Can I use the FT300 to reach safety requirements?
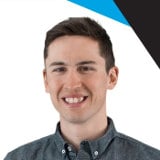
Posted on Feb 21, 2018 in Collaborative Robots, Robot Sensors, Safety
4 min read time
We get a bunch of questions on our products, their versatility, if the product can do this and that… The truth is our products are made to be versatile, allowing the user to do several applications with a single program. As for the FT300 Force Torque Sensor, one thing it cannot do is to ensure safety of its user. And here’s why.
The FT 300 is safe to use, but should not be used for safety
Let’s just make a quick recap on the normal use of a force torque sensor. Such tooling are used to detect force at the robot wrist. It is not a tactile sensor placed at the fingertips of your gripper. It’s a sensor that you fix directly on your robot’s wrist, allowing it to read the force applied by the gripper in different direction during a given task.
Let’s say you are inserting a pin in a hole you want to feel that the pin is entering in the hole and not beside it. You can achieve such task with a FT sensor (and a lot more). In other words it’s like taking a can of soup in your hand. You can identify if it is heavy or not and this information comes from your wrist and/or arm depending on the effort they are doing to lift the can. Well that sensor is the equivalent of a FT sensor.
The FT300 is safe to use but should not be used for safety
Since collaborative robots are used without fencing, a lot more attention is given to safety requirements. In fact, the robot can literally be in contact with its user, so you have to make sure you control everything that can happen in the cell in order to reduce (read eliminate) the risk of injuries. A risk assessment has to be performed and you also need to reach safety requirements of your local worker association.
That being said, some safety requirements are expressed in force. For example, if an impact occur on the hand of the user, a maximum of 150N should be reached. Since robots are not necessarily programmed to show their sensed forces, it is logical to ask if you can use a force torque sensor to read the force that is reached at the impact. So why our force torque sensor cannot be used for such application? There is a actually a few reasons.
A single sensor at the wrist
Collaborative robots generally have a lot of different sensor embedded in their body. Either it is force torque sensors located at each joint or current limitation in their motors, every cobot have their way to track all their joints states and to stop a motion if they overshoot safety requirements. The robot controller is managing all this information and will stop at the moment that a single joint has reached a high value.
That also means that if the robot hits you with its shoulder, the joint at the base of the robot will ‘feel’ the impact, but the joint on at the robot wrist will not sense anything. So if we follow this concept, the only way the wrist joint will feel impact is if the impact occurs after this joint (on the tooling).
So there is really just one type of impact that can be felt by the FT300. Everything previous to the wrist can’t.
PLdCat3
You often see such inscription in robot controller, emergency switch or other safety devices, it is a safety rating that tells the amount of redundancy a device have and the possibility of failure.
To be able to use a device for safety, you need to have redundancy such as at least 2 independent communication channels and sometimes redundant sensors. So if we take the example of a collaborative robot, most of them will have 2 sensors that will look at joints counts and will ‘certify’ that the robot is at the place it needs to be. In the case of a sensor failing and the robot starting to ‘freak out’, the second sensor can shut the first one down and the robot won’t hurt anybody.
Since the FT300 was not designed for safety requirements but to measure forces in industrial applications, it doesn’t have such redundancy. So even if it is precise and very sensitive, it is not rated as being a safety sensor so if, for example, there is a sudden failure of the sensor, there is nothing to shut down the whole robot in order to prevent impact with a worker. Such details can be crucial in collaboration mode.
There is also reliability issues that needs to be addressed. In fact the ‘’PLdCat3’’ inscription ranks the reliability of the device. So if the safety device can fail 1 time out of 1 000 000 it gets a certain ranking. This type of data need to be tested and the safety device needs to be tested several time in different situation to make sure the reliability have been ranked correctly. Since the FT300 was not designed for safety requirement, we haven’t tested its reliability to achieve such a ranking.
100 Hz
The FT300 is reading and emitting at 100 Hz frequency or 100 times per second. It is a very fast rate if you are measuring a force on an object but if you are monitoring an impact with a human you will need to react faster than than (1000 Hz or more).
The FT300 is really good at doing what he has been designed for, but unfortunately it hasn't been designed to reach safety requirements. You will need to use other methods to make sure your robot is safe. And like in all collaborative applications, complete your risk assessment and make sure your cell is safe!
Leave a comment