How Difficult Is it to Implement Robotics Into a Manufacturing Plant?
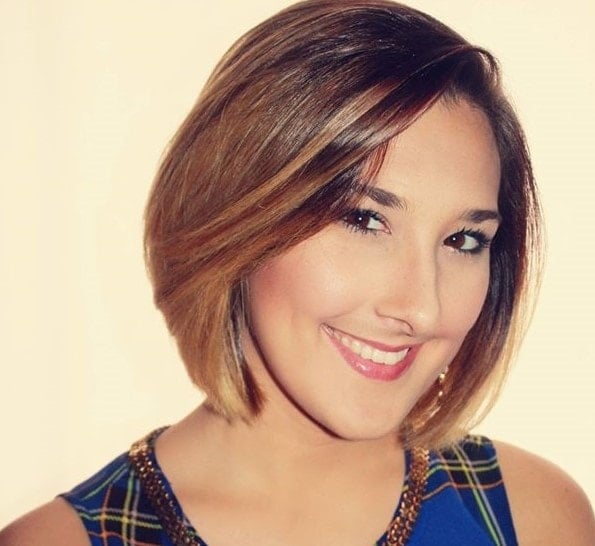
Posted on Mar 14, 2017 in Manufacturing
4 min read time
Robots are the way of the future. Multiple industries have embraced the power and efficiency that automation offers for their business and for their customers. No longer are robots in the workplace a part of science fiction. We still have a long way to go before they are as capable as a person, but the foundations are in place.
The time to implement robotics into your manufacturing plant is now, but perhaps you’re concerned about the difficulty of such an endeavor? Join us as we look at the simple checklist you should be using to show yourself and your employees the simplicity of implementing robotics into your plant.
Why You Should Implement Robotics Into Your Plant
The biggest obstacles that manufacturers foresee when they’re looking to implement robotics are things like these:
- Cost of integration
- Training
- Return on Investment (ROI)
- Safety
- Feasability
These concerns are natural, but unwarranted. Today’s solutions address all of these concerns, and it’s clear that many manufacturers are seeing this. A recent survey found that a majority of manufacturers in the US plan to implement robotics in the next 2-5 years.
This same survey found some interesting motivators behind the decision to implement robotics:
- 54% said they plan to add $1 million or more into their budget for advanced manufacturing.
- 49% of smaller companies plan to add $100-200K
- 78% said innovation was a major motivator in their desire to implement new technologies.
Manufacturers are seeing that the addition of robotics offers the ability to expand, increase efficiency, handle more requests, increase the overall quality of their output, and it represents a major leap forward in innovation.
Let’s look at three simple considerations you need to look at before you’re able to implement robotics into your manufacturing plant.
5 Simple Considerations to Implementing Robotics Into Your Manufacturing
Today’s automation solutions for manufacturing are wide and varied. They are also tailored to a wide variety of business and skill levels. Implementing them is a lot easier than you would think. Here are three things to consider:
1. Room on the Floor
First things you’ll need is space. Prior to ordering robotics or equipment, find out the exact dimensions that you’ll need and measure these on your plant’s floor to ensure everything will fit properly.
It’s important to look at more than just the base of the machine’s size. Consider the reach it has and how much space it will need to fully function when you’re doing your measurements. Consider space for other machines or workers as needed.
2. Additional Power Requirements
The second things to consider is the power you will need to make the robots function properly. While it’s easy to assume you have the extra electricity from the power grid to install these robots, you should absolutely check.
Take a look at your power grid’s consumption versus the amount you have to work with. Follow that up by looking at the power needed for the additional robotics. You may find that you need temporary generators to keep everything running, but don’t fret.
In many cases, the increased production from robots will give you the opportunity to expand your own efforts and ultimately increase the power grid in your plant to further accommodate this new technology.
Keep in mind, that this applies to non-collaborative robots. Many of today's modern solutions in the collaborative field use standard electrical sockets, and therefore don't consume much more power than a computer would use.
3. Employee Training
Your employees will no doubt have concerns about switching over to automation. They will need to know how these new robotics work and what features are in place to ensure their safety. Thankfully, many robotics providers also offer training courses for employees who will be working alongside the robots or working in partnership with them if they are collaborative models.
Additional education and knowledge is important for employees as it empowers them to not only understand their robotic colleagues better, but it also gives them opportunities to grow and contribute more to the business.
4. Designing the Cell
At this point, you will need to help the application engineer understand the space and product flow needs for the robot. The goal is to minimize the robot's overall space usage, while still allowing access for operators, materials, forklifts, and so on.
From here, the application engineer will conceptualize both 2D and 3D models of the system's layout and integration in the factory floor. All levels of employees, from operators to management, will contribute information to help bring the project to fruition.
They key here is to keep communication lines open. Everyone should understand the potential conflicts that will arise in both opinion and logistics. Ultimately, keeping things open will ensure that the project moves smoothly.
5. Budgeting
Our final consideration is perhaps one of the most important. When planning out implementation of robots, you'll need to communicate with all levels of the plant, including the employees, to understand how it will affect the current budget.
It's important that you do this early in your planning, as it will directly affect everyone in the company. By respecting the budget and passing communication down through the levels of your employees, you can ensure that everyone is on the same page.
Final Thoughts
Robotics in manufacturing is an excellent matchup. As technology continues to evolve, we’re seeing major leaps forward in how robotics can improve every aspect of your business. What experiences have you had transitioning to robotics? Let us know in the comments!
Leave a comment