How CRUM Mfg Saved 20 Hours/Week with Robot Palletizing
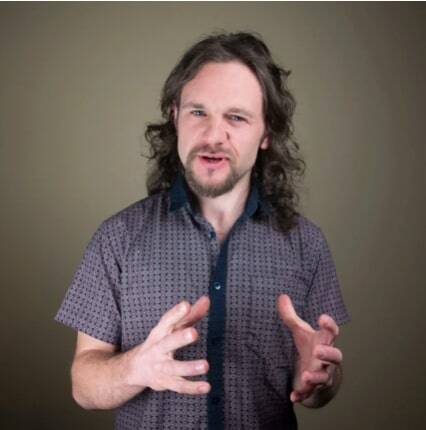
Posted on Jan 04, 2022 in Case Study
7 min read time
Manual palletizing is a very common problem for manufacturers. Integrator CRUM Manufacturing sees many companies struggling to manually palletize efficiently.
One such company came to CRUM Manufacturing with a problem…
A customer came to CRUM Manufacturing with a palletizing problem
CRUM Manufacturing is a Universal Robots-Certified integrator of automation solutions based in Waterville, Ohio, USA. There are two divisions of the business: a manufacturing side for the automotive industry and their automation side.
Kyle Heitmeyer is a controls engineer at CRUM. He explains:
"For the automation side, we can automate whatever our customer truly needs. Whether it is palletizing, machine tending, or creating new quality check fixtures, if a company wants something automated, they come to us and we design, build, and integrate those systems."
One customer came to CRUM with a problem. They needed to automate the palletizing of their product boxes.
Kyle says:
"Most companies don't have a dedicated palletizer or person to palletize. They're running one line and when they have a some downtime they try to hurry up and load a few boxes on the pallet. It's not efficient.
"Also, most companies struggle to integrate some sort of manual or hydraulic turn/lift table themselves for ergonomic reasons. It's a problem that people are still trying to solve."
The Task: Palletizing and several pre-processes
As an integrator, CRUM is often called in to deploy robotic applications that are more than just "out-of-the-box."
There are typically extra "pre-processes" that can add extra complexity to the task. For this customer specifically, the palletizing task involved several processing and verification steps in addition to putting boxes onto the pallets.
The pre-processes for this customer's task were:
- The boxes came down one of two conveyors.
- The robot needed to pick them up.
- A weighing process was used to validate each box and test its weight.
- Then, the box was placed on a fixturing point.
- A custom label was produced by a printing machine.
- The robot needed to take the label and stick it to the box.
- Then the robot would palletize the box.
There was added complexity as the customer was using recycled pallets so the pallet heights weren't always consistent. The customer needed a way to easily handle batches of different height pallets without having to call CRUM to reprogram the system. This meant that the programming needed to be very simple.
How CRUM would have solved this problem in the past
Before the Robotiq Palletizing Solution came on the market, palletizing with a collaborative robot wasn't always easy.
In the past, Kyle had integrated other palletizing applications using a Universal Robot.
He explained how challenging it was before:
"With one deployment, we had the pallet itself on a turn/lift table. So we were able to place three layers of product at one height, but we were only able to reach half the pallet.
"First, we'd finish one half of a layer, we'd rotate the table, and then do the other half of it. After the first three layers, we'd drop the pallet down and start at the same height where we originally started for Layer 1. When rotating, you need to consider the speed and acceleration because you don't want the boxes to fall over when the table is in motion.
"The system did work but the mechanical engineering and design added a lot more time. Also, the programming was more in-depth and not as user-friendly for the customer."
An exciting new palletizing solution arrives on the market
For this new customer, Kyle had the opportunity to try out a new palletizing product that had just come on the market.
He describes how he came across it:
"A distributor notified us that Robotiq had a new product coming out. They had a demo unit at their facility. We were able to go down there during that time, check it out, and I could test the program.
