3-Finger Adaptive Gripper Simulation Data
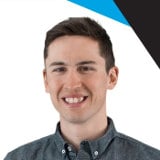
Posted on Jun 10, 2015 in Robot Grippers
3 min read time
At ICRA 2015 we got a lot of feedback requesting supplementary data concerning our 3-Finger Adaptive Gripper. The robotic end effector has been used for several applications that require simulations, so we thought it was time to make this data publicly available for everybody.
There are various applications that require simulations before going real time in real life. Most research labs perform simulations to test their solutions before trying the robot out in real life, mostly to avoid literally crashing a setup (that's the kind of stuff that can happen when you try new things!). With devices such as robots where safety is a big concern, you want to be able to control as many aspects as possible on the robot before pushing the start button. However, to do a simulation you need a minimum of information on the system you will be simulating. In the case of a robotic hand, you want to have a lot of mechanical information. There are a couple of data points that are crucial to running a good simulation. Notice that most of the simulations that are or will be done with our hands are dynamic and this increases the complexity of the simulation.
Simulation Data
Gripper Nomenclature
In order to avoid confusion and as with every good simulation you need to make sure your nomenclature is correct! Since it can get really complex because of the number of parts and because there are 3 fingers that work with the exact same principle, so again, you’ve got to get your nomenclature right. We have identified all the parts and pivots, so everyone can be sure they are talking about the same thing and using the same wording just check out the picture above.
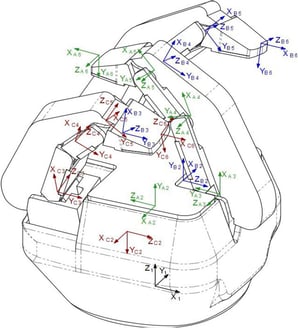
Coordinate System
To have a complete dynamic simulation you need to know the position of each pivot. In fact, each pivot has to refer to the next or previous one to make sense in the simulation. Since it is dynamic, all the pivots are moving when the finger gears are being actuated. Adding the fact that grasping an object changes the configuration of the fingers, knowing the phalanx position is crucial. Notice that each coordinate system follows the same rules (Z+ in the direction of the axis and X+ in the direction of the next pivot) Using the right hand rule, it is then possible to place the coordinate system in space.
HD Parameters
The Hartenberg-Denavit parameters, are used by the theory of the same name for articulated linkage-pivot mechanisms. The goal of this theory is to be able to predict the position of a part or the end of the articulated mechanism by changing the parameters presented in the matrix. In other words, if you want to know where a finger(s) are going to be in space when you do 5 motor rotations, you will be able to calculate it with the HD parameters. We have listed the HD parameters for each of the 3 fingers including the angle range in all Gripper axes.
Dynamic Data
Data from the springs, motors, gears and force are provided to complete the dynamic model of the 3-Finger Gripper. All this information is crucial when it's time to simulate the response of the Gripper when grasping an object. For example, how does the Gripper react in encompassing mode?
To get further information on what kinds of innovative projects have been accomplished with our 3-Finger Adaptive Gripper, take a look at this link.
Leave a comment