Lexicon of Collaborative Robot Terminology
Posted on Mar 18, 2014 in Collaborative Robots
7 min read time
The idea of standards is to try and harmonize usage across many countries and often fields of use. The standards are thus written in many languages and these languages might use the same term for similar meanings, but they might also use the same term to mean different things. There is terminology for the standards and there is common usage terminology, which also could be the same or different according to the language. So lets look at some specific terminology for the English language, so that we can all be on the same page when talking about robotic technology.
The following terms have been taken from several sources, including the newly released ISO 13482:2014 definitions for personal care robots and what is most often sited as 'general knowledge'. I have grouped the terminology not alphabetically, but by subject matter, so distinctions can be more easily recognized between terms.
ROBOT
Robot
Might mean just the arm without the end-effector for industrial automation standards; or an automatically controlled, reprogrammable, multipurpose manipulator programmable in three or more axes; or an actuated mechanism programmable in two or more axes with a degree of autonomy moving within its environment.
Robot System
The robot arm with the end-effector used in industrial standards.
Robotic Device
Actuated mechanism fulfilling the characteristics of an industrial robot or a service robot, but lacking either the number of programmable axes or the degree of autonomy.
Service robot
Robot that performs useful tasks for humans or equipment excluding industrial automation applications.
Mobile robot
Able to travel under its own control.
Robot cell
All the robot system(s) and associated equipment required to perform task(s) that are contained within a safeguarded space.
Robot Lines
Many robot systems or robot cells usually coordinated.
Collaborative Robot
A robot designed for direct interaction with a human within a defined collaborative workspace.
Collaborative operation - where a worker is in the sphere of active interaction during an automated robot operation. Often where the operator directly loads and unloads the robot or manually drives the robot to a specific location.
Autonomy or Autonomous Mode
The ability to perform an assigned mission(s) without direct human intervention.
Semi-Autonomous Mode
Operational mode in which the robot function accomplishes its mission with partial human intervention, different from collaborative in that semi-autonomous requires human interaction to run the robot, where as with collaborative mode the robot is generally autonomous and the human is working alongside the robot and not directly involved in the control of the robot.
Operator or User
Usually a human or a person designated to make parameter and program changes, to start, monitor, and stop the intended operation of the robot or in the case of personal care robots this maybe the beneficiary of the service provided.
Command Device
Device that enables the operator or a user to control the robot.
Manual Control Device
Human operated device connected to the control circuit. One or more manual control devices attached to a panel or housing form a command device.
Manual Mode
Operational mode in which the robot is operated by direct human intervention via pushbuttons or a joystick. This mode is usually used for teaching, tele-operation, fault-finding, repair or cleaning.
ENVIRONMENT
Working Envelope
The region of space a robot can reach.

Maximum Space
Volume which can be swept by the moving parts of the robot as defined by the manufacturer, plus the volume which can be swept by manipulators and payloads. For mobile platforms, this volume can be defined by the physical boundaries through which the robot can move around.
Restricted Space
Portion of the maximum space confined by limiting devices that establish boundaries which will not be exceeded by the robot.
Monitored Space
Space observed by sensors available to the robot.
Safeguarded Space
Space in which the robot initiates a safety-related function if a safety-related object is detected within it. Examples of safety-related functions include trajectory changes, speed reduction, protective stops, or force limiting. Space can be static or dynamic, depending on the robot, its application and its (dynamic) shape.
Collaborative Workspace
A workspace within the safeguarded space where the robot and human can perform tasks simultaneously.
Protective Stop Space
Space in which the robot will perform a protective stop if a safety-related object is detected. Distinctive from a Safeguarded space as the function performed is limited to a protective stop and a Safeguarded space may be much broader.
Cage Free
Robot not confined with a safety fence.
STOP
Protective Stop or Safety Stop
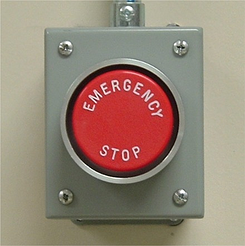
Used interchangeably, interruption of operation that allows an orderly cessation of motion for safeguarding purposes. A safety stop means that only the power to the manipulator motors is disconnected. There is no recovery procedure. You need only to restore motor power to recover from a safety stop.
