhelpful comments.
2. 整頓 (Seiton) — Set in Order
This stage is all about storing each item properly. Commonly used items should be stored where they are easily accessible and clearly visible. Items which are necessary but rarely used should be stored elsewhere.
An important part of this stage is to begin to develop a culture of storage within your team. As 5S expert Oscar Olofsson says "It is one thing to set up storage areas. It is another to have people use them properly."
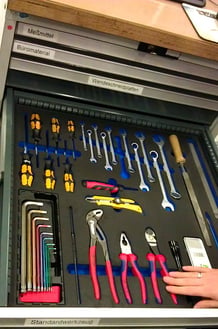
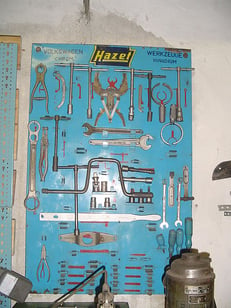
- Unfortunately for my toolbox, this stage is probably where I should get rid of the toolbox itself. At the very least, I should invest in extra storage. Popular options for 5S workshops are shadow boards or foam drawer inserts. These give each tool a unique storage space and make it obvious when one tool is missing.
- For the robot cell, ensure that everything has a place within the cell and store it where it will be handy. Things which are rarely used should be stored out of the way and regularly used items should be visible with defined storage places.
- For robot programming, decide on a clear structure for your programs with consistent version numbering, variable names and comment formatting.
3. 清掃 (Seiso) — Shine
This is the stage where you get out your mop and rubber gloves, and get cleaning. A clean work cell is an efficient work cell. However, this stage is not just about cleaning away the dirt. It also gets your team accustomed to the cleaning procedure so that they know how to maintain a clean workplace. One benefit of this stage is the good feeling the whole team will get when they see a clean, organized workspace.
- For me, this stage would involve cleaning all my tools before putting them into their new, organized storage spaces. I covered them all in cement dust recently, so this is quite a good idea!
- For the robot cell, do a big clean up before you begin using the cell. Get the team involved so that they become familiar with procedure.
- For robot programming, go through all of your code and implement the new structure and naming conventions. Clean up unused code and optimize where possible.
4. 清潔 (Seiketsu) — Standardize
While the previous stage is about doing a one-time clean, this stage is all about maintaining a consistent standard of cleanliness. During this stage you aim to answer the question: "The workplace looks great now. How do we keep it looking this great?" It involves setting daily sorting and cleaning tasks as well as spreading the work among all team members so that no one person is left doing all of it.
- For my toolbox, this stage would involve deciding to put tools back in their correct place every time I finish using them. I might also add my tool storage to my weekly list of cleaning tasks, so that I can notice if it is becoming untidy and sort it out before it gets worse.
- For the robot cell, it would involve setting standard procedures in place so that everyone knows how they should be cleaning the cell. This might involve a folder or laminated poster which explains the cleaning procedure.
- For robot programming, this means writing down your chosen program structure and naming conventions, and displaying the information somewhere that everyone can see it. A laminated "programming cheat sheet" can be a good way of maintaining order for programming.
5. 躾 (Shitsuke) — Sustain
This final stage is all about discipline. It is about training your team to maintain the standard of order and cleanliness that you have all agreed on. This involves long-term dedication to the 5S approach and continual improvement of the storage solutions to ensure that they still meet the needs of the team.
- For me, and probably for many of us, this stage is one of the most challenging. Sure, I might decide "I will put my tools back whenever I finish using them" but in practice this behavior often disappears after a few weeks. This stage would involve retraining myself to actually keep my tools in order.
- For your robot cell, this involves being vigilant and regularly revisiting the previous stages of 5S to remove items that have become unnecessary. It will also involve training new team members on the cleaning procedures.
- For robot programming, this means being consistent with versioning, code backup, user management and code testing procedures. Programmers should be trained in your chosen coding standards and the standards should be improved and updated wherever necessary.
How to Find Out More About Lean Robotics
Lean Robotics is a specific application of Lean concepts to make your robot cell deployment a success.
You can learn more about Lean Robotics by going to leanrobotics.org and grab a copy of the book while your there!
Leave a comment