What Are the Best Types of Cups for Your Workpiece?
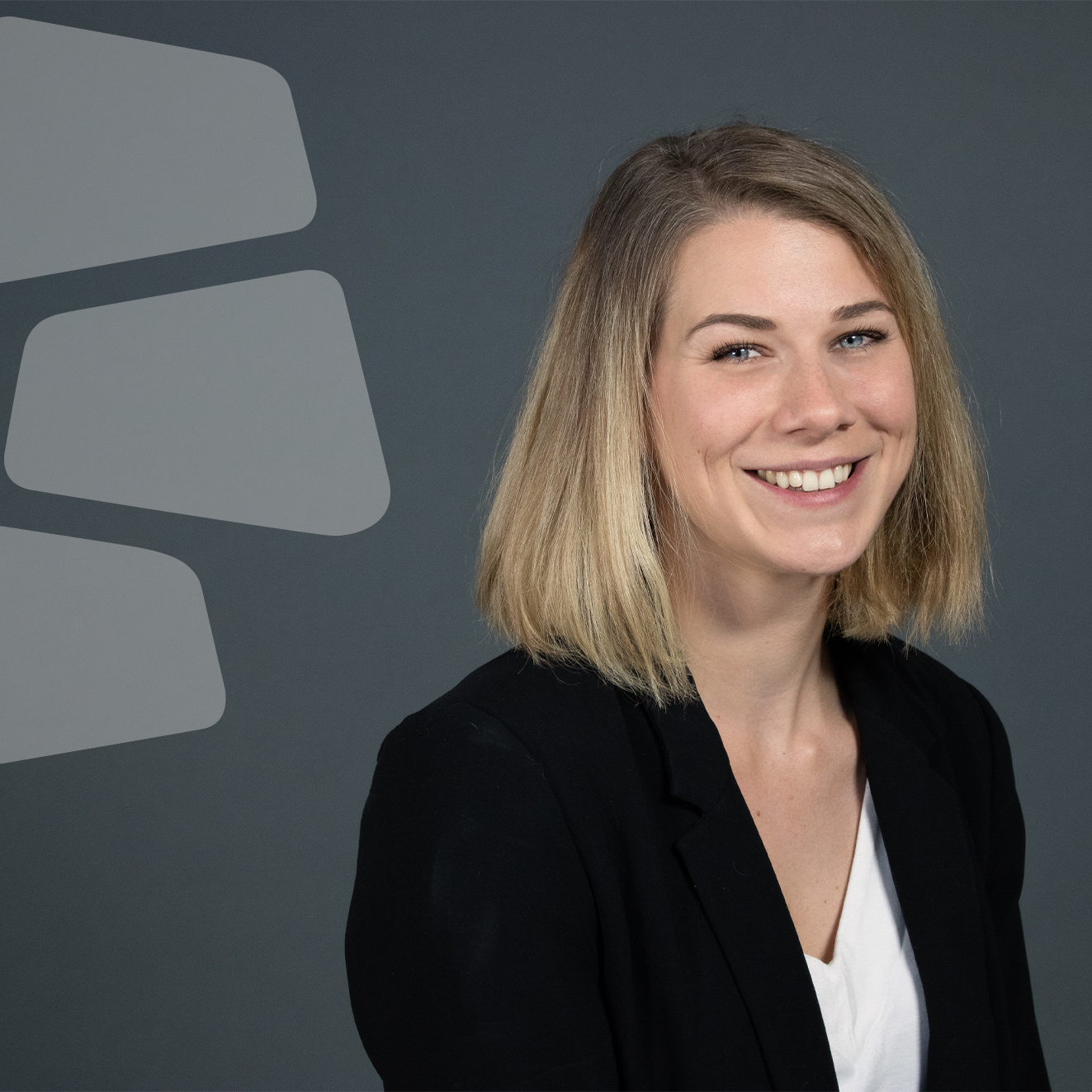
Posted on Oct 24, 2019 in Manufacturing
5 min read time
From packaging to machine tending to assembly, a growing number of boring, repetitive tasks are now automated by robots so that the immense creative potential of human hands and minds can be better applied elsewhere. If you’re interested in the performance and versatility of the Robotiq AirPick and EPick Vacuum Grippers, which launched at the Automate 2019 show in Chicago, chances are you’ll want to implement your own automated vacuum-handling system to enjoy the increased productivity and efficiency.
Designing a reliable vacuum-handling system involves many factors, but they all come together at the vacuum suction cup. Today, leading manufacturers like Festo offer many types of cups to manipulate a wide range of materials. However, there is often more than one right answer when it comes to selecting the right cup for a particular application, which is why we’ve put together these vacuum suction cup selection guidelines to help you make sense of the different types, sizes, and materials available. It is important to note that cup selection typically involves a combination of theory to narrow down to a few good options and physical testing to make the final decision.