Controlled Stop
Stopping the manipulator actions with power available to the motors, so that the manipulator path can be maintained. When completed, power is disconnected from the motors. Controlled stops are preferred since they minimize extra, unnecessary wear on the robot and the actions needed to return the robot system back to production.
Uncontrolled Stop or Hard Stops
Immediately stopping the manipulator actions by disconnecting power from the motors.
Kill switch or e-stop or emergency stop - is a safety mechanism used to shut off a device in an emergency situation in which it cannot be shut down in the usual manner.
Monitored stop or Safety-rated monitored stop - applies to a robot drive system that has built-in safety to ensure speed and/or torque is limited to a safe value. With this capability, the robot controller software and hardware have a safety-rated ability to limit the robot's range of motion. Hard stops, therefore, are no longer mandatory on new robots and controllers that have this ability.
SAFETY
Safety-Rated
A prescribed safety function with a specified safety-related performance, much more work needs to be done in this field to establish global safety ratings.
Inherently safe - commonly used to describe this new generation of collaborative robots. The inclusion of safety-rated technology with the robot and its controller is leading to new ways of using robots, and the belief is that the use of robots in manufacturing is only a small part of where they can be used. The expectations are that this will significantly increase the number and type of robots being sold.
Safety-Related Obstacle
Object, obstacle, or ground condition which can cause harm if it comes into contact or collision with the robot, may include humans, domestic animals, or property to be protected from harm.
Passive Safety
From the automotive industry and includes all means of preventing an operator from getting injured or at least to minimize the injury consequences in case of a collision.
Software limits - restrictions to one or more operational parameters of the robot as defined in the control system can restrict operating spaces, speed or force.
Open Texture Risk
Risk occurring from unpredictable interactions in unstructured environments.
Safety-Rated Soft Axis and Space Limiting Technology
This optional feature is available on new robots and may have different names depending on the robot manufacturer, but the functionality remains the same. Safety-rated software is used to control the robot motion so that restricted space can be more flexibly designed. Case studies have shown that this saves both floor space and cost in the system design.
Safety-Related Force Limit
Sets the upper boundary of force that a certain point of a robot can exert against a human, or other surrounding objects without creating an unacceptable risk. Standards are being worked on to establish criteria for this.
Electro-sensitive protective equipment or ESPE
Assembly of devices and/or components working together for protective tripping or presence-sensing purposes, and comprising as a minimum: a sensing device, controlling or monitoring devices, output signal switching devices or safety-related data interface. The safety-related control system associated with the ESPE, or the ESPE itself, might further include a secondary switching device, muting functions, stopping performance monitor, etc. A safety-related communication interface can be integrated in the same enclosure as the ESPE.
Pressure-sensitive protective equipment or PSPE
Assembly of devices and components triggered using the “mechanical activated trip” method to provide protection under hazardous situations. Examples of PSPE are pressure sensitive mats and floors, bumpers, pressure sensitive edges and bars. PSPE generate a stopping signal by the use of different techniques, e.g. mechanical contacts, fibre-optic sensors, pneumatic sensors.
FUNCTIONALITY
Relative Speed
Magnitude of the difference between the velocity vectors of the robot and an object (including a human) about to be touched. The robot velocity is the vector sum of velocities for the robot body and its moving parts.
Kinematics
The actual arrangement of rigid members and joints in the robot, which determines the robot's possible motions. Classes of robot kinematics include articulated, cartesian, parallel and Selective Compliance Assembly Robot Arm or Selective Compliance Articulated Robot Arm or SCARA.
Compliance
This is a measure of the amount in angle or distance that a robot axis will move when a force is applied to it.
Accuracy
How closely a robot can reach a commanded position.
Repeatability
How well the robot will return to a programmed position. This is not the same as accuracy.
Teach Mode
A task using manual reduced speed mode.
Some words are recognized by their common use meanings such as: risk, risk assessment, contact, unintended contact, allowed contact and hazard, which are all given standard dictionary definitions. What terminology we use determines many things especially our attitudes. So having a positive common language about robots is important for societal acceptance. So designing 'protective stops' instead of relying on a 'kill switch' is probably a good place to start.
Leave a comment