What's the Difference Between Lean Robotics and Lean Manufacturing?
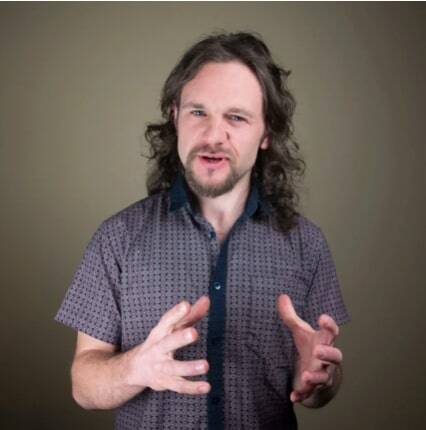
Posted on Sep 21, 2017 in Manufacturing
5 min read time
What is Lean Robotics? How does it fit with Lean Manufacturing ? Here are all the answers!
One of the first questions manufacturers ask us when we tell them about Lean Robotics is: Is that different from Lean Manufacturing?
The simple is, yes, Lean Robotics is different from Lean Manufacturing. However, they are closely related. Lean Robotics is based on the principles of Lean. If you are familiar with Lean Manufacturing, there will be a lot of familiar concepts.
In this article, we'll introduce the basics of Lean then explain how Lean Robotics fits in.
What is Lean Manufacturing?
Lean Manufacturing is a set of principles to improve productivity and reduce waste. The principles are based on the Toyota Production System, which was developed by Toyota in the 1990s. It was originally called "just-in-time manufacturing." Modern Lean Manufacturing incorporates Toyota's system with some other business tools.
Lean principles can be applied to all areas of business, not just manufacturing. Because of this, the word "manufacturing" is often dropped and the principles are referred to simply as "Lean."
The single guiding principle of Lean is this:
Maximize customer value while minimizing waste.
Various other principles form the foundations of Lean. However, it is important to remember that it is not simply a "box of tricks" — although it does involve a set of tools. Introducing Lean Manufacturing means inciting a change of mindset across the entire business.
The Seven Wastes of Lean
The key to Lean is minimizing "waste." The Toyota Production System, its precursor, defined three types of waste: muda (non-value-added work), mura (unevenness or lack of flow) and muri (overburdening people or processes). Lean implementations often focus on muda and less on the other two types.
Muda waste is defined as "actions that add no value." Lean defines seven types of waste that are common in manufacturing environments:
- Transport — Time lost moving materials or products from one stage of the process to another.
- Inventory — Storing more raw materials or Work in Progress than necessary.
- Motion — Any movements of workers which are unnecessary and add no value.
- Waiting — Time lost when workers are waiting for other processes to finish.
- Over-Processing — Adding more value than the customer requires, e.g. when features won't be used.
- Overproduction — Making too much product, which results in excessive inventory and storage costs.
- Defects — Products which are not up to standard will have to be replaced and the work put into producing the defect product is wasted.
All of the tools of Lean can be seen as reducing one or more of these seven wastes. Lean Robotics also places a lot of importance on waste reduction.
The Tools of Lean
Lean practitioners use a lot of business tools to reduce waste. Some common ones are:
- Value stream mapping — A way to map the stages of the process to determine how each stage contributes value to the customer.
- Kaizen (continuous improvement) — A way to continuously improve all parts of the business. In the real world, no process is ever perfect. All workers should be constantly looking out for ways to make the process better.
- Kanban (pull systems) — A scheduling system which is used to control the supply chain by eliminating queues of Work in Progress.
- 5S (or 6S)— A way to organize work spaces to be more efficient, using the five steps of: Sort, Set in order, Shine (i.e. clean), Standardize and Sustain. A sixth step, Safety, is sometimes added.
- Poka-yoke (error proofing) — A way to introduce mechanisms which bring attention to worker error as it happens to avoid inadvertent mistakes.
These tools are all important to Lean, but they are only a means to an end. The most important aspect of Lean is the change of mindset which comes with it. This is also true for Lean Robotics.
What is Lean Robotics?
Lean Robotics is a methodology which we have developed here are Robotiq.
Basically, Lean Robotics is a method to help you efficiently deploy collaborative robots in your factory. It applies Lean principles to collaborative robotics to make integration as straightforward as possible.
We developed it because industrial robots have traditionally been complex to deploy, involving high investment and disruption. This is no longer the case with collaborative robots, which can be deployed quickly and easily into your existing processes. However, you have to deploy them in the right way, otherwise they can cause as much disruption as traditional industrial robots. Lean Robotics teaches you the right way to introduce robots.
How Lean Robotics Incorporates Lean Principles
Lean principles are applied to robotics by considering each robot cell as if it were its own self-contained, mini manufacturing business. To do this, we define the terms:
- Suppliers — These are the processes which come immediately before the robot cell in the manufacturing line. For example, if the robot is assembling electronic boards, its suppliers will be all of those processes which provide it parts for assembly.
- Customers — These are the processes which come immediately after the robot cell in the manufacturing line. For example, if the robot provides assembled electronic boards to a packaging process, this will be its customer.
- Value chain — These are the steps that the robot takes to add value to the product.
Lean Robotics interprets the following concepts from Lean Manufacturing:
- Customer Value — Defining value from the customer's point of view — As the robot's "customer" is viewed as the next stage in the manufacturing process, "customer value" is whatever is important to that next stage.
- Value Chain Creation — Mapping the chain of activities that produce this value — This involves looking at all the actions taken by the robot to identify which of them add value.
- Waste Elimination — Conserving resources and eliminating waste throughout the entire value chain — This should happen at every stage of robotic deployment: design, implementation and operation.
- Continuous Improvement — Continually taking small steps to improve the process and take it closer to perfection — Deploying robots involves a steep learning curve for members of your team. Instead of trying to learn everything at once, we recommend building your team's robotic skills little by little.
In this way, we can apply established Lean techniques to robotic cells.
Lean Robotics: Small Scale Lean for Large Scale Improvement
Lean Robotics is a specific application of Lean concepts. We designed it to help you to deploy collaborative robots to your business. Although it focuses on the "small scale" of a robotic cell, it can have large scale effect on your business.
You can learn more about Lean Robotics by going to leanrobotics.org. Why not grab a copy of the book while you're there!
Leave a comment