Preparing your factory for the workforce of the future
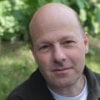
Automation, Artificial Intelligence and the Internet of Things are transforming the modern-day factory. High on the list of what’s being transformed is the workforce. Here’s how to get ready.
Photo by Margaux Olverd on Unsplash
It’s time to look long-term at who will be working in the company plant.
A clear picture is emerging of facilities. If the reports are correct, they will still require plenty of human beings. It's those “soft skills” that humans possess that will help guide the increasingly automated parts of the operation. Those looking at the future predict more decisions will be made from the factory floor, while the factory floor will be filled with increased machine-to-machine communication.
Looking at case studies from some of the innovative factories operating today and taking leads from some prognosticators, here is a cheat sheet to help you prepare for the factory workforce of the future and think about your future operations.
There will be lots of manufacturing jobs
We’re nowhere close to announcing the death of manufacturing jobs in the west. In fact, according to a 2018 skills-gap report by Deloitte and The Manufacturing Institute, the industry could experience employment bottlenecks, leading to a potential 2.4 million jobs in the US going unfilled by 2028, with US$454 billion at risk if qualified workers cannot be found to fill the open jobs. Is your HR department set up for this? How far afield are you willing to look? It might be time to put together some long-term recruitment strategies.
Human skills will be key
As a manufacturer or company manager, you’ll be able to better harness the changing technology if you hire factory workers for their “soft skills.” And what are those skills? Decision-making, critical thinking, people management, creativity, and adaptability. Drilling down further into more specific skills, you will need to hire people who can program for robotics, calculate algorithms for supply chain and can work with both tools and software. These are the new terms to put onto those future job postings.
Expect some new job titles
Don’t get caught up in the old roles and duties; they’ll be shifting to match the changing needs on the factory floor. Two recent reports, one by ManpowerGroup and UI Labs’ Digital Manufacturing and Design Innovation Institute, the other from Deloitte, offer up dozens of new titles including Digital Twin Architect, to create virtual representations of products, processes and systems, Collaborative Robotics Technician, to set up and maintain collaborative robotics systems, Robot Teaming Coordinator, to monitor robot behaviour in work environments and provide feedback to programmers, and Predictive Maintenance System Specialist, to monitor the health of a critical manufacturing asset and figure out when it might fail. These may sound foreign right now, but in the future, they will be part of the manufacturing lingo.
Some improvements will be worker-led
As changes come fast and furious, you’ll need to start drawing more on your workers for their insights into productivity. That’s what happened at a Procter & Gamble plant in the Czech Republic town of Rokovníc when the longtime employer in the town of 16,000 was facing unprecedented market shifts. Operators and employees were invited to think about what problems automation could solve and to identify opportunities that might give a boost to productivity. After implementing upgrades suggested by those employees, the factory managed in three years to increase output by 160 percent. Customer satisfaction rose by 116 percent. Are you ready to allow your workers to have more of a say in your future?
Machines will be talking amongst themselves
Listen closely. That’s the sound of all the future machines communicating. While workers communicate with their superiors, each other and their robots, a new generation of on-demand automation technologies will be sending signals to one another. Setting up this type of monitoring is proving to be a low-cost solution and is already saving companies hours of inspection time. It also identifies equipment that needs to be replaced or is in better shape than previously thought. It might be time for you to start looking at this technology for your company.
It’s easy to fret about the future, but many of the doomsday scenarios about manufacturing are proving to have been off-base. There will be a particular type of factory that will thrive in the decades ahead, and it will need to attract a particular workforce. This glimpse into the future might just take away some of your worries and help you feel better prepared.
Leave a comment