Vision System Applications and Alternatives
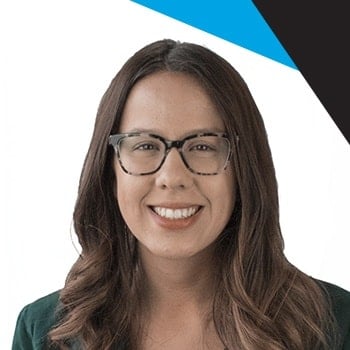
Posted on Oct 31, 2016 in Vision Systems
5 min read time
If you’re confused about whether or not a vision system is the way to go to accomplish your project, you are at the right place. Check out these alternatives.
Pick & Place
The key aspect in a pick and place application that is likely to influence your decision between using a vision system or another option is usually part presentation. You need to locate the parts in order to let the robot know where to pick them up. Below are some options that will solve part localization for pick and place applications. Note that here we are talking about the pick position, but the same factors apply to the place position. Depending on what you need to do when placing your part, you may need a vision system to determine the proper position also. BUt first, take a look at this pick & place challenge on DoF.
Fixtures
Your parts are placed in trays or secured with fixtures, so they are always at a constant position relative to the robot. This is usually really simple to do and program. You simply need to teach the positions to the robot. Some robot models come with palletizing programs that will help you teach positions fast. If you already have this kind of setup, then using vision is probably overkill. If, however, you don’t have such a system, then consider the following: designing a fixture can be costly. Also, fixtures can get tricky to design if you want to feed a lot of parts to the robot without recharging the jigs. In this case, you need to be able to place as many parts as possible within the robot’s reach. Another downside to this is if you have several different parts that have to be picked by the robot. In this case, you may need several different jigs which would therefore add to the cost, plus you should consider changeover time when you are estimating the efficiency of the system.
Bowl Feeders
These are meant to take bulk items and singularize them such that one part at a time would be presented to the robot and the robot would always pick this part from the same position. Once a setup like this is installed and adjusted correctly, it usually works great. You only have one pick position that you need to program into your robot to pick up the part. However, this type of equipment can be quite expensive and hard to adjust depending on the shape of the parts you are picking. Furthermore, with a bowl feeder most of the time you are stuck with the option of sorting only one kind of part. Switching between different parts will require you to add another bowl feeding system to your robot cell.
Conveyors
Conveyors can be a good option for part presentation. However, if you want to use a conveyor without a vision system, you need to have a datum line or point of reference that your part will rest against such that you will always pick that part from the same position or location. In this case, you will still probably need a presence sensor to let the robot know when the part has arrived at the picking location. Once it does, some robots have an option that allows you to pick the part while the conveyor is moving, otherwise you may have to stop the conveyor during picking and start it once it’s done. If you don’t have a datum line or the parts are not always in the same position or at the same spot on the conveyor; you will probably need a camera to locate the part on the conveyor.
Vision Systems
This option is commonly used to find a part’s location and orientation. There are many different ways you can use a vision system to accomplish part recognition. You can simply have the parts rest on a surface and have a 2D camera locate them. You can also have parts constantly moving on a conveyor with a fixed or robot mounted camera that can locate the parts. Or you can have the robot do a 3D scan of a surface and search for parts. All of these options have pros and cons. Some may work for what you need while others won’t. So if you feel that you need some guidance on how vision might apply to or improve your application, get in touch with an expert who will be able to help you out. Vision is a good option if you are often switching parts.
Quality Control
Quality control is another major key aspect that can be improved with automation for almost all manufacturing processes. The first thing you need to do is identify what aspects of the part you need to look at in order to say whether the part is good or bad. Then by looking at the different vision algorithms, you will be able to see which visions systems match your needs and can perform the quality inspection task you are looking for. Of course, there are alternatives to using vision to perform quality checks. We have listed some options and compared these to the use of a vision system.
CMM or Coordinate Measuring Machine
For example, if you have a part coming out of a CNC machine and you want to validate its dimensions. The most common system used is a CMM. In this case, the system touches different surfaces on the part to measure it. Usually people will be searching for CMM machines with an accuracy of approximately 0.25mm. If you want to reach this level of accuracy with a vision system, for the moment it is pretty difficult and probably overly expensive. Let’s assume that you need at least 3 pixels to cover the accuracy value of 0.25mm and that we have a 150mm x 150mm field of view which is large enough to cover the part. You would need approximately a 1800 X 1800 pixel camera to do the job. And this does not take into account any lighting challenges that may come with the images of shiny metal objects coming out of a CNC machine.
Eddy Current
This technique can be used to detect a part’s position and its defects. Due to its high sensitivity, you will be able to detect small cracks, deformities, pits, etc. However, using eddy currents are limited to conductive materials whereas using a vision system is not.
Vision
If you are on a production line where products are coming out on a conveyor and you simply need to check part presence and do some measurement analysis without extreme precision, then vision will be the best option. This is because the camera is able to take a snapshot of the part as it is moving on the conveyor. Thus you could perform live quality checks on the part without having to remove it from the production process and instead of doing batch sample testing. You are actually testing every product coming down that line.
Learn more on how to integrate vision systems for collaborative robots by downloading our brand new eBook. You will acquire basic knowledge of machine vision to help you figure out exactly what a simple vision application is. It might also be useful to understand the differences between this type of application and a more complex one. So, if you are just starting with vision, or if you think adding vision to your system might solve one of your pet peeves, this eBook will be a great place to start.
Leave a comment