Job Shop vs Flow Shop: Can Robots Work for Both?
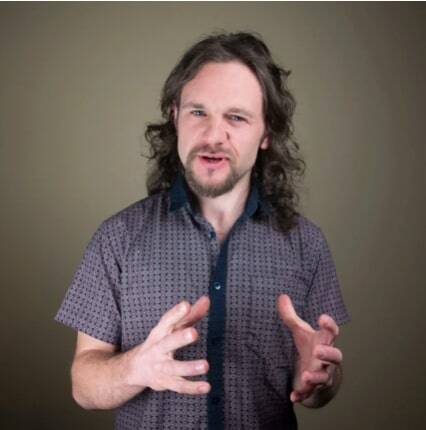
Are robots feasible for high-mix, low-volume job shops? What is the difference between job shops and flow shops? Here are the answers.
Motoman calls it your "manufacturing DNA" — the route your products take through your process.
Do you run a job shop, a flow shop or a mix of both? The question is fundamental when you are considering introducing robots. If you have a job shop, you might worry that collaborative robots aren't for you. How can you automate processes that are constantly changing, right?
Let's have a look at how collaborative robots apply to these different environments:
What Type of Shop Do I Have?
Job shops, flow shops and the other types of "shop" are a way of describing the route that products take through your manufacturing processes.
If your products move through a linear, unchanging sequence of steps — with one operation per machine — you probably have a flow shop. If your products move from machine to machine in a manner that you could call "all over the place" you might have a job shop. Or you might have another type of shop entirely.
Flow Shop
High-volume manufacturers (e.g. automotive) traditionally use a flow shop model, with each stage happening in exactly the same order every time.
The key to flow shop scheduling is that the product goes through each step of the process only once. If the product needs two drilling operations, for example, you will have two drilling machines.
Some advantages of flow shops are:
- Easy to automate — It is simple to apply robotics to a flow shop because the steps are consistent and repetitive.
- Easy to measure — Many manufacturing KPIs (Key Performance Indicators) are designed for flow shops.
- Easy to optimize — As a result of being easy to measure, it is also easy to tell which stages in the process need to be optimized and there are clear solutions for dealing with unoptimized steps.
Some disadvantages of flow shops are:
- Low flexibility — Flow shops are great for a production line, but if your products are continuously changing your process will be hard to standardize into a consistent flow.
- More initial work — It takes a lot of work to set up a flow shop at the beginning. The investment is also high because of the need to have a machine for each operation.
- Hard to increase capacity — Imagine you start getting big orders from a customer. With a flow shop, it can be difficult to boost capacity at short notice. You may have to invest in a whole new production line, which is risky if the customer orders suddenly drop again.
Flow shops have used robots for many years. Due to their consistent operations, it is easy to identify where robots could help the process.
Job Shops
Most small machine shops deal with high-mix, low-volume products and often use a job shop model. Machines are grouped by functionality and the product moves between them as and when they need to, often passing through the same machine several times before it leaves the machine shop.
Products do follow a "flow" (of sorts) but it is usually unplanned — or only loosely planned — and it rarely stays consistent.
Some advantages of job shops are:
- Easy to set up — Small businesses often implement jobs shops because they are simple to set up and the initial investment is minimal. You can begin with one or two machines and add them as needed.
- High flexibility — It is easy to add, change or remove stages in the process. If a part needs to be re-machined, it is simply sent to the corresponding machine.
- Easy to increase capacity — Because it is easy to add a new machine to a job shop, you can increase capacity incrementally by adding a new machine.
Some disadvantages of jobs shops are:
- Hard to automate — Traditionally, it has been very difficult to automate job shops because automation has required consistency. This is starting to change, as we discuss below.
- Hard to schedule — Scheduling in job shops is notoriously hard. Most of the time, it is done on-the-fly. This causes a lack of standardization, meaning that the same product can take wildly different times to pass through the process.
- Hard to measure and improve — The inconsistent nature of the process makes it difficult to measure the different stages of the process, which means that improvement of job shops is also a challenge. Improvements are often tackled haphazardly — e.g. "The lathe has got a big backlog. Let's get a new lathe." — rather than by trying to optimize the stages of the process.
Another consideration for job shops is that they require more skilled workers than many flow shops. Depending on your situation, this might be an advantage or a disadvantage. However, we usually think of it as a good thing.
Consider what Sequoia Automatic's manager Dennis J. Burke said when he introduced robots to their job shop:
"It's easier to find employees willing to run several robots than it is to find a worker willing to load and unload a machine tool all day long. We can sell ‘thinking jobs' to prospective employees; it's harder to sell non-thinking, monotonous jobs."
Job shops are traditionally a challenge for robots. However, this is starting to change.
Other Shops: Group Shops, Open Shops and Project Shops
There are other types of routing which you can find in manufacturing. For example:
- Group Shops (aka Hybrid Shops) — In practice, most processes fall into this category — a mix between flow shops and job shops. They incorporate batch processing on common operations.
- Open Shop — These have no scheduling at all, which makes them a bit of a "free for all." Operations can take place in any order, which means they are very flexible but hard to optimize in practice.
- Project Shops — In contrast to job shops — where the product moves from station to station — project shops perform all operations in the same location. Product stays in place and material comes to it. This may be a suitable model for a DIY kitchen project, but it is usually not efficient for manufacturing processes.
Applying Collaborative Robots to a Flow Shop or Job Shop
Traditional industrial robots required consistent, repeatable tasks. In the past, this has meant that they were only suitable for highly ordered flow shops. The initial investment was high and it took a long time to set up the robot.
That has all changed since the introduction of collaborative robots.
Collaborative robots can be used in job shops as easily as they can in flow shops — well… almost as easily.
Cobots have several advantages which means that they can overcome the challenges traditionally associated with automation in a job shop:
- Quick and easy to reprogram — Cobots are inherently flexible which means that they do not reduce the flexibility of the overall job shop.
- Can do several tasks a day — You can move a cobot to a new workstation in a matter of minutes, which makes them as compatible with job shops as human workers.
- Especially good at batch processing — Even if you only incorporate a few batch processes, cobots can help to boost the performance of these tasks. You can introduce flow concepts incrementally, without disrupting the overall job shop model.
Yes, job shops were traditionally a challenge for robots. But with collaborative robots, there is now no reason not to introduce automation into your machine shop, whether you have a job shop, a flow shop or something else entirely.
Do you have a job shop, flow shop or something else? What concerns do you have about applying collaborative robots? What tasks are challenging for you to apply automation? Tell us in the comments below or join the discussion on LinkedIn, Twitter, Facebook or the DoF professional robotics community.
Leave a comment