6 Powerful Strategies to Improve Manufacturing Process Efficiency
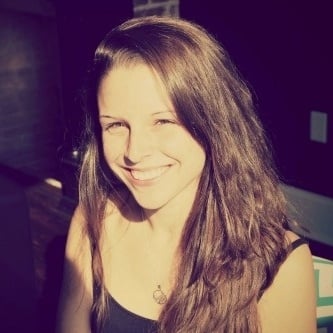
Posted on Feb 26, 2019 in Manufacturing
6 min read time
A process is a repeatable aspect of business operations that can be optimized to boost efficiency. In a manufacturing setting, keeping a high level of efficiency is especially crucial because doing so directly impacts total output, customer satisfaction and more. Making gains with process efficiency takes time and concentrated, ongoing effort. Here are six strategies you can use to improve process efficiency in your facility.
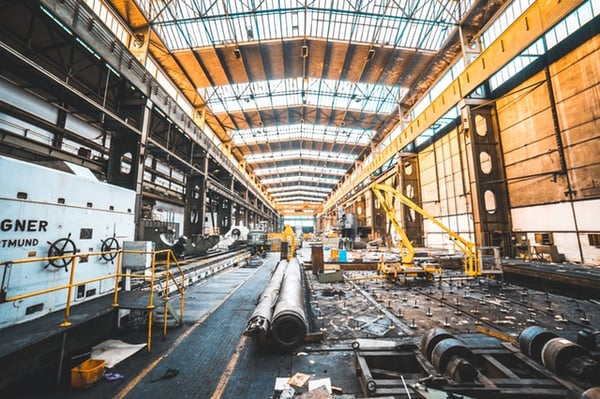
1. Dig Into Data and Use It to Illuminate Areas of Improvement
Not long ago, manufacturers that collected information about operations only had isolated data sets. Now, it's possible to dig into data and see where existing processes break down or determine the conditions required for maximum efficiency.
In one case, a mining company used data to learn that the best performance occurred during peak oxygen levels in the mine. Then, the establishment altered its leach recovery process and increased the average yield by 3.7 percent in three months. Without looking at the data in depth, the company might not have known which aspects of its process to tweak to see such gains.
Getting started requires picking a problem that data analysis could solve, such as a process that’s continually cost-intensive. Next, all aspects of that process must be accurately measured. Finally, the last step is to look at the data and determine how to make improvements based on the findings.
For example, it may become clear that people go through too many unnecessary steps when tweaking a machine to make it perform different functions. In that case, the fix might involve improved employee training or investing in enhancements to the equipment that make it more versatile.
2. Take a Team Approach to Goal Achievement
When setting goals at a company, it's smart to figure out where bottlenecks exist and assign a dollar value to them. There are various ways to identify bottlenecks. They include:
- Finding the machine or the step that uses the highest percentage of its capacity. It is the bottleneck.
- Locating the machine or the process that has the longest wait times. The previous machine is the bottleneck.
- Determining areas of backlogged work. Tracing the source of backlogs identifies backlogs — which are caused by equipment as well as people.
Tackle the most expensive bottlenecks first. Then, task teams of employees with working toward goals that eliminate or reduce those problem areas.
Roll out the implemented changes gradually to avoid significant disruptions to the existing processes. Then, communicate with each team regularly to see if it's getting closer to the intended goal or if it's time to do things differently.
A team management method known as Command and Control gained popularity throughout the 20th century, but because it involved team leaders ordering employees to do things and punishing them if they refused, it contributed to low morale.
A more favorable team communication method is called Engage and Create. While using it, a team leader seeks input from team members and values their contributions. Additionally, all team members engage with other workers and understand everyone has a valuable role to play. A team management style called Interested Engagement also focuses on listening and responding to team feedback. It’s similar to Engage and Create because it also prioritizes working together.
If using a team management method such as Engage and Create, assigning milestones to groups through a project management app allows people to take ownership of tasks in ways they may not do individually.
3. Recognize Employee Engagement as a Way to Improve Process Efficiency
Process efficiency suffers if employees don't feel engaged in their work or are not able to collaborate with others. It may also take a downturn if people regularly participate in incorrect practices because of inadequate training.
Workers at the Weetabix Food Co. took part in Rapid Lean process improvement programs from Lauras International that emphasized training and coaching of operators, technicians and front line managers. They also designed improvement plans and charters. Moreover, the company introduced its Rapid Lean processes at the plant, and staff members attended relevant workshops that were several weeks long.
Ultimately, the company improved output by more than 50 percent and reduced waste by 80 percent. Those results show how worthwhile it can be to focus on employees when improving processes.
