Are You Still Doubting Collaborative Robot Safety???
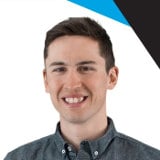
Posted on Jul 02, 2015 in Collaborative Robots, Safety
4 min read time
As I visit different shops and laboratories to discuss the potential of robotic integration, the major concern is always safety. And this is totally legit, you really don't want you or your employees to get hurt in their everyday job. However, collaborative robots are doing a great job on the safety side of things. Force limited robots are really the rising trend in the industry right now and not just for functional reasons, but also for safety reasons. It is now easier to automate a process without having any type of guarding around the robot arm. But what does it all means? Can we really trust these force sensors?
Stabbing Robot
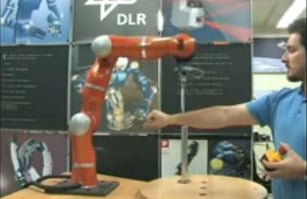
I recently watched a video from DLR, the German Space Agency that conducted a study on soft tissue injuries in robotics. As I have often said in my past blog posts: ''It's not because the robot is ''safe'' that the application is safe''. Well apparently, DLR is nuancing this statement.
In the following video, the study shows different impact scenarios for soft tissue damage caused by different types of tools wielded by a collaborative robot. In the case study they were using a KUKA LBR iiwa.
The first impact set was identified as a penetration injury. This was pretty much caused by a downward movement of the robot arm which penetrated a material used to simulated human tissue, here a leg of lamb. Using a butter knife, scissors, a steak knife or screwdrivers, the first impact set was done without any ''impact detection'' at a speed of 0.64 m/s. You can clearly see the level of penetration that is reached by the tool. In fact without some kind of force detection, the collaborative robot cannot feel what it is doing (just as an industrial robot would not feel what it is doing). This means that the robot will stop its motions only once its position is reached regardless of whether or not an impact has occurred.
In the second set of impacts, the force limitations have been set and the motions are done at the same speed. Using the same tools, you can see a very shallow penetration or even no penetration at all. Since the robot notices the force, it stops when the force threshold has been met.
The third set of impacts is completed using cutting motions, so an angular dragging motion to cut or slice an object for example. First the study is done without force detection using a kitchen knife and a scalpel. The penetration level is quite impressive for both tools. Since the robot is not feeling any restriction, it just goes to its next requested position. Ouch!
The fourth set of impacts is done using the same cutting motion, but with force detection activated. Even if the tools used are very sharp, they do not penetrate the soft tissue because the force detection threshold has been set to detect this. Once the robot is feeling excessive force over what it is programmed to detect, it simply falls into alarm or emergency mode and stops all its motions.
Finally the tests are done on a human arm to demonstrate the safety of the concept. All these tests are simply proving that force limited robots can be used for dangerous tasks and still be safe for the user. Notice that the impact tests implicating force limitation have been done by substituting a lamb for a human and these tests do not consider the head or vital organs as parts that could potentially sustain injury. You should also notice that a part of the upcoming ISO/TS 15066 will be entirely dedicated to the impact of robots on human body parts and the force threshold that will or will not be acceptable. This standard will also consider the pressure applied to different impact areas (the sharpest area, the more concentrated the force, etc).
Kicking Robot
The next video has been generated after the study on different crash impacts. This study was also directed by DLR. You can see in the video different robot setups for different speeds and inertias and on different body parts. The baseline is to observe the difference in impact between a robot having force sensing or impact detection and others who don't.
The major difference between robots with force limitation and those without it is that once the robot hits the mannequin, the force limited robots will loosen all their joints and stop its motions to protect the human or in this case mannequin. With regular robots they will continue until they reach their final position without adjusting anything.
As I was looking for some data on the safety features of collaborative robots, I noticed that most robot manufacturers don't even rate (or explain) the maximum force available in collaboration mode. In other words there is no direct way to know what force level is applied by the robot before it shuts down. I know that in some robot controllers different settings can be established to stop the robot, but nothing really quantifies the energy level or the force that will initiate this stop. Maybe this is only a question of there being too many possible configurations and that the inertia of the robot arm also has a variable impact on the energy output. Even so, it would be interesting to have this data on specification sheets.
Anyway, the conclusion of these two videos confirms for me that collaborative robots are safer than I thought. I had always considered the sharp tool case as being the most dangerous, now this seems to be more nuanced. Depending on the force threshold you set on the robot, even a sharp tool won't be able to penetrate soft tissue. I'm not saying that all cobots are safe in all circumstances, but if you were concerned about this situation, you have the proof that this isn't black or white. You still have to do a comprehensive risk assessment when integrating any robot onto your workfloor or laboratory. However, if you were doubting of the credibility of these robots, you now have proof.
Leave a comment