Construction
Vacuum suction cups are available in different shapes, each suitable for gripping different surfaces:
- Standard: suitable for flat and slightly undulating and domed surfaces. Vacuum suction cups of this type can grip workpieces very quickly thanks to their low overall height and small internal volume. Their flat shape gives them good stability as well as the ability to withstand lateral forces and rapid acceleration. The typical applications of standard vacuum suction cups include smooth or slightly rough workpieces such as glass, metal, and plastic parts.
- Bellows: suitable for beveled, domed, round, large surfaces and pliable workpieces because of their ability to compensate for uneven surfaces. Bellows vacuum suction cups provide damping for handing delicate workpieces, such as glass bottles or lightbulbs. Other common applications include electronic components, blister packs, and injection-molded plastic parts.
- Oval: suitable for slim, oblong workpieces such as profiles and pipes. Despite their relatively small dimensions, oval vacuum suction cups can generate higher forces than standard, circular cups, making them indispensable for handling all kinds of thin and curved objects.
- Extra deep: suitable for snappy handling of round and domed workpieces. Extra deep vacuum suction cups can be seen as a compromise between standard cups, which perform best with flat, solid surfaces, and bellows cups, which can handle even heavily corrugated surfaces with a large curvature at the expense of agility.
All types of vacuum suction cups manufactured by Festo are available in many different sizes, and it’s advisable to always use a slightly larger cup and work at a lower level of vacuum force to ease the requirements on the vacuum pump.
To make an educated decision about the size of a vacuum suction cup, calculate its lifting capacity (F = P x A) and multiply it with the appropriate safety factor (2 when the cup face is in the horizontal position and 4 when the cup face is in the vertical position).
For more complex motions or orientations, additional variables should be taken into consideration to determine the correct vacuum suction cup size, including acceleration forces, workpiece surface coefficient of friction, and the weight of the workpiece:
- Horizontal suction gripper position, vertical direction of movement: FH = m x (g + a) x S
- Horizontal suction gripper position, horizontal direction of movement: FH = m x (g + a/μ) x S
- Vertical suction gripper position, vertical direction of movement: FH = (m/μ) x (g + a) x S
FH = Theoretical holding force of the suction gripper (N)
m = Mass (kg)
g = Acceleration due to gravity (9.81 m/s2)
a = Acceleration of the system (m/s²)
S = Safety factor (minimum value is a safety factor of 1.5)
μ = Friction factor (0.1 for oily surfaces, 0.2–0.3 for wet surfaces, 0.5 for wood, metal, glass, and stone, 0.6 for rough surfaces)
Materials
Festo offers the following options for its vacuum suction cup materials:
- Nitrile-rubber (Perbunan): suitable for even, oily workpieces.
- Nitrile-rubber antistatic (Perbunan antistatic): suitable for electronics.
- Silicone-rubber (Silicone): suitable for food products.
- Polyurethane (Polyurethane): suitable for workpieces with a rough surface.
- Flouro-rubber (Viton): suitable for industrial high-temperature applications.
- Polyurethane wear-resistant (Vulkollan): suitable for high-stress applications.
While all these cup materials are suitable for gripping workpieces with even surfaces, only polyurethane can handle rougher surfaces like wood or stone. Polyurethane has very high wear resistance compared with other vacuum suction cup materials, but it’s quite expensive to manufacture.
Nitrile-rubber, on the other hand, is very economical, making it the go-to choice for general industrial applications. Its other major advantage is excellent oil and chemical resistance. Festo also offers an antistatic version of its nitrile-rubber vacuum suction cups for handling sensitive electronics.
The temperature range of nitrile-rubber vacuum suction cups makes them usable even for injection molding, but silicone is generally seen as a better choice because it can handle both hot injection-molded parts as well as frozen packaged foods thanks to its impressive temperature range (from -30 to 180°C). The FDA has even cleared silicone for direct contact with food and drug products. Another important advantage of silicone vacuum suction cups is that they don’t leave marks on surfaces, a common issue with nitrile-rubber cups.
But silicone vacuum suction cups are not without their downsides. First, they tend to cost between 30% and 50% more than nitrile-rubber cups. Second, their wear resistance is very poor. For high-stress applications where surface marking is not acceptable, such as in the automotive industry, polyurethane is the best choice. Of course, the suction effect (which is often the cause of surface marking can also be prevented with better control over the vacuum flow and modern Vacuum Grippers like Robotiq AirPick and EPick.
For industrial high-temperature applications where outstanding chemical resistance is required, fluoro-rubber vacuum suction cups are an easy choice because only they can resist ethanol, alcohol, isopropanol, water, acid (10%), and alkaline (10%).
Conclusion
Vacuum suction cups are easily overlooked, but the role they play in the design of every vacuum-handling system is absolutely critical. While selecting suitable vacuum suction cups for your application may seem complicated at first, all you need to do to make the right choice is follow our guidelines and carefully weigh the pros and cons of each option available. By combining the right vacuum suction cups from Festo with modern Vacuum Grippers from Robotiq, you can say goodbye to boring, repetitive tasks and increase your productivity and quality alike.
Leave a comment