3-Finger Adaptive Gripper Raring to Go at the DARPA Robotics Challenge
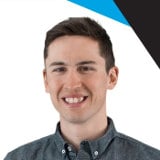
Posted on May 05, 2015 in Robot Grippers
6 min read time
The DARPA Robotics Challenge Finals are on their way and we are really excited. It is always fun to see research labs such as the teams at DARPA using our products. However, aside from the fact that we are pleased, what is the motivation of these teams to use the Robotiq 3-Finger Gripper for this contest? Here's what came out of our observations.
With 8 teams out of the 25 participating teams using our Gripper, it is the most frequently used Gripper in the whole competition. So there might be a good reason why teams are using the 3-Finger Adaptive Gripper. Here is a short list of some of the key points that we think will be useful for the teams. Notice that these advantages can also be used in industrial applications. Most of the teams are using regular programming methods (the same ones used in industry).
Dexterity
Some tasks at the DARPA Robotics Challenge will require a lot of dexterity. I only have to think about the ''Vehicle Driving'' and ''Valve Opening'' operations to recognize that a lot of dexterity is required. The 3-Finger Adaptive Gripper has several finger configurations (basic, wide, pinch and scissor) these can be used to grasp different parts of a handle, steering wheel or valve. With such different challenges you need to have a robot gripper that can adapt to the different situations.
Using vision feedback, the teams can see the shapes they want to grasp and can adapt the Gripper fingers to their needs. But even if you can configure your Gripper fingers into different positions, you still need to grasp the part, which leads to the next advantage of our Gripper: Adaptive technology.
Adaptive Technology
This is probably the most important reason why the teams are using our Gripper. In fact, the design and under-actuation of the Gripper fingers allow the robotic hand to be ''Adaptive''. In other words, the fingers will adapt to the shape of the object. By configuring the force, speed and position of the fingers, you can either grasp small objects with a lot of dexterity or by leaving the settings unrefined you can do rougher work.
As you can see in the video, there are a very wide range of applications that can be accomplished with the Gripper. This is basically due to its capability to adapt to different shapes and of course different situations.
Payload to Weight Ratio
The Gripper is also relatively light for the payload it can handle. If you compare it to other robotic grippers, the 3-Finger Gripper is able to lift more weight, while applying a lower load on the robot wrist and arm. This is the best of both worlds, since you want to minimize the weight of the tool you are using in order to transfer that extra unused weight to the potentially heavier object that you want to grasp, because remember, the weight limit for the robot arm includes the gripper and the object that it is grasping. The fact that the Gripper can also lock its fingers around a shape allows it to grasp objects with a bigger payload. So, you can figure that for the tasks that involve tool manipulation, the 3-Finger Gripper is ideal.
Simplicity
The Gripper uses 4 electric motors (1 for finger rotation, 3 for finger actuation) which reduces the risk of malfunction compared to grippers with more motors. The gripper is also easy to program even if there are a lot of parameters offered. By being able to set force, speed and position variables, the teams can change the settings in a few seconds to adapt the Gripper to the task being executed.
Teams Using the 3-Finger
Here's a short list of the teams that will be using the 3-Finger Adaptive Gripper for the DARPA Robotics Challenge Final. Remember these names, they are going to score high in the dexterity components of the challenge ;-)
- TARTAN Rescue: CHIMP (CMU Highly Intelligent Mobile Platform) took third place in the 2013 DARPA Robotics Challenge Trials. Carnegie Mellon University-NREC designed CHIMP to work in dangerous, degraded environments that were built for people, not robots. CHIMP’s near-human form factor, strength, precision, and dexterity give it the ability to perform complex, human-level tasks in these settings.
- Team HKU: The team from Hong Kong University is comprised of a group of researchers to undertake this interdisciplinary research project including: Professors, Researchers, PhDs, MSc and BSc students from HKU. Team members specialize in Robot Vision, Motion Planning, Control System, ROS programming, System & Networking programming, Human Machine Interaction and Robotic hardware.
- Team IHMC Robotics: IHMC Robotics is a team from the Institute of Human and Machine Cognition in Pensacola, FL. They are a dedicated group of researchers, scientists, and engineers from all over the world, ranging from local high school and undergraduate interns to post-doc researchers. Since the Challenge kicked off with the VRC for Track B teams, they saw well over 40 people come and go, all contributing to different key facets of their DRC effort. Their actual roster holds 22 team members. One of the many focuses of the IHMC Robot Lab has been advancing the study of walking and balancing for humanoid robots.
- Team MIT: Members of the team come from departments and labs across Massachusetts Institute of Technology’s School of Engineering, including the Department of Electrical Engineering and Computer Science, the Department of Mechanical and Ocean Engineering, the Department of Aeronautics and Astronautics, the Computer Science and Artificial Intelligence Laboratory, and the Laboratory for Manufacturing and Productivity.
- Team TRAC Labs: Team TRACLabs, based in Houston, TX is the only small business-run team to advance to the DRC Finals with DARPA funding. Two broad strategies guided their approach through the Virtual Robotics Challenge and Trials: (1) rely on human intelligence for high-level decision making and (2) treat the competition primarily as a matter of systems integration. With a robust and cohesive foundation in place, their goals for the Finals are to increase robot autonomy, improve robot control, and explore new strategies for human-robot interaction.
Team TROOPER: Their team has a solid history - including a top placement in the 2007 DARPA Urban Challenge - working across multiple autonomous platforms, in creating autonomy and control software that can guide robots. Their partnerships with the University of Pennsylvania and Rensselaer Polytechnic Institute gives their team a strong foundation from university research, as well as industry practices.
- Team ViGIR: Team ViGIR (Virginia-Germany Interdisciplinary Robotics), comprising researchers from TORC Robotics, Technische Universität (TU) Darmstadt, Virginia Tech, and Oregon State University, is a collaborative research and development effort aimed at advancing the state-of-the-art in humanoid robot control in order to allow for effective human-robot teams. Their goal is to enable robots to respond more effectively to humanitarian disasters, thereby reducing the risk to humans.
- Team WPI-CMU: Worcester Polytechnic Institute has teamed up with Carnegie Mellon University creating a seamless integration of theory and practice. The team is comprised of undergraduate students, graduate students, engineers and professors from around the world. Members have a variety of expertise in robotics software, balancing and walking behaviors, robot perception, project management, and professional software engineering.
So with a lot of teams using our Grippers we have learn that it is appreciated for is dexterity, simplicity and adaptability. We are still looking to enhance our products, but seeing such a high level team roster using our Grippers makes us feel like we did a good job for the moment. If you want to learn more about some different research projects the 3-Finger Adaptive Gripper is being used in, follow the link below.
Leave a comment