Industry 4.0 – What Is It? And What’s In It For Me?
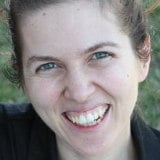
Posted on Mar 21, 2016 in Manufacturing
6 min read time
So you’ve heard about Industry 4.0, or “smart manufacturing” or whatever it’s called where you live. Industry 4.0 is a term that originated in Germany a few years ago, and it’s meant to represent the fourth industrial revolution – what were the first three, you ask? 1.0 was water and steam power; 2.0 was electric power; and 3.0 was computing power, part of which includes industrial robots. Industry 4.0 is still just a concept – let’s say, a vision of what’s coming next, in order to focus on the development needed to get there. Estimates vary, but the first ‘Industry 4.0 factory’ will probably see the light of day in 2020.
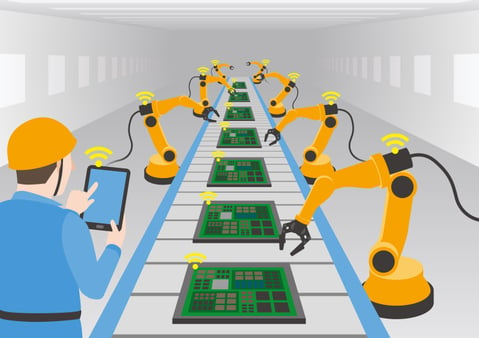
TODAY...
So let’s look at what exists today. What are the changes you can make today to have a state of the art factory? On one hand, there’s the automation of individual processes. Using a robot to load parts, adding a camera for inspection, automating a welding process, etc. On the other hand, there’s the digitization of the data from various steps of the production process. You can register feedback from an individual process, record temperature and pressure levels, manage supplies, etc. Statistics can be collated from all this data, therefore enabling management to analyze and optimize the process. Various levels of digitization are possible, as is represented here in an example automation pyramid.
Image: automationinside.com
So as we speak today, most companies manage these two aspects of automation as two separate areas, probably because they refer to two different sets of expertise: automation on one hand and IT on the other. Watch this video for an example factory of the future application.
... AND TOMORROW
With Industry 4.0 comes the rupture of our existing production mode: instead of having a vertical integration, with ERP systems (enterprise resource planning) helpful for long term scheduling, MESs (manufacturing execution systems) keeping track of things a little closer to the production and SCADA (Supervisory Control and Data Acquisition) interacting directly with production; we foresee a horizontal integration: every unit is connected to the network, so it can interact directly with every other unit. It’s the concept of the Internet of Things: intelligent machines, the warehouse management system, the production system and the manufactured product all connected together on the same network. Of course, you still need a global construct to tie everything together, i.e. you need a high level display of the relevant information coming from everywhere.
For example, a machine at step 3 of a production process could alert other machines from steps 4 and onward that the production will be delayed a bit because there’s an urgent fix that needs to be done on the machine at step 3. Of course, there will still be humans interacting with the machines in this manufacturing process. A production plant manager will still manage the plant, but s/he will have more data coming from all the machines, therefore enabling a better use of resources, better scheduling of maintenance, delays, etc. Based on current technology, I picture this person located in the middle of the plant, with a tablet in hand, looking at all the data coming in from the machines, taking in all the information coming in verbally from the employees, and making decisions based on this data: adjusting the production schedule, ordering supplies and adjusting employee assignments all according to the current plant conditions.
In the future you could include 3D printers that facilitate a custom based approach, and you can sit in your living room, choosing (or even designing) various options for your brand new car (or other consumer goods). At the other end of the line, in the manufacturing plant, a machine analyzes your order, checks if the raw materials are available, checks if all the steps of the production process are feasible, queues your order if everything fits, and tracks the whole process, from your order to delivery. So it’s Amazon’s warehouse (with independent mobile robots that carry items and packages around based on orders placed by customers on the internet) meets the automated factory.
Image: Global Success Club
THE CHALLENGES
OK, that’s still a few years away at the moment, and it might not be exactly like this, but you get the idea. Industry 4.0 is actually a concept, which has the strength of focusing the development efforts in the right places. Once the concept is defined, we can see where the system fails to perform, and this is where the effort for improvement can be concentrated. For example, cybersecurity is one area that needs to be focused on. We don’t want manufactures to be hacked, as has been the case lately in a few hospitals. So, intelligent management of huge amounts of data is another area that needs development. Developing a communication standard is also an issue. Imagine if every manufacture developed its own way of doing things… what a mess that would be! There’s an initiative in the United States, called the "smart manufacturing platform" that aims at developing just such a standard. It’s defined as a platform that will be similar to an app store. It will be possible, eventually, to take or contribute to the platform with bits of software that will be useful for a factory – e.g. you have developed an interface that displays statistics that are especially useful in the pharmaceutical industry, and you make it available on the “smart manufacturing platform”.
So, aside from the exciting idea of being able to customize your car from your living room, what are the advantages of Industry 4.0? Well, since you have real time data, you can spread the effort and resources more accurately. So productivity is increased, and the use of raw material is optimized. The quality of the final product should also be improved; if the data coming from process #8 shows that the real value used always has an offset from the set point, then the design plans can be adjusted accordingly and the simulations as well. This will enable a simulation that actually corresponds to reality, and eventually a product that is closer to its original design. Adaptability is a big plus in Industry 4.0. I really like the analogy with Formula One racing from Ken Young (Technology director, The Manufacturing Technology Centre in the UK):
“The cars are going around the track with thousands of sensors and every time it goes past the pit wall they download a load of data, and the race engineers tell the driver how to drive in response to that data. That’s what we’ve got to do to our factories, we need to have that pit wall somewhere to make sure that your machinery, your systems are working better than the next guy’s.”
Now let’s look at the down side: every solution has its drawbacks. The cost of putting in place such digital infrastructure can be impressive. If you have one production line and only a modest quantity of products made on this line, then automating it from A to Z might not be profitable. Then again, it’s hard to tell without a proper feasibility study. Another disadvantage to complete automation and digitization of your processes is ending up having more data than you can actually use, and becoming confused instead of more productive. This is related to the big data challenge that I mentioned earlier.
OK, so you get it. A modern factory with all the steps automated and interrelated, with operators on their tablets tracking on going production, that’s where we’ll be in a few years. But what can you do to help get there today? Here are a few suggestions:
- Familiarize yourself with the technologies available today. The more you fall behind, the greater the gap will be when you decide to get on board with technology.
- Stay aware of the global strategies of Industry 4.0, in your own country and abroad.
- Think of Industry 4.0 when you acquire new equipment; a sensor with an Ethernet connection will eventually be useful to connect to the rest of the factory.
For more information visit our resource center.
Leave a comment