3 Innovative Solutions to Overheating in Robotics
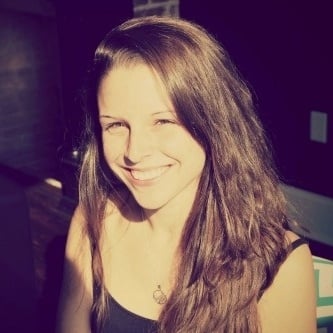
No matter how advanced our technology gets, we always seem to find ourselves battling disappointingly mundane problems—not least of which is heat management.
Whether it's to do with complex machines here on Earth or shuttles re-entering our atmosphere, we humans find ourselves up against heat on a regular basis.
Our robots do, too, which is why the following three technologies show so much promise for helping our robots operate under safer conditions.
Now that robots have gone mainstream, and are working alongside humans all over the world, one of the next big steps is rethinking how they keep themselves cool.
Collaborative robots are particularly ripe for innovation when it comes to better temperature management. This is the type of robot we're beginning to rely on to help us work better and smarter. So, it's only logical for us to ensure they're reducing—rather than adding to—the complexity of our workflows.
A robot that can prevent or address overheating and its side effects would be an asset indeed.

Excess heat continues to be a problem for robots, and must be managed carefully.
1. Liquid cooling and "sweating"
In some of the most exciting new developments in robotics, the problem of excess heat is being tackled from an unexpected angle—using the human body as a model.
One robot, named "Kengoro," was built with "muscles" and "tendons" that replicate the human body's skeleton and musculature and operate like a (somewhat eerie) marionette. But its designers didn't stop there—they also used porous aluminum to allow a water-based coolant to circulate throughout Kengoro's frame, enabling the robot to "sweat" through its "pores."
From its sweaty chassis to its nimble musculature, Kengoro demonstrates several innovations that might soon be standard issue on collaborative robots.
Kengoro is a robot with "muscles," "tendons," and even the ability to sweat!
2. Nanoscale temperature probes
The term "microelectronic device" applies to the components of many consumer electronics and cobots. These microelectronics often give off heat that must be channeled away—or otherwise dealt with—before it affects the whole device.
But when it comes to measuring temperature inside microelectronic devices, there has always been one big hurdle: including a temperature probe in something so small can throw off conditions enough to render your measurements useless.
Whether it's with digital-industrial machinery or a collaborative robot, we need to do better if we want to eliminate all the potential risks of heat.
Scientists are now eyeing nanoscale temperature probes as a way to allow our machines to monitor themselves for temperature variations.
These nanoscale probes are nothing like a conventional thermometric probe. Scientists are using the properties of materials used to build robots—like aluminum's oscillations under an imaging beam—as a way to measure local temperature gradients.
It sounds complicated, and it is. But the mechanics are surprisingly simple, and could have a wide variety of material applications, including letting metals and silicone effectively operate as their own thermometers.
3. "Activity trackers" for robots
One reason humankind has found itself so reliant on technology is because our bodies weren't designed for everything we want to do. For one thing, our eyes can only take in a limited amount of the world around us.
We're even more limited with regards to seeing what goes on inside our bodies—meaning we're often in the dark about critical system failures until it's too late for medical intervention.
Wearable activity trackers are getting better at giving us advanced warning of potentially fatal health conditions, but they still have a long way to go. Meanwhile, roboticists' attempts to do the same thing—but for robots—have made huge progress.
Researchers are looking at the natural, barely-audible vibration and "hum" all electronics and materials give off while they're doing "work."
Even the tiniest change in these vibrations is enough for sufficiently sensitive equipment to tell when something is about to go wrong, as sometimes happens with unsafe amounts of heat and friction.
The idea here is that machines and robots in the near-future will be able to run near-constant checkups in the background to monitor their overall "health," as well as the condition of individual components.
We rely on robots that work long hours at repetitive tasks, which inevitably causes them to suffer from general wear and tear. Perhaps in the future, we won't ever need to stop operations to repair them, because they'll already be doing it themselves!
Learn more about cobot risk assessment
Collaborative robots have the potential to raise productivity while working alongside humans. But as these technologies evolve faster than safety standards can keep up with, how can your factory benefit from cobots without compromising worker safety?
Leave a comment