4 Reasons You Still Need to Watch for Human Error When Working With Robotics
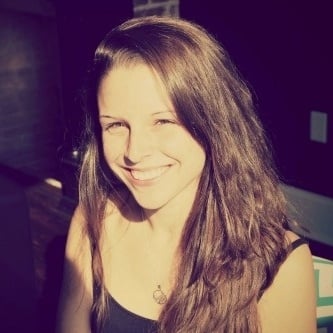
It's increasingly common for companies to invest heavily in robotics and use innovative machinery to reach targets faster and with fewer errors than humans alone could.
High-quality robotic equipment can achieve high accuracy and repeatability without becoming fatigued like people do.
As such, the quality level of a product could go up once companies deploy robots, but it's necessary to be mindful of human error and solve issues associated with it to maximize the overall impact.
Human + Robot collaboration at the Robotiq User Conference 2018
1. Humans may not feel competent around robots
Keeping productivity levels high is a constant challenge at many companies, but robots can help manage that obstacle.
Beyerdynamic, a German audio equipment manufacturer, sought to double productivity levels in a four-year span and needed robots to help without taking up extra floor space. It deployed a combination wrist camera and gripping robot and noticed rapid gains in both speed and quality levels.
The company communicated with employees to see which ones wanted to try the robots in a pilot project. Those who participated received training to get comfortable around the robots and are now accustomed to the new process.
It's crucial for companies to help employees embrace robots by providing relevant training. Otherwise, they may not feel at ease and might make errors due to nervousness or unfamiliarity.
2. People could stray too close to robots in motion
Collaborative robots have safety features that make them move slowly around humans and stop if they make contact. However, other industrial robots can cause fatal injuries. In one instance, a worker who fixed robots at an auto parts factory was killed when a robot that malfunctioned struck her.
A lawsuit filed about the matter mentioned that the robot should not have entered the area where she was working. But, something went wrong when several of the employer's safety devices on the machinery failed. It's not enough for company representatives to assume such features will work properly. They must keep people safe by being more proactive.
It’s been reported that, already, 51,550 warehouse workers get hurt or killed on the job every year in the U.S. Add robots into the equation, and it’s possible we’d see that number increase. While solutions like safety painting could help reduce this number and better mark off a robot’s expected path of travel, managers and floor overseers should prioritize educating their teams about the need to be mindful when working around robotic equipment.
Although the Occupational Safety and Health Administration (OSHA) doesn't have specific robot-related requirements, that industrial machinery falls under the organization's General Duty Clause. It requires employers to keep workplaces "free from recognized hazards that are causing or are likely to cause death or serious physical harm."
3. Robots require proper programming for optimal output
Some of today's leading robotics equipment performs several tasks, making repeatability more valuable than ever. When a startup called Creating Revolutions experienced double-digit rejection rates for its hospitality pagers, the company's representatives hoped robots could change the trend. The business ultimately invested in a two-finger gripper that handles four tasks.
The company's error rate dropped below one percent after it started using the robot. This case study demonstrates how some of today's technologies are truly multitasking options. They still need humans to tell them which job to do, though. Programming mistakes that people make could waste time and money for businesses that use robots. But, continual education is essential, especially in tech-centric workplaces.
According to a survey of American workers published in 2014, 54 percent felt they did not possess the skills needed to excel in their jobs. If an employee does not know how to program a robot to set it up for a new task, it doesn't matter how many different functions the machine can do.
This lack of knowledge can disrupt the workflow. That's an especially likely outcome if a person programs the equipment incorrectly due to a lack of training or has to find someone who does have the necessary programming skills.
4. Improper maintenance could compromise performance
Many robots can tell users if something is wrong or a part is about to fail. However, periodic preventative maintenance at recommended intervals is crucial, including after periods of prolonged use. If people make mistakes while maintaining robots, the overall lifespan of the machines could go down.
Employers should provide all-encompassing checklists to guide maintenance processes. They should also carry out drills to test employee competency for maintenance matters.
Robots are smart but need human intervention
Even the most up-to-date robots won't demonstrate trouble-free operation if humans make frequent mistakes.
It's an employer's responsibility to safeguard against preventable human errors to enable the most favorable outcomes made possible by robots.
Leave a comment