How to Integrate Your First Robot (Part 3/3 Lack of Technology)
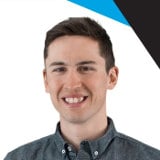
Posted on Jul 29, 2015 in Robots
4 min read time
As a wrap up of our past two blog posts on the different tools to use to integrate your first robot, the following article talks about the third point outlined in this series: The gap that exist between manufacturers according to the robotic technology they employ. In fact, as most people in manufacturing do not have a robotic background it might at first seem to be scary to get into this topic. But, here are a couple of tricks to close this gap.
1. Look around you
We are in 2015! Technology is evolving at a very fast rate. It is sometimes hard to keep up with all the new kids on the block in the automation world. It is a full time job just to be aware of everything that is going on in the market. With this being said, if you are not an insider it may appear daunting to find what you need for your process. You’ll want to start by becoming informed about the robotic market, what your different options are and what has already been done in surrounding plants (or what your competition is doing). Remember that some people dedicate their careers to developing automation systems, and that you cannot catch up to them in a couple of weeks. Just start from where they left off to make your life easier
I highly recommend going to your customers or suppliers that are already automated and ask for a little informative visit. They will probably be stoked to tell you what they did and how it works. Most important of all if they already have an experience in automation, they can probably give you tips or refer to you to websites or suppliers that can help you through your process.
2. Optimize your production (first)
The bottom line is…Can you change your product design to have an easier assembly and to eventually automate your process more easily? Since you are going to be in a redesign process you may want to start by focusing on small stuff on your product that can make a big difference in your assembly, like 'Can you use clips instead of screws'?
Small features such as screws and other fixing methods can be rethought. It's not because the casing of your product is fixed with fours screws that it cannot have the same mechanical properties with two or three. Doing so is not just increasing your automation potential it's also optimizing your manufacturing process and at the end of the day your productivity. Think about it, automating a process that is not optimized will not give you the most efficient results. Think about a lean production.
Another aspect of product design can also be packaging. For example, if your supplier takes an item and places it in a box and then you have to pick it up again to add a component to it, where that component may come from another subcontractor, well maybe it would be smarter if you sent the components down to your supplier, and they put it together when they are producing the product. Then you will not have to unpack it, rework it and then repack it. You might save a few steps here.
3. Funding
Budgets are always tight, so look into the different kinds of funding that can be available to companies to automate their processes. Depending of your region, you can search for funding from external organizations or directly from the government. You may even want to share R&D costs with other companies that have your same challenges.
4. One step at a time
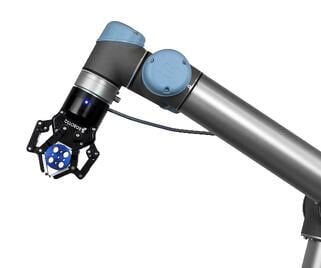
As I have said in the past, start small. If you are a pure manual shop and you want to automate your process, you may want to start small and take one step at a time. If applicable, use collaborative robots, these kinds of robots require fewer safety features and space. They can be a good first step into robotization. Starting with a full blown cell can sometimes be too much to handle and may result in difficulties or even failure, which might require reorganizing your project with cost delays and lessons learned. I highly recommend you start with a robot and a tool and see if you can do the job with this, if not, add on to it by introducing a vision system and other sensors to achieve your process.
I really hope that these tips helped and directed you to tools to automate your first manufacturing process. Introducing a robot in a manufacturing plant is a big move in terms of investment and process change. You really want to do it the right way to see the benefits automation can capture. We have launched an eBook on how to integrate a collaborative robot in a global company, if this is your case, you may want to take a look at it by clicking on the big button at the bottom of the page.
Related Articles
Leave a comment