Top Three Causes of the Manufacturing Skills Gap
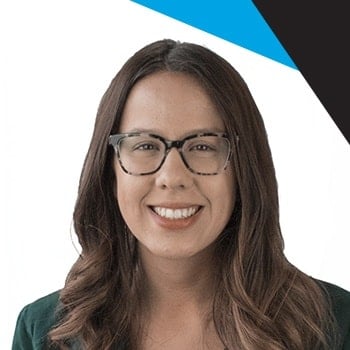
There are three commonly listed causes of the skills gap: Retirement of older workers, lack of skilled workers, lack of desire to work in manufacturing. Join us as we go through all three of these gap sources in detail and how to get rid of them.
Gap Source 1: Retirement of Older Workers
If it’s any consolation, manufacturing isn’t the only industry affected by widespread baby-boomer retirement.
In fact, its effects are being felt by the whole economy. According to a US Census report, “By 2029, when all of the baby boomers will be 65 years and over, more than 20 percent of the total U.S. population will be over the age of 65.”
You can’t stop people from retiring, of course, but that doesn’t mean there’s nothing to be done. You can make the most of their remaining time with your company, and possibly even inspire them to delay retirement.
Help Them Transfer Their Knowledge Before They Go
- Set up mentorships and training opportunities within the company to capture as much knowledge and industry wisdom as possible before it walks out the door with your most experienced people.
- Ask your top near-retirement-aged associates to share how they weathered different crises in the industry. This invaluable wisdom is hard-earned, and you don’t want younger people to have to re-learn these lessons the hard way.
- Have your seasoned professionals, especially if they were with the company in the 1980’s, share how they successfully managed technological changes over the years. For example, when computers were first introduced, were there any fears that turned out to be unfounded? How about unexpected benefits resulting from that technology shift? Sharing these stories can help others reduce their fear of change, and help newer managers see what works and what doesn’t when introducing new technology.
Convince Your Best People to Delay Their Departure
According to a 2017 Retirement Confidence survey, 1 in 4 workers aged 55+ say they expect to retire between the ages of 66–69. If you can encourage some of your top employees to delay retirement, you can take full advantage of those extra years.
Implement Incentives to Hold Off on Retirement
- Create flexible work arrangements, such as part-time hours and remote work.
- Allow phased retirement, or re-hire retired workers as independent consultants.
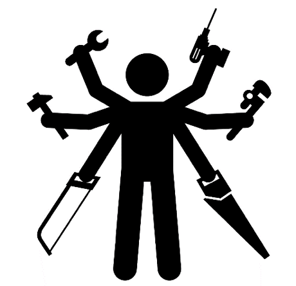
Major changes in traditional training and new skill requirements are contributing to the skills gap.
According to a 2016 CNN Money article citing Labor Department figures, the number of apprentice programs in the United States decreased by 11,000 from 2002-2015.
Additional Skills Required
The 2012 TalentLens/Pearson report, “Hiring Manufacturing Staff in the 21st Century: A fundamental Shift in Skills” says that “While sheer brawn and loyalty were once the primary predictors of success, new roles critical to today’s modern manufacturing facility (i.e., design, engineering, logistics, supply chain automation, etc.) demand that successful employees bring much more to the table.”
Soft skills such as teamwork are also in demand. In the 2016 Workforce Statistics for Miscellaneous Durable Goods Manufacturing provided by the Bureau of Labor statistics (BLS), the occupation “Team Assemblers” had ten times as many people as “cutting, punching, and press machine setters, operators, and tenders, metal and plastic.” BLS describes the Team Assemblers occupation as “Work as part of a team having responsibility for assembling an entire product or component of a product. Team assemblers can perform all tasks conducted by the team in the assembly process and rotate through all or most of them rather than being assigned to a specific task on a permanent basis.”
Demand for Mechatronics Knowledge
According to an April 2017 white paper from the Association for Advancing Automation, Work in the Automation Age: Sustainable Careers today and into the future, “New job titles for traditional roles such as machinists, welders, coders, and technicians often incorporate the term ‘mechatronics’ to reflect the need for technical training that includes systems design as well as mechanics and electronics.”
To work in manufacturing, you need all three: trade skills, soft skills, and technical skills.
Skills Needed
- Trade skills – traditional skills used in manufacturing and production that are often learned through apprenticeships.
- Soft skills – teamwork, critical thinking, and flexibility.
- Technical skills – the ability to work with and troubleshoot automated processes.
Gap source 3: Lack of Desire to Work in Manufacturing
The Manufacturing Institute/Deloitte 2015 skills gap study states “Adding to manufacturers’ challenges to fill jobs is the issue of overcoming industry perception… While Americans consider manufacturing among one of the most important domestic industries for maintaining a strong national economy, they rank it low as a career choice for themselves.”
This problem of perception is largely based on outdated information.
What CAN be Done
✓ Raise the profile of your company in a positive light.
✓ Open your doors to students, your community, and the media to show what it’s like to work in manufacturing today.
✓ Share current statistics about career opportunities in manufacturing.
Get the eBook exploring the skills gap, with a focus on solutions and strategies to close and fill the gap. We’ll explore the answers to questions you might have right now.
Leave a comment