4. Explore Robotic Process Automation
Robotic process automation (RPA) involves using software to automate manual tasks and get rid of substantial amounts of repetition for employees. Statistics projected that worldwide spending on RPA would reach $898 million in 2018, representing tremendous growth over the 2017 expenditures totaling $542 million.
Some manufacturing-related tasks that are typically a good fit for RPA include purchase order processing, transportation management and regulatory compliance. Robots and cobots can also be installed on factory floors to aid workers in completing their tasks faster than before the equipment existed.
Atria produces vegetarian and gourmet food and depends on cobots to assist with packaging and palletizing processes. Switching to different packaging applications for various types of food took six hours without using cobots but was reduced to only 20 minutes when depending on those machines.
Since there are so many ways to apply RPA in a manufacturing plant, it's necessary to thoroughly investigate all the possibilities before choosing one. After going through that stage, it should become evident which options are most appropriate. RPA is particularly useful for improving error-prone processes.
5. Develop a Schedule and Standards for Routine Maintenance
Even the most efficient processes fall short when machinery breaks down due to insufficient maintenance procedures. That's why it's crucial to view equipment maintenance as an integral part of process efficiency.
Begin by planning a schedule of routine checks for each piece of equipment. Next, set standards regarding the conditions that may necessitate more immediate inspections. For example, if team members notice unusual wear patterns, abnormal levels of tension or other strange characteristics of a machine's components several times in a short period, it's probably time to be proactive and investigate further.
Another way to connect process efficiency to routine maintenance is to ensure all team members know the correct ways to report problems. They need to know which channels to go through to notify superiors of suspicious findings, how to submit reports and other necessities. Bringing clarity to each step helps prevent mistakes and enforce uniformity.
Here are some basic steps to follow when bringing uniformity to the equipment maintenance process:
- Create a template that includes all the necessary steps for maintenance, broken down by the piece of machinery or type of machine (Cooling, assembly, etc.).
- Indicate how often to perform each maintenance check (daily, weekly, annually, etc.).
- Create a row or area where a person can sign or initial and provide a date for each maintenance check performed.
- Include a section at the bottom of the maintenance record that indicates a contact name or number that the person performing the check should use if they notice anything unusual about the equipment.
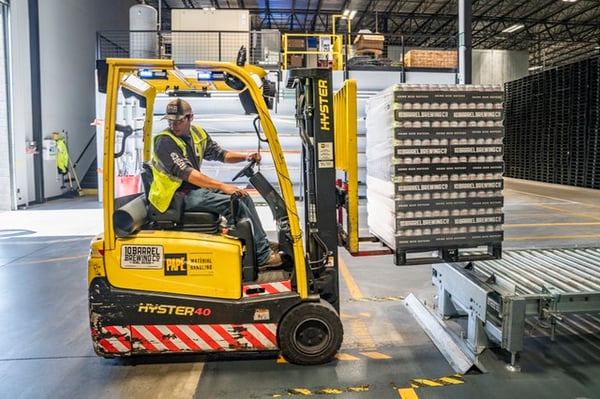
6. Change the Factory Floor Layout to Cut Out Unnecessary Movement
Excessive movement by employees in a manufacturing plant can hinder productivity and cause other disruptions. Consider strategically rearranging the factory floor layout so it allows people to do their jobs with limited amounts of movement. Get started by removing unused tools from the area and setting up the ones employees need in ways that make sense for the jobs they perform.
See if there are ways to shorten the path of travel by adjusting the placement of the equipment in instances where employees must move components between machines. In 2016, Honda tried an innovative upgrade to the traditional assembly line layout with its assembly revolution cell (ARC) line. It has a moving conveyor holding a vehicle and a complete set of parts laid out in a sequence. Four assemblers then step onto a platform and ride around a U-shaped cell to put the car together. Each employee handles several tasks along the assembly line, thereby broadening the assortment of responsibilities dealt with by each person. Honda says this setup increases the assembly line efficiency by 10 percent and reduces material handling by the same amount.
Stay Dedicated and Anticipate Positive Results
These suggestions won't cause overnight improvements, but they're worth trying as part of a longstanding commitment to enhancing process efficiency.
No matter which ones you go with, don't forget to seek feedback along the way.
Process improvement is something manufacturers often don’t know how much they need until they get started and notice the favorable outcomes. The tips here offer information to stimulate success, especially when people stay positive and think about the advantages of higher efficiency within their facilities. Flexibility and a willingness to adapt will help entities thrive.
Leave a comment