What Should be the First Collaborative Robot Application in Your Factory?
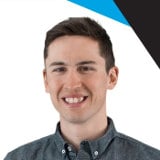
Posted on Jun 09, 2015 in Collaborative Robots
4 min read time
You are now convinced of the potential of collaborative robots to increase the productivity in your factory and maybe even beyond within your global enterprise. Now you need to identify that first application to get things going. What should it be to make sure it is a successful step leading toward even more successful collaborative robot integration? Here are some steps to guide your choice of the first application and some ideas to leverage that first success.
1. Find a Simple Process that a Collaborative Robot can do and that People don't Like to do.
Looking at your plant layout and workers’ operations, you have probably determined a couple of spots that you think would be great candidates for the introduction of a first collaborative robot. To rank your top application(s) you can look at the following aspects.
- Get the people on your side: You should focus your energy on jobs that are dull, dangerous, repetitive, or have ergonomic problems, basically the jobs that nobody wants to do. If most of the time, no one is very motivated to do them anyway; everybody will give you a hand on finding a solution.
- Understand the robot capabilities and limitations: Can this job be done by the robot? Even if you don't have a huge robotic or automation background, you can judge the do-ability of certain applications. Keep in mind that certain applications have a proven track record, these are mainly automated with collaborative robots. They include: pick and place, machine tending, dispensing and packaging. Most of the time, these tasks involve simple motions and do not require too much programming, sensing or force control. This is really where you want to begin your collaborative robot process. Make sure to document the potential process. How are the parts presented? What do they look like? What needs to be done with them? Take photos and videos of the current scenario. This can give you ideas and can be helpful later to show before & after, as well as to share the knowledge you’ve gained with colleagues within your plant or more globally in your corporation.
- Start Small: KISS applies here “Keep it simple, stupid”. Find a stand-alone application that does not need integration of sensors and communication with other machines or conveyors. Never underestimate the time and complexity of integrating machines together: It always takes longer than expected, especially the first time! Find an application that you can do with simple part presentation on a tray, using only the robot and an easy to use end effector. If you realize that at some point you need something different, then add it. Do not start with a bunch of different tools or a complex vision system that you may end up not even using.
2. Make Sure it's Safe
Once you have identified your application, you will have to figure out if it is safe enough to be done in your plant. Even if the cobot arm is considered ''safe'' or collaborative, this doesn't mean that your application is automatically safe.
- Risk Assessment: Just like any other machine that you install in the manufacturing workplace, you must do a risk assessment. If you are working in a big factory, you have probably already done risk assessments for other machines. In this case, it is a bigger concern since a cobot is normally used without safety guarding. This means that humans are exposed to the movement of the robot and the consequences of what comes with this. So even if the collaborative robot is certified as ''safe'' to work alongside humans, if it carries a sharp knife... it suddenly becomes dangerous and needs to be guarded. If you can do a ''pre-risk assessment'' before introducing the robot, this will give you an idea of whether or not a cobot can be successfully introduced into your factory with relative ease.
- Refer to Standards: Safety standards are a very regional thing. People in Germany do not use the same norms as people in the United States or people in Canada. Even if we share a lot of things in common, little exigencies are required by each individual legal system. So it is critical to make sure to follow the required norms and regulations in your region. However, if you are working in a global company that has several plants everywhere on the planet, you may want to use the most stringent norms to build your robotic cell. By doing so, you can export the cell to any other plant worldwide and hopefully very few things will then need to be switched.
3. Leverage your First Collaborative Robot Success
This first installation will be a great learning experience that will come with some challenges. On top of the productivity gain, this knowledge gain is just as valuable for your company. Make sure to document it and to share the information.
- Bullet Proof: Make sure to build a first collaborative cell that is fully trouble free. In fact, if the goal is to export the cell to other plants you want to have solved every single problem that could potentially happen with the robotic cell. Keeping in mind that people will probably call you to ask questions about different types of problems, you really want to be ''bullet-proof'' and know the most you can.
- Success Story: Other plants in your organization will listen to the guys in engineering on how to introduce collaborative robots, but they are even more interested in how well their peers succeeded in practice. People often want to see real world examples of what has been done and what they can do on their side. Document your integration with before and after pictures, as well as videos, Q&A, plus metrics. Explain how this first experience will lead to other implementations in your factory.
- On the Floor: Now that people on the workfloor have a better understanding of the benefits and challenges of using a robot, ask them where they would introduce the next robot. Provide innovation/suggestion cards so they can submit their ideas. Use resources (interns are great for that) to try out the most promising ideas, showing that you listen to people while building your internal knowhow on applications. Put the people who submitted great ideas under the spotlight so they get the recognition they deserve. Again, keep before + after pictures, videos plus notes of all applications so you can share them globally.
Using these few tips can probably lead you to a successful integration of your first collaborative robot in your factory and leverage that effort. This is good for you, your colleagues and your company!
Leave a comment