Robotic Material Handling Case Study - Robotiq Adaptive Gripper

by Olivier Grenier-Lafond.
Last updated on Dec 12, 2024
Posted on Aug 26, 2014 in Robot Grippers
1 min read time
Posted on Aug 26, 2014 in Robot Grippers
1 min read time
Concept Systems is always searching for the most efficient and flexible material handling systems for their customers. Many companies count on their workers to make the adaptations necessary in handling a wide variety of workpieces, but are faced with serious cost problems when they need to execute similar tasks with robots.
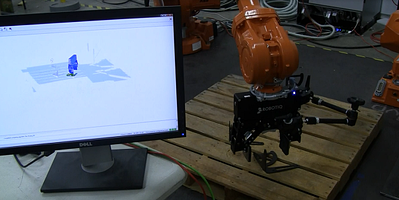
The Challenge
- Automate the system for the highest ROI for their customers
- Adaptive end effector and software
- Be able to handle various parts up to 20 lbs
- Improved data processing and material handling
The Solution
Concept Systems was able to leverage the benefits of a robot, an electric gripper and a vision system by finding the best combination in order to maximize the ROI for their customers when offering them a flexible automated system for different industrial environments.- Task categorization for the robot-gripper-vision system
- Fast and flexible integration with a Robotiq Adaptive Gripper
- A portable and versatile solution
- A flexible automated system
The Results
This automated system using the Robotiq Gripper and their in-house vision system allowed Concept Systems to offer a flexible turnkey solution to its customers at a reduced cost compared to standard systems. They can easily demonstrate to any manufacturer with oddly shaped parts that their system will pick up everything they need to handle. This solution can also be part of an autonomous logistics system between production lines. For more details read the case study on material handling involving Concept Systems.
Leave a comment