"The ease of the setup was the selling point for us. With Robotiq's palletizer system, their built-in URCap for Universal Robots really made it easy to set up. It also gives you some flexibility to tweak the system to fit your current scenario because not everything will be an out-of-the-box scenario."
Pro-tip: Get your hands on the robot as soon as possible
Whether you are an integrator yourself or you just want to use robotic palletizing in your own facility, Kyle has a pro-tip for you…
He explains:
"My advice is to do your research and see examples of it working. Make sure you feel comfortable that this solution will work for you.
"If you have an opportunity, get your hands on the robot or view a video demonstration. For me, as a controls engineer, that was a big thing. Any time we bring in a new product, we have the weigh the benefits it could provide with the learning curve that it might bring to us.
"With this solution, I could see how easy it really could be to set up. And it let our mechanical engineer see how much he doesn't have to worry about. Just being able to get our hands on it helped us a lot to make the decision to move forward with the Robotiq solution."
The little steps that make a robot deployment challenging
For this application, the little tweaks that Kyle needed to make were vital for the success of the task. These were the steps relating to those pre-processes we mentioned above.
Kyle says:
"The palletizing portion was the easiest part of it. The hardest part was weighing and labeling the boxes. But, the palletizing was simple."
"With the available seventh axis in Robotiq's system, we were able to add the pre-processes as well as the palletizing itself."
One obstacle he encountered was that the customers' boxes needed to hang over the pallet about half an inch on each side. This is not an out-of-the-box feature of the palletizing solution.
Kyle explains that Robotiq support was instrumental in helping him to get past this challenge:
"Robotiq were very helpful. They seem very caring about making sure their product does work for the company and they're there to assist you all the way through.
"When I had questions about programming, I got put on with one of their tech support. He was very attentive with all of my questions and answered them very quickly. Kendra, our account manager, would also reach out to me and make sure nothing else popped up."
The solution to handling the box overhang?
Kyle explains how they overcame the challenge:
"We added a spacer to automatically offset the pallet. So we were able to make the pallet just a little bit wider to cheat the system. But, the flexibility of the programming is what made that possible.
"Kendra from Robotiq had another customer with the same problem and they were trying to find the solution for it. I shared what we did with her, which helped them. It definitely helps that we're an integrator because we see a lot more out in the field than the average person."
How long does it take to deploy robot palletizing?
A concern that many companies have when they start using automation is that the deployment will take a long time.
This is one of the advantages of using an out-of-the-box solution. Deployment can take just days or weeks instead of months.
Kyle explains how long a simple deployment of the palletizing solution would take in a customer's facility.
"Usually with projects like this, we can order the palletizer immediately after receiving a purchase order from our customer. Upon receiving the unit, we could probably deploy it in 2 weeks if it's just a palletizing process with no pre-processes.
"I'd say that we could probably have it up and running in a couple of days, but we like to run the system hard to debug it prior to giving it to the customer. You more or less want to try to "break it" before you give it to a customer, is how we usually describe it."
The result: Saving 20 hours a week for just one task
What has been the impact of the palletizing solution on the customer's line?
Kyle says:
"I think it's saving them about 20 hours a week, of two operator's time: for a first and second shift.
"Also, it's just one less thing they have to worry about. Before, it was one of the line leads that had to take care of it. Instead of being able to watch something else, they had to walk away and take care of the palletizing.
"It really allows a customer to take ownership of their system, which is our goal. They feel comfortable enough that when small changes happen, they can program the changes themselves."
And what does the customer think of the Robotiq Palletizing Solution now that it has been in production for some time?
Kyle adds:
"I've reached out to the customer a couple of times, just to check up. They said it's probably one of the best automation systems they have in their facility. And they already have at least 8 systems there — 4 cobots and 4 industrial.
If you would like to see what the Robotiq Palletizing solution could do for your business, check out our product page or get in contact directly.
What questions do you have about robotic palletizing? Tell us in the comments below or join the discussion on LinkedIn, Twitter, Facebook, or the DoF professional robotics community.
Leave a comment