Practical Automation Strategies from a Global Food Industry Leader
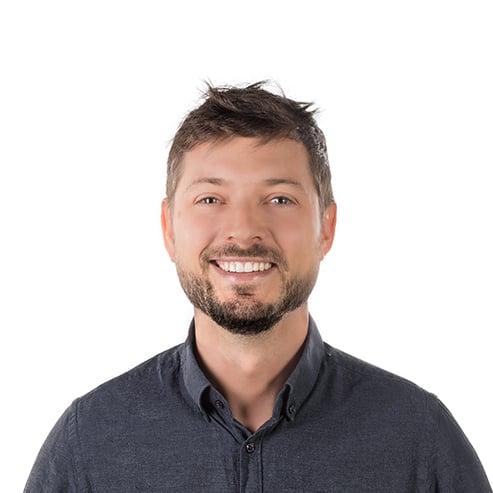
Posted on Feb 05, 2025 in Automation
3 min read time
For manufacturers, automation is no longer a luxury—it’s a necessity. But when it comes to automated palletizing, complexity can be the enemy of efficiency. In this exclusive conversation, John, a global director at a major food corporation, shares why his company is moving away from large-scale custom integrations in favor of modular, scalable solutions that deliver fast ROI and long-term flexibility.
Strategic Investment in Automation - Low-risk with quick cost savings
As businesses navigate economic uncertainty and rising interest rates, John emphasized the importance of prioritizing low-risk automation solutions with quick cost savings.
“High-risk, long-duration projects with potential for substantial gains are not our preference at the moment,” he stated. Instead, his company is focusing on end-of-line palletizing solutions that integrate seamlessly into existing workflows without requiring extensive reconfigurations—ensuring minimal disruption to downstream operations.
The Challenge of Engineered Solutions
John highlighted the complexities of engineered automation solutions, noting that while they are beneficial for high-volume production lines, they often require extensive customization that can quickly double the budget.
“Large, customized integration projects attract more scrutiny and opinions, making it harder to maintain simplicity and control over the project’s scope.” - says John.
The rigid nature of these solutions also makes future upgrades or modifications challenging, reinforcing the need for more adaptable automation strategies.
The Power of Modular & Incremental Automation
John’s company favours modular and incremental automation, which provides greater flexibility while maintaining efficiency.
“These solutions may have lower payloads and longer cycle times, but they are budget-friendly, low-risk, and designed to fit within existing operations without requiring major reconfigurations,” he noted.
By implementing smaller, quicker automation projects, his company can make better use of available capital, especially when larger projects experience delays. For a step-by-step guide on modular and incremental automation, check out our Lean Robotics Methodology.
Practical Advice for Companies Seeking Automation
When asked about selecting the right palletizing solutions, John stressed the importance of keeping it simple.
“Opt for standard, reliable, and robust solutions. Think of automation as an ongoing program rather than isolated projects. Remember, palletizing is about moving boxes— so don’t overcomplicate it.”
He advised companies to focus on quick wins and low-risk solutions to build momentum and confidence in automation.
Awareness & Adoption of New Robotic Technologies
John also pointed out that many businesses are still unaware of the accessibility of collaborative robots (cobots), which require less floor space and fewer infrastructure changes than traditional automation solutions. He cautioned against unnecessary project expansions driven by system integrators looking to increase scope and complexity. Understanding all available automation options and ensuring alignment with business goals is crucial for successful implementation.
The Evolving Narrative of Automation
John reflected on how the motivation for automation has evolved. “In the past, automation was often driven by fear of missing out. Today, it’s about cost savings, modernization, and workplace improvement, all while maintaining financial viability in a time of constrained capital,” he said.
His company’s strategy has shifted toward prioritizing numerous small, standardized automation solutions that deliver consistent savings and efficiency. In an unpredictable world, automation must not only reduce costs but also provide flexibility to adapt and thrive amid constant change.
Conclusion
John’s insights underscore a key message for manufacturers: automation should be practical, scalable, and focused on real efficiency gains. By choosing modular, standardized solutions, companies can ensure quick returns, maintain operational agility, and create a foundation for long-term success.
As automation continues to evolve, embracing smart, adaptable solutions will be critical for navigating today’s dynamic business environment.
Leave a comment