Collaborative Work by Yaskawa/Motoman: FSU
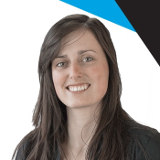
Posted on Oct 22, 2013 in Collaborative Robots
2 min read time
A couple of weeks ago, Robotiq released its new ebook on Collaborative Robots introducing 9 different robots to the industry. These new types of robots are renown for their ability to work safely alongside human workers. The way industrial robots are used in manufacturing is about to change, since no barriers are necessary anymore. The safety systems are now integrated into the robots themselves.
New Standard
In order to assure that the use of these new robots is safe on the production line, the Robotics Industry Association announced, in May 2013, the adoption of the AINSI/RIA R15.06-2012. This is the new robot safety standard. Companies are now able to use collaborative robotics and remain AINSI certified, as long as the guidelines are respected. Various safety systems can be used to meet this standard and they are explained in a previous article: Safety Standards for Collaborative Robots
What about Yaskawa/Motoman?
When reading our ebook, some may notice that Yaskawa/Motoman robots are not on the list. In fact, they don’t have collaborative robots, as we presently understand them. However, their controller offers a “Functional Safety Unit” that respects the new AINSI standard. Therefore, any Yaskawa/Motoman robot can be use in a collaborative way.
The system uses safety-rated monitored stops, as well as speed and separation monitoring. Safety-rated lasers and sensors are part of the system and they are used to detect the presence of humans in the collaborative zone. More details of the Functional Safety Unit (FSU) for Yaskawa/Motoman are explained in this video showing a collaborative assembly application with a Motoman robot and a 3-finger robot end effector:
Moreover, the sensors used with the FSU are fail-safe. Erik Nieves is the Technology Director for Yaskawa Motoman Robotics in Miamisburg, Ohio and he explained this fail-safe feature:
“Safety-rated sensors have built-in fail-safes. The signals go to two separate places in the robot controller, and those signals are then processed by separate hardware running different algorithms. Those two pieces of software and hardware are then doing cross-checking between them. And if either one of them drops, the system goes into a safe condition. Robot controllers that are third-party certified for functional safety per the standard have to demonstrate that level of redundancy.” - Erik Nieves
Therefore, manufacturers can be assured when looking at Motoman’s products for collaborative tasks. Especially since the FSU agrees with the new AINSI Standard in several ways.
Leave a comment