Want to Produce Locally? Reshoring Is Easy and Thriving
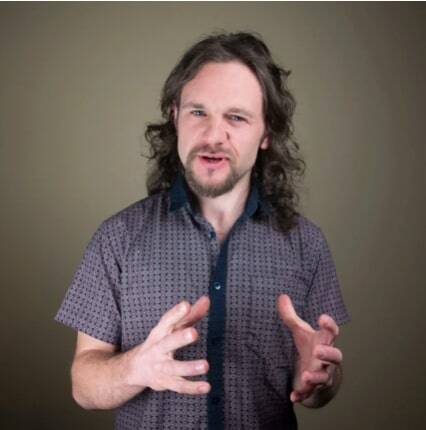
Posted on Nov 07, 2019 in Automation
5 min read time
The offshoring bubble appears to be deflating. Now, more than ever, businesses are looking for ways to move operations locally. Here's why they're doing it.
Offshoring has been increasingly popular over the last 20-30 years. By "offshoring" I'm referring to the practice of moving manufacturing and other business processes from the country where a company is based to a country with lower labor rates.
Over the last 20 years, the practice of offshoring has become ubiquitous in many industries thanks to its competitive benefits. For example, back in 2001 — when Stanford University investigated The Economics of Offshoring in the Software Industry — the most common reasons for offshoring were to reduce costs, to allow companies to focus on their core competencies, and to improve product quality.
Things have changed since the early 2000s. Over the last few years, offshoring has become less and less attractive in a world where sustainability, innovation, and "buying local" are much higher on customer's agendas than ever before. As another change, local production is now often synonymous with quality.
According to a report by the World Economic Forum published in June 2019, there is a rise in "automated microfactories." These are small factories with high levels of automation. They are based locally and are fueling the “think global, build local” approach to manufacturing.
Do you want to benefit from this trend towards more local production? It's easier than you might think.
Is this goodbye to offshoring?
Like almost every economics-related trend throughout history, the practice of offshoring appears to have grown and grown in popularity… until it has become unsustainable and the trend has "flipped."
Some commentators have termed this the "offshoring bubble."
While it doesn't seem that the bubble has burst exactly — at least, not in the same way that housing bubbles often burst or the banking bubble burst in 2008 — the offshoring bubble does seem to be deflating.
According to a 2013 special report from The Economist, the rising practice of "reshoring" (the opposite of offshoring) means that manufacturing is starting to "come full circle" — companies are bringing operations back home that they had previously moved offshore. The report cites firms like Google, Apple, General Electric, Caterpillar, and the Ford Motor Company, which are all moving operations back to their home country following offshoring.
Offshoring is still happening, but its popularity appears to be waning. The percentage of companies looking to reshore their manufacturing rose from 9% in 2009-11 to 19% in 2012-14, whilst companies looking to offshore operations fell at the same time.
Part of this reduced popularity is caused by the political effects of offshoring. As the report says "Offshoring has brought huge economic benefits, but at a heavy political price." For example, local unemployment increases when a large corporation moves thousands of jobs offshore. This can harm the reputation of these companies.
Also, various "low-labor rate" countries are no longer the cheap sources of labor that they once were. For example, as the report states "China is no longer seen as a cheap manufacturing base but as a huge new market." We mentioned this on the Robotiq blog over four years ago concerning robotics.
Offshoring vs nearshoring vs outsourcing vs onshoring vs reshoring
There are a lot of terms that you need to get your head around when we're talking about "offshoring vs local."
Here's a quick comparison of the different terms:
Offshoring
Offshoring is the practice of moving some of a business's work and/or processes abroad.
In general, offshoring means moving work to countries where labor costs are lower than in the home country. However, technically offshoring can be done to any country.
Nearshoring
Nearshoring is a specific type of offshoring where the country is close to the business's home country.
The classic example of this is when a business in the USA moves manufacturing to Mexico, other parts of Central America, or Canada. The operation is not entirely local, but it is more local than sending the work to the other side of the world.
Outsourcing
Outsourcing simply means contracting work out to an external supplier. It doesn't necessarily have anything to do with offshoring as it is often done in the business's home country.
Offshored work can be either outsourced or not. For example, a business could set up its own manufacturing plant in another country. This would be offshoring but not outsourcing as the work is not done by an external contractor.
Onshoring/reshoring
The terms onshoring and reshoring both refer to the same practice. They are the exact opposite of offshoring.
The report from The Economist explains the concept of reshoring like this: "Many American firms now realise that they went too far in sending work abroad and need to bring some of it home again, a process inelegantly termed "reshoring"."
Inelegant or not, that's what the terms mean.
How automation can help you to produce locally
There are various advantages to moving your manufacturing operations more locally, including full control of the product, higher product quality, and competitive advantages. With collaborative robots, it's often very easy to achieve. You can now automate tasks at almost every stage of manufacturing, all the way from machining blanks (as in the example below) right up to collaborative robot finishing (e.g. sanding and polishing).
A wonderful example of how easy it is to implement local automation instead of offshoring comes from Lowercase, an American eyewear manufacturer whose story you can find in our Case Study Library.
When they started the company, friends Brian Vallario and Gerard Masci wanted to break a long-established trend in US eyewear manufacturing. Most brands, they explained, sell spectacles which are manufactured overseas. They wanted to make a product which was different from the rest. Part of their competitive advantage was by using the "Made in USA" label.
With the help of Axis New Jersey, they deployed a machine tending application with a Universal Robot in just 5 days despite having no experience with robotics beforehand. They are now able to handle their 17 different eyewear styles using the same machining process. This allows them to focus on more valuable tasks in the business, like new product design and handling orders.
As co-founder Brian Vallario said to us:
"Being such a small shop, every set of hands counts. There's so much that we're taking care of on a daily basis outside of the actual machining that [the robot] is a really big help."
The trend towards more local microfactories, like that of Lowercase, appears to be a sign that the offshoring bubble is deflating.
Which business operations do you currently offshore and how could reshoring work for you? Tell us in the comments below or join the discussion on LinkedIn, Twitter, Facebook or the DoF professional robotics community.
Leave a comment