How To Handle Fragile Parts With Robots
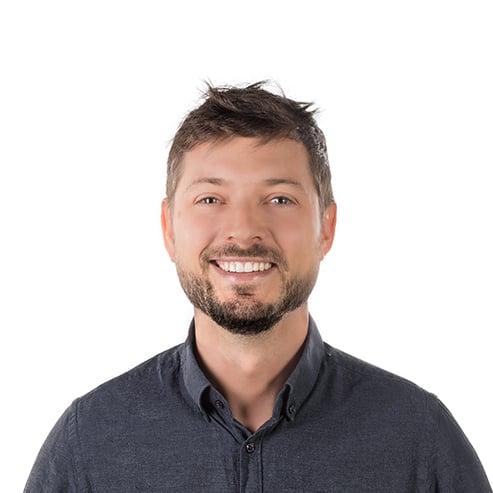
Robots were initially used in dull, dirty and dangerous jobs. Today, you can add yet another D to that list: delicate. Handling fragile parts comes with its challenges. This article offers examples and guidelines to use to avoid damaging fragile parts when handling them with a robot.
Fragile parts are subject to damage from three sources:
-
Excessive holding/handling force from the gripper
-
High acceleration/deceleration from the robot
-
Being crushed while picked or placed
Here are a few fragile part examples by industry:
-
Electronics Industry: handling thin wafers
-
Food Industry: handling fruits, vegetables or baked goods that vary in size and shape
-
Automotive Industry: handling ceramic catalytic converters
-
Casting Industry: handling wax patterns in investment casting - any deformation made on the wax part will result in a deformation in the final metal part
Best practices for handling fragile parts with robots
Different factors can be considered at the gripper, robotic system or programming levels to avoid damaging parts.
Gripper level
-
Position control
Control the gripper position to avoid finger collision damage. -
Force control
Control the force to avoid crushing the part. -
Force sensing
For very precise force control, you'll need feedback using force sensing. -
Gripping modes
Encompassing grips will have more contact points and distribute the pressure more evenly on a part. -
Fingertip design
Similar to an encompassing grip, it is possible to adapt the finger shape for more friction surface to distribute the pressure or use a soft material, to reduce the necessary actuation force.
Robotic system level
-
Vision system
A vision system can be used to adjust the trajectory precisely to avoid hitting the part and to pick it up in the proper orientation. -
Compliance device or force-torque sensor
Compliance, or force-torque control, can be used at the wrist to avoid hitting the part or coming at it too hard.
Programming level
-
Minimize acceleration and deceleration
This will reduce the reaction efforts from the tool due to acceleration. Having smooth trajectories with gradual acceleration will also help. -
Part orientation
Choose a place and orientation to pick the part so it minimizes the required holding force.
Leave a comment