6 Key Points for Effective High Speed and Precision Robotic Welding
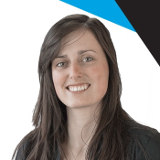
Posted on Dec 11, 2013 in Robotic Welding
4 min read time
In the last RIA webinar, interesting subjects were discussed such as high speed and high precision welding. The panel discussion presented important things to consider if you want to use these processes with industrial robots. So here are the top 3 things to consider when welding at high speed and high precision.
Top 3 Important Concepts for High Speed Robotic Welding
1) Part Fit up
One important thing to consider when welding at high speed is the part fit up. It is very important that the part can not move during the process by using the right clamping force. Compensation is a slow process so, if your part moves, it will increase your cycle time. Moreover, inadequate clamping would make your robotic welding process non repeatable and again considerably slow down your speed. Positioning your part the right way, the first time, for your weld can also improve your speed.
2) Choosing Appropriate Equipment
The appropriate choice of equipment is necessary for high speed welding. If you know that you need high speed welding for your application, you could easily consider fast welding processes such as laser welding, plasma welding or other technologies meant for high speed welding. Moreover the choice of the right power source must also be considered to assure the right amount of heat for the weld. Then, the filler material can influence your welding speed a lot, especially for thin material. The experts mentioned higher manganese and silicon filler material which help for oxidation, as well as constant current, which allows the weld to be molten for a longer period of time.
3) Pay Attention to Magnetism
The other thing that was mentioned is about the magnetism in welding. The part to be welded often has clamp tooling or pins to fix it in its right location, however it is recognized that the current will be affected by those hardened materials as the torch passes near them. These current characteristics can induce sudden changes in the welding arc which will slow down your process since you won’t have the right melting parameters. In order to avoid these interferences, the welding path of the robotic welder can be adjusted as well as the location of the clamping or grounding tools.
Top 3 Important Concepts for High Precision Welding
1) Make Sure to Know the Welding Robot Dynamic Path Repeatability
When talking about high precision welding, the main component to consider is the welding robot itself. When end users are looking to buy a robot for this kind of robotics application, they often look only at repeatability and tend to make their decision on this simple characteristic. However, what most people don’t realize is that this data is taken in a static environment. In a welding process the robot has to be precise when moving. So the advice the experts gave was to deeply discuss the dynamic path repeatability with your robot manufacturer supplier. A simple look at the robot chart will not give you the right information about precision of the robot for all welding applications. Moreover, it is important to check this characteristic with the same end-of-arm tooling that you will be using to make sure it will fit your needs.
2) Consider all Environmental Conditions for Your Welding Applications
The next important thing to mentioned is again part location and clamping. Laser and camera tracking can also help with precision. Also, trimmed edges can cause poor fit gap and variation that can alter your accuracy. Weather or environmental conditions can also play a role in the precision you can obtain since moisture and oxidation will affect your welding process.
3) Have Regular Maintenance and Calibration of Your Equipment
The last important thing to consider is the maintenance of your equipment. Industrials robots do wear down and need readjustments over a certain period of time. Calibration should also be done on a regular basis to assure the precision of your robot.
RIA’s webinar on Advanced Welding Techniques contains a lot of interesting information, so if you want to see my previous posts, check out:
RIA’s Webinar: Advanced Welding Techniques
Advanced Welding Techniques - Panel Discussion
Stay tuned for even more valuable content!
Leave a comment