KUKA's Collaborative Robot Option: KR 5 SI
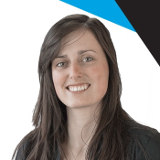
Posted on Dec 05, 2013 in Collaborative Robots
3 min read time
Since the release of our last Ebook on collaborative robots, robot manufacturers have been informing Robotiq that they also have their version of a collaborative robot. Therefore, other collaborative robots are now known and we would like to present them to you.
In our last edition of the Ebook, the German manufacturer KUKA was not on the list, however, we were informed that one of their collaborator's designed a technology package that allows for safe human interaction.
Becoming a Collaborative Robot
The company MRK-Systeme GmbH provides automation solutions for many industrial sectors. They are specialized in safety systems that allow human-robot collaboration. So they are presenting the 'Kleinroboter' or small robot, KR 5 SI (for Safe Interaction).
This is a technology package that is an option for the KR 5 ARC HW KUKA’s low payload robot. This option is able to transform ordinary industrial robots into a collaborative robot approved by DIN EN ISO 10218 and TS 15066 regulations. The certification system is one reason why physical separation is no longer needed between robots and humans.
Safety System
The system is based on 5 functionalities:
- The software, KUKA.SafeOperation, monitors the position and speeds of each axis of the robot in order to respect the work space.
- The use of damping safety pads all around the robot provide a constant reduction of the kinetic energy in case of a collision. The pads also hold the tactile and capacitive sensors mentioned below. Tactile sensors are used to stop the robot if a contact occurs.
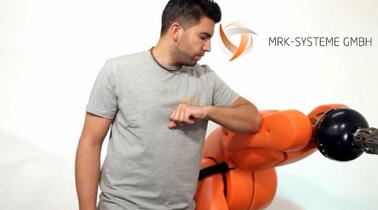
- The systems also has capacitive proximity sensors that detect a human presence with the change of the electrical field. This is done by measuring the dielectrical constant. Here is a chart showing different materials:
- The system has 7 to 6 sensor areas around the robot structure. The analysis of the signal depends on the robot position.
- The end effector area is protected by a detachable adapter flange. If a collision occurs with the flange, it will detach to avoid any damage or injuries. The force to detach the flange is about 120 N and a safety signal will stop the robot.
With all these components, the robot is classified as safe for human interaction. However, it is important to mention that working around a robot, in general, will always have some risks and a worker should always be aware of that and work wisely around any industrial robot.
Applications
This system can be used in at least two applications: a carrying measurement system and material handling.
As an example for the measurement system, the robot could hold a camera in order to do automated inspections. (Quality Insurance)
Or, for a material handling application, the robot could be used in a machine loading and unloading task. (Pick-and-Place)
For more information on this new collaborative robot, see the company website: MRK-SYSTEME GMBH
Leave a comment