Machining with Industrial Robots
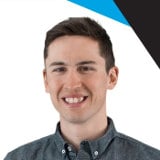
Posted on Nov 23, 2014 in Robots
4 min read time
The machining world has been using robots for a little while. Mostly to do machine tending. Although, with a lot of technological progress, industrial robots are now ready to do machining. In fact, with processes that must deal with more crazy shapes and differing rigidities, an industrial robot can be a great alternative.
How Machining is Usually Done?
Traditionally machining is done by using a milling or a turning machine. The first one is a tool that turns at a given RPM and removes material from a raw part. A milling machine can have from 3 to 6 axes. A turning machine is the opposite, the raw part is turning around an axis and the tool stands still (most of the time) and removes material from the part. There are other subtleties and details but this is basically how it is done.
These machines which can be huge are normally placed on a workfloor with a proper power supply, air supply and coolant fluids. The parts are placed ''inside'' the machines. So the machining area can be limited to this sometimes much smaller space.
CNC machines, are automated machines that run a particular program and work on the part that is placed in the workspace. This market is always evolving, bringing in new models, adding axes and ways to do the job more easily. CNC machines are now equipped with tool changers and pallet changers which means the machine can virtually always be working on a part.
Why not use a 6-axis milling machine?
With the requirement of more complex shapes in the manufacturing process, it is sometimes hard to get the desired shape using the classic machine. In some applications, it is just not possible to use milling or turning machines because the part is just too big for the machine.
The solution to this problem is to use 6 or 7-axis industrial robots. Although, depending on the application a lot of rigidity might be required. You want your robot to be as accurate as possible. With backlash, robot warm-up and other factors; the robot often has to be regularly re-oriented to have sufficient precision. Vision systems can be used to get the robot to the right spot at the right time.
Vision System
To have good results in machining, rigidity is the key. With the enormous potential force that is applied on the tool, the robot always has some kick-back and often has to be re-positioned. Even though this seems simple, it must be re-placed exactly. So how can this be done? Well, external vision systems have been developed to re-position the robot at the right spot when problems occur.
The vision system can measure the position of the robot at a very high interval and realign the piece where it should be. The precise path has been pre-programmed and the robot should be right in line with where it needs to be, the vision system makes sure that the robot is always at the right spot. This allows the robot to have a good accuracy and precision. To learn more about accuracy and precision, read the following article.
With a vision system this means that the footprint of the robot can be a smaller than the footprint of a classic CNC machine.
Aircraft Machining Using Robots?
Aircraft use rivets to fix the cabin to the aircraft frame. This process is very old and was initially done by workers that were using drills. Now with the introduction of materials like composites and titanium it is harder (literally) to drill the aircraft frame. Aircraft manufacturer are now using mobile robots rigid enough to drill holes precisely. The system is using a vision system to locate the hole. The operator can then relocate the robot to drill to the exact spot. Watch the next video, it is quite impressive. This is the very definition of collaborative manufacturing.
This process couldn't have been done in a machine, because the parts are too big. And rigidity with the robot arm was needed to get a great result on the part. Industrial robots were the key to success in this case.
Grinding/Finishing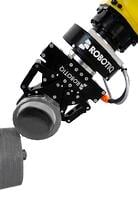
Finishing refers to all the polishing, sanding, grinding and other operations that are done after the machining process. With the introduction of the force torque sensor it is now possible to execute these applications using a robot that is force controlled. This means each and every part will be polished the exact same way. As the path as been pre-determined, the force torque sensor limits the force applied on the part which produces a consistent result for each part.
Machining is a growing area for automation, particularly if we want to reshore manufacturing jobs, so hopefully, this has given you some food for thought. Seriously, to get more information on force torque sensors in the robotic world or if you want to see what the different applications this device can be applied to, take a look at the link below.
Leave a comment