3 Challenges Manufacturers Face When Implementing Robotics
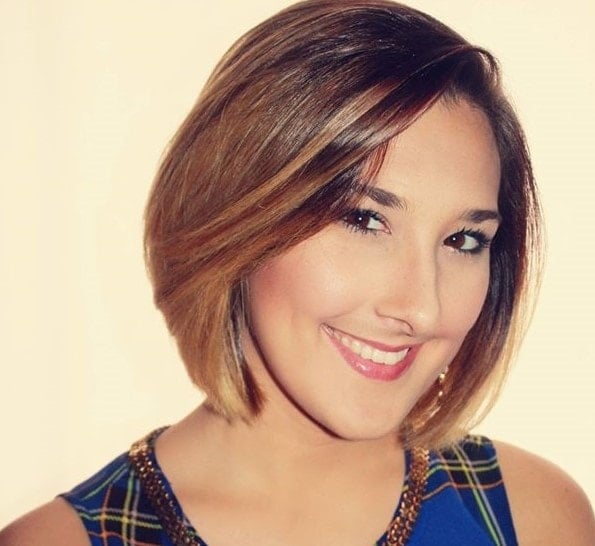
Posted on Feb 27, 2017 in Collaborative Robots, Robots, Safety
3 min read time
As the world’s population continues to grow, and the demand for technology rises, manufacturers have larger orders to fill than ever before. Efficiency is key, which is why many are turning to modern robotics to improve their overall production rates. It’s an excellent solution to a complex problem, but it’s not without its fair share of challenges.
Let’s take a look at three challenges that manufacturers are facing today when implementing robotics, and what solutions are being used to combat these issues.
3 Challenges Manufacturers Face With Robotics (And 3 Solutions)
When we think of robots in manufacturing, some of us will recall the traditional fenced robotics that were efficient, if a little simple. We have moved past these into new and exciting fields of technology that offer even better solutions than ever before.
Here are three challenges manufacturers will commonly face when implementing robotics, and how the industry is solving them:
1. Skillsets and Experience
There’s a growing gap in the skillsets of workers in the manufacturing industry. In a study done by Accenture, it was found that 75% of manufacturing companies reported a shortage of skilled workers that required more than a high school diploma.
As baby boomers get older and retire, there’s a growing need for people to replace them, but you cannot simply give people the skills needed to replace these jobs. However, you can give them to a robot.
Enter Sawyer, the solution being sold to countless manufacturers by Rethink Robotics. Sawyer represents one of multiple solutions in the field of collaborative robotics. Among many other things, Sawyer is able to learn and perform complex tasks by having a human counterpart guide Sawyer through the process. After this demonstration is complete, Sawyer is able to perform the task with ultimate precision.
This is thanks to the Intera software that features the iconic "face" screen, which helps Sawyer communicate better with coworkers. The software has the top "train-by-demonstration" user interface that allows teaching Sawyer to be so simple and intuitive.
This training is quick and efficient, and unlike a person, Sawyer won’t forget. By implementing collaborative robots into the manufacturing process now and letting them learn from their human counterparts, we can effectively combat the skill gap and fill those jobs that are being abandoned by retiring individuals.
2. Cost of Technology
Purchasing robots outright can be an expensive venture for large manufacturing companies. Even small ones may not be able to sustain the cost. To combat this, a new wave of companies are offering robotics as a service.
The concept involves renting the robots for a decreased rate than simply buying them outright. In this way, companies can quickly and effectively implement robots into the workforce and still stay within budget. There are also companies who offer modular solutions which allow manufacturers to spend only what they need.
Here are some examples of these types of companies currently being utilized:
- ABB Ltd - a robotics company that offers a wide variety of robotics and modular manufacturing systems.
- Fanuc Corp - A company that offers flexible solutions for manufacturers both large and small.
- Sterraclimb - a service robotics company that makes a robot capable of lifting heavy items and climbing stairs on its own.
3. Safety Concerns
Our final challenge is the safety of human workers when working with robots. Fenced robotics are usually isolated from human workers for this very reason. Thankfully, the robotics industry is answering the call once again with collaborative robots that are equipped with a wide range of safety features.
The four main focuses of collaborative robotics companies in regards to safety are the following:
- Stopped state monitoring - the ability to stop working when a human enters a specific area and resume working when the human leaves.
- Speed and separation monitoring - Slows down or stops depending on the distance of the human in question.
- Hand guiding - The ability to know when a person is in contact with the robot for guidance and training.
- Power and force limiting - Sensors and technology that restricts the amount of force applied. These include mechanical solutions, electrical ones, and elastic actuators.
Today’s mainstream collaborative robotic solutions are power and force limited, to make them safe for setup and use along humans.
Final Thoughts
The rise of collaborative robotics and robotics as a service is solving many of the challenges that manufacturers face when trying to implement automated solutions. What challenges have you seen in your industry and how has robotics solved them? Let us know in the comments!
Leave a comment