How to Create Fast Cycle Times with the Adaptive Robot Gripper?
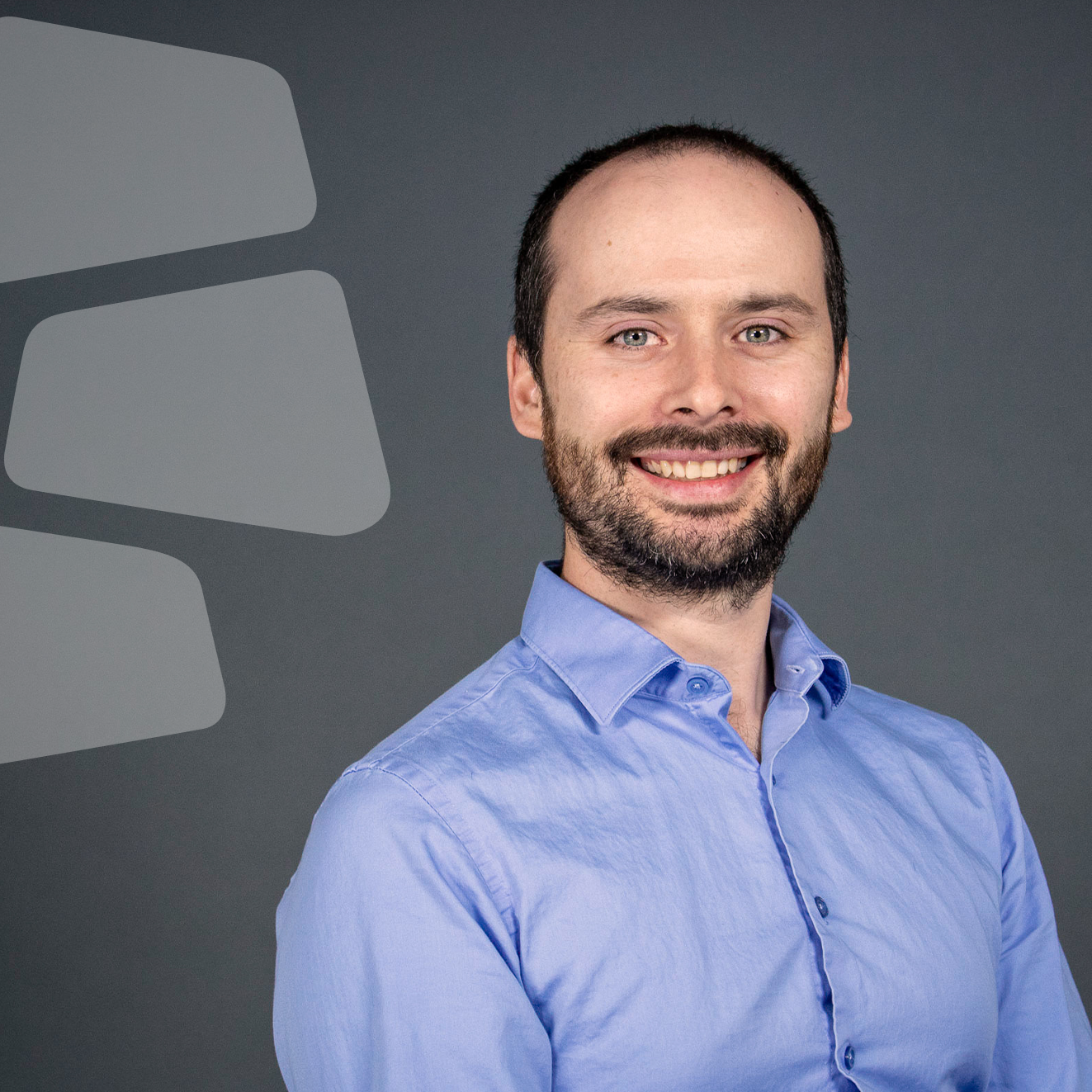
Posted on May 22, 2014 in Robot Grippers
3 min read time
One of the advantages of a servo-electric robot gripper is that it allows you to control the position of the fingers. If the size of the object you want to pick up is known, the fingers can be partially closed before the robot has reached the pick-up location. This, in turn, will reduce the time required to pick up the object and therefore the cycle time will be reduced. As we all know, reducing the cycle time is highly desirable as it allows us to increase the production rate of a robot. In this article, I will present how the cycle time can be reduced by programming the partial opening of the 2-Finger Robot Gripper.
How to Calculate the Robot Gripper Cycle Time?
If we consider a pick and place application, the cycle time can be split into two components: the time required by the robot to move during the whole cycle (Trobot) and the time required by the Gripper to pick up the object and release it (the Gripper cycle time, Tgripper). Let's focus on the Gripper cycle time as the robot component will vary too much depending on the application.
The Gripper cycle time can in turn be split into three components: the time required to grip the object (Tgrip), the time required to release it (Trelease) and the idle time, which comprises all the time required for the Gripper to update its status to the master and for the master to send new commands to the Gripper, plus the time lost during the acceleration and deceleration of the fingers (Tidle). The idle time is tricky as it depends on the communication protocol and on the master and will vary slightly from one cycle to the next. Therefore, the Gripper cycle time can be split into a fixed delay (Tidle) and two delays which vary according to the grip margin (Tgrip, Trelease). The grip margin is the opening of the fingers minus the object size and is required to avoid interference between the Gripper and the object during the approach trajectory. To measure the Gripper cycle time, we ran some tests using the TCP/IP communication protocol on a standard PC. We ran the tests for both gearbox options (24:1 and 14:1) of the Gripper, using the full speed setting. We found that the cycle time varies proportionally to the grip margin, as shown on the graph below:
On the graph, it can clearly be seen that minimizing the Grip margin will have an enormous effect on the Gripper cycle time, and as a consequence on the total cycle time. The cycle time can more than double if no attention is paid to the partial opening position!
For these tests, Tidle was found to be 0.16 seconds for the 14:1 gearbox option and 0.31 seconds for the 24:1 gearbox option. Again, these values will vary depending on the master and the communication protocol of the Gripper. Tgrip and Trelease can be approximated by dividing the Grip margin by the finger speed. The Gripper cycle time is therefore computed as:
Tgripper = Tidle + 2 x Grip margin / finger speed.
Notice that the experimentation have been done on a first generation 2-Finger 85 Adaptive Gripper because gearboxes can be changed. The same concept applies on the latest version of the 2-Finger 85 Adaptive Gripper without considering the gearboxes difference.
How to Choose the Grip Margin?
In the last section, I showed the effect of the grip margin (finger opening before the grip minus the object size) on the Gripper cycle time. Clearly, this distance has to be minimized in order to get the best production speed out of your robot. How small of a margin can we use? Well, it depends. On one hand, the Gripper repeatability is good enough to lower the margin to a very small value (under 1 mm). However, a small grip margin will require the robot to be very precise in its approach trajectory to avoid hitting the object. This may require the reduction of the robot speed, which will in turn increase the cycle time. Therefore, a tradeoff has to be achieved which will depend on the application (robot, object shape variability, object positioning, etc.). Generally, it is better to use a slightly larger grip margin to avoid hitting the object in all possible situations (reliability is often more important than cycle time!). As a result, the choice of the grip margin is not always easy to optimize.
To conclude, lets just say that being able to set the partial opening position is a key feature in the optimization of the cycle time. This is a clear advantage of servo-electric grippers such as the 2-finger Adaptive Robot Gripper!
Leave a comment