Short on Workers, High on Costs? Deloitte Says Automation May be the Answer
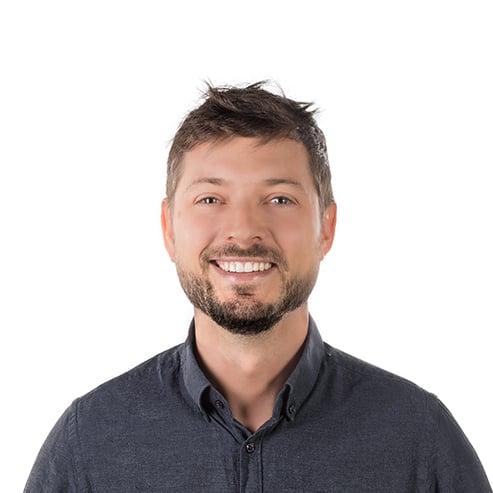
Posted on Feb 12, 2025 in Automation
2 min read time
Manufacturing is at a crossroads. Labor shortages are growing, costs are rising, and the pressure to stay competitive has never been higher.
Forward-thinking manufacturers are already leveraging robotic solutions to bridge labor gaps, boost efficiency, and drive profitability. The question isn’t if automation will reshape manufacturing, but how fast companies can adapt to stay ahead.
Image source: Deloitte
Labor Shortages and Skills Gap
Is your company struggling to hire and retain the skilled workers you need? If so, you are certainly not alone. The manufacturing sector is experiencing a significant skills gap, leading to a substantial number of unfilled positions.
Deloitte projects that between 2024 and 2033, there will be a net need for approximately 3.8 million new employees in manufacturing in the US alone. Alarmingly, around half of these positions—1.9 million jobs—could remain unfilled if the skills and applicant gaps are not addressed. These trends are similar in other industrialized nations globally.
Cost of Employee Turnover
As if hiring qualified employees weren’t hard enough, manufacturers are also dealing with high turnover rates and the associated costs. 60% of respondents indicate that the average cost to replace one skilled frontline worker ranges from US$10,000 to US$40,000, while 56% say that employee turnover has a moderate to severe impact on their bottom-line finances.
Aging Workforce
An aging workforce exacerbates labor challenges. In the United States, more than 2.6 million baby boomers are expected to retire from manufacturing jobs over the next decade, further shrinking the labor pool. Beyond that, decades of experience and knowledge will exit the industry as older workers leave the workforce, contributing to an ever-widening skills gap.
Enter Automation
Faced with the above challenges, what can manufacturers do to thrive in an uncertain environment?
Implementing automation addresses each of these situations simultaneously by:
- Improving Health and Safety: Automation reduces the need for humans to perform hazardous or physically demanding tasks, decreasing workplace injuries.
- Enhancing Productivity and Efficiency: Automation enables continuous operation without fatigue, leading to higher output and consistent quality.
- Reducing Labor Costs: By automating repetitive tasks, manufacturers can lower labor expenses and reallocate human resources to more complex roles. More appealing roles typically translate to lower turnover rates and associated costs.
By embracing automation, manufacturers can address current labor challenges and position themselves for sustainable growth in a competitive market.
Looking for some concrete examples of companies like yours who have solved their labor woes thanks to automation? Take a look at our success stories!
Ready to explore your automation options? Talk to an expert
Leave a comment