How to Get Your Team on Board with Robotics
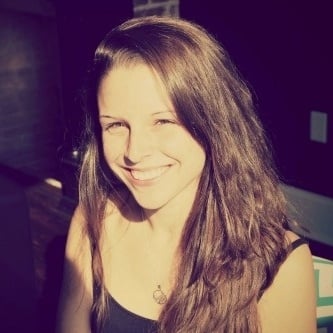
Until recently, most robots in the industrial sector were integrated into assembly lines in order to do things for humans. However, thanks to the surge of collaborative robots, things are changing. These new robots work with people and assist them with their tasks directly.
According to the International Federation of Robotics’ 2017 World Robotics Report, over 1.7 million new industrial robots will be in factories around the world by 2020. Companies worldwide are increasingly interested in exploring the potential of cobots.
A collaborative robotic cell at beyerdynamic's facility in Germany.
However, it’s understandable if your human workforce isn’t immediately receptive to the idea.
Many headlines about the rise of robots question whether particular jobs are at risk of being replaced by technology. That’s why it’s crucial to address these concerns before you bring in a robot.
Here are six things you can do to help your team embrace a new perspective:
1. Provide team members with straightforward information
If people don’t receive details directly from your company, they’ll likely jump to hasty conclusions. That's a recipe for spreading rumors and eroding morale.
Consider holding a few information sessions to inform people about why you're bringing in cobots, when you plan to implement them, and which safety features will be put in place.
Also, remember not to shut down communications once the first information session is over. The goal is to listen to employees and address their concerns fairly, so you should aim to have an open-door policy for anyone with further questions.
2. Focus on the benefits to employees
Statistics indicate that each year, nearly a quarter of the injuries suffered by manufacturing plant workers happen because of overexertion. Similarly, eight percent of all incidents involve repetitive motion. Cobots could help workers stay healthy by reducing the strain of their jobs.
When discussing robots with your workers, clarify that the type you’ll be using is made to work alongside humans, not replace them. Besides the advantages to well-being, you could also touch on how cobots augment people's speed and accuracy levels.
3. Reassure workers of your methodical approach
Your workforce is especially likely to be wary of cobots if it seems like management decided to invest in robots quickly without valid reasons for doing so. That’s why it’s smart to emphasize that the decision wasn't made lightly, and indeed involved a great deal of thought.
You might mention how robotics will help your company reduce expenditures. For instance, companies with robots have been achieving cost savings for years while keeping customer satisfaction levels high. If applicable, it’s also worth mentioning how your company considered different brands of cobots that offer various capabilities.
If it’s evident that the implementation of cobots is well-controlled and carefully thought out, workers should feel confident about the future.
4. Demonstrate cobot safety features in action
People are typically most afraid of what they don’t understand. With that in mind, take care to thoroughly introduce workers to the built-in cobot features that will keep them safe. These components often let humans anticipate cobots’ movements so they can understand how the cobots work with people to achieve shared goals.
Cobots usually respond to pressure, and slow down their movements when they detect humans nearby. If you can show employees how the safety features work, they’ll feel more at ease about working closely with robots.
5. Don’t be dismissive of fears
Despite all your efforts, some people may still be frightened of what’s ahead.
A study of more than 4,000 American adults found that 72 percent of people polled were either somewhat or very afraid of robots and computers that can perform human jobs.
It’s essential that you make yourself available to listen to the doubts people have about robots in the workplace. By showing that you care about and understand their trepidation, employees will see that you’re aware they’re uneasy and want to try and ease the uncertainty.
6. Remain open to feedback after implementation
Substantial changes in operations typically involve learning curves. There may be unforeseen issues that arise after you start using cobots, including shortcomings that can be very frustrating to workers.
Employees could become angry if managers simply install cobot technology and then "walk away" without offering employees the chance to provide feedback.
Remember to reserve time for testing the technology and training employees. Depending on factors like materials, production speed, and changing human roles, it may be necessary to show flexibility regarding the planned use of cobots.
By giving workers options for reporting the pros and cons of their experience with cobots, you’ll reap data that will be a huge help with making improvements in the future.
Getting people to embrace new technologies isn’t always easy. Luckily, with these straightforward tips, you can show your team how cobots will help — not hurt — them and their careers.
Leave a comment