Which Surface Shapes Are Compatible With Robot Finishing?
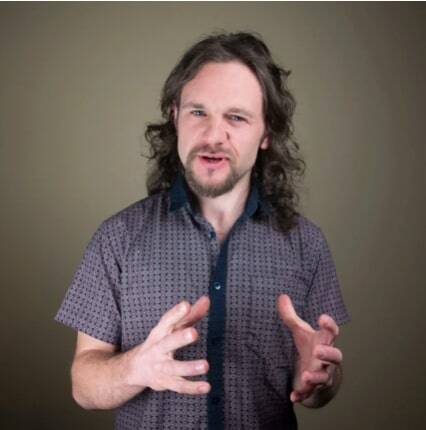
Robot finishing requires more planning than manual sanding and polishing. Here's how to determine if your workpiece surface shape is compatible.
Human hands are extremely adaptable. With manual finishing, practically any surface shape can be sanded or polished. We don't usually think about categorizing the shape of the surface we are working on — we just get on with the task.
With robot finishing, we need to be more specific.
In the past, you needed to be extremely precise with robot programming. You would often have to program every single point of the robot's trajectory.
Modern finishing kits mean that you can now program a robot finishing application much more easily and quickly. To program a finishing path into the robot, you now only have to categorize the shape of the surface and define the path by a few "waypoints."
Which surface shapes are compatible with robot finishing?
You can sand or polish practically any surface with a robot. However, you must first categorize the shape of that surface.
There are 4 compatible shapes:
- Flat surfaces — e.g. a glass window, metal sheet, or wooden panel.
- Curved surfaces — e.g. a curved metal car bonnet, airplane fuselage, or circular disk.
- Spherical surfaces — e.g. a wooden dome, fiberglass plant pot, or spherical plastic speaker.
- Mixed surfaces — any combination of the above surface shapes.
Each of these surfaces requires a different strategy when programming the path into a robot. Programmed is carried out by entering the correct "waypoints" into the program. Then, a specialist path planner will calculate all of the points in the robot path.
The role of waypoints in robot finishing
"Waypoints" are simply intermediate positions in a robot program. For example, if I'm doing a machine tending task and I want the robot to move from the CNC machine to a crate via the table, there are 3 main waypoints in that program: the CNC machine; the table; and the crate.
Waypoints play an important role in robot finishing because they allow us to program the robot's path without having to program every single point in the trajectory.
When we are sanding or polishing by hand, we don't think about our arm movements as being through "waypoints." Instead, we think in terms of lines or zones of the surface. With a software tool like Finishing Copilot, it is possible to program the robot using a similar approach, with only a few points to define each zone of the surface.
Picking the right A value
Below, we outline the different waypoints that are required to program each of the 4 surface shapes. However, there is another value which is also needed for all shapes. This is known as the "A" value within our Finishing Copilot software. You could also call it the interval or the spacing. It defines the distance between two lines of the finishing task. The software will use this value to calculate all the lines within the program.
To overlap or not to overlap?…
… that is the question…
And the answer is (usually), Yes! You should overlap!
It is generally taken to be good sanding practice to overlap each row of the sanding. A common amount of overlap is between 25-50% of the width of the sanding tool.
To calculate the A spacing you can use the following equation:
A = width of sanding surface x (100% - overlap in %)
For example, if you were using a 5" (12.7cm) sanding pad as used by our Sanding Kit with an overlap of 40%, you would get:
A = 5" x (100% - 40%) = 3" or 7.62 cm
Flat surfaces: 4 waypoints
Programming a flat surface is the easiest of all of the finishing tasks. It only requires 4 waypoints, one for each corner of the surface.
The 4 waypoints for defining a flat surface
Flat surfaces include rectangles, squares, and triangles (if two of the points are the same).
- Start point — First corner of the rectangle/square zone.
- Short edge point — The robot will move in straight lines parallel to the "long edge." The "short edge" isn't necessarily the shortest, it just refers to the edge that the robot will zig-zag along.
- Long edge point — The robot will move directly here after the start point.
- End point — Final corner of the rectangle
Curved surfaces: 6 waypoints
Curved surfaces are slightly more complex to program than flat ones. You could think of them as a square/rectangle with 2 extra waypoints (6 in total) to define the arc of the curved edges.
The 6 waypoints for defining a curved surface
Curved surfaces include cylinders, cones, and flat circles.
- Start point — The first corner.
- 1st edge curve center — The center of the arc in the first "short" edge.
- 1st edge curve end — The end of the arc in the first short edge.
- 2nd edge start point — The end of the "long" edge (i.e. the edge that the robot will move parallel to).
- 2nd edge curve center — The center of the arc in the second short edge.
- End point — The final corner.
Spherical surfaces: 9 waypoints
The newest addition to our Finishing Copilot software allows you to program spherical surfaces for the first time ever. Spheres are the most complex basic shape that you can get when it comes to robotic finishing. Programming them requires 9 waypoints.
The 9 waypoints for defining a spherical surface
Spherical surfaces can include anything from a literal sphere to more complex curved geometries. The surface can be thought of as a flexible quadrilateral (4-sided shape) distorted over the spherical surface.
- Start point — The first corner of the quadrilateral.
- 1st edge curve center — The center of the arc in the first edge.
- 1st edge curve end — The second corner of the quadrilateral.
- Center curve start — The center of the "long" edge.
- Center curve center — The central point of the quadrilateral.
- Center curve end — The end of the arc in the "long" edge.
- 2nd edge curve start — The fourth corner of the quadrilateral.
- 2nd edge curve center — The center of the arc in the last edge.
- End point — The fourth and final corner of the quadrilateral.
It is possible to use either a vertical or a horizontal motion for spherical surfaces.
Mixed surfaces: Combinations
Although there are only 3 basic shapes, you tackle almost any surface shape by combining the 3 types above.
Combinations of surface shapes are quite easy to achieve. You just need to split up the surface into flat, curved, and spherical zones. It is then simply a case of programming each zone using the required set of waypoints.
Leave a comment