How to Tidy the Mess with Good Robot Cable Management
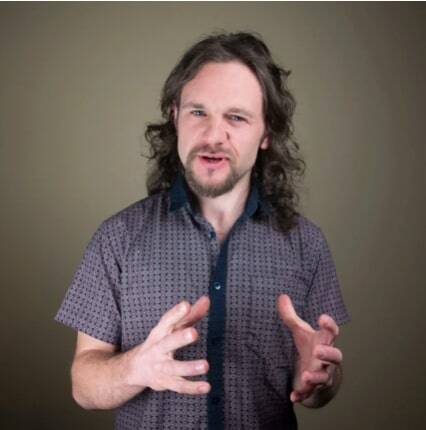
You don't want to break your robot cables due to bad routing, right? Robot cable management can seem complex because robots can move in so many ways. But with the right approach, your cables can last for years.
Good cable management is vital when you are working with robots.
You might imagine that the worst situation is when a cable is routed so badly that the robot rips it apart. However, there are more problematic scenarios, such as when the cable is damaged imperceptibly and it causes the robot to behave strangely.
Unlike with other types of cable routing, robot cabling problems are hard to fix on the fly. Because robots are autonomous, the robot could break a cable before you even have time to realize or react.
The solution? You need to be proactive with your robot cable management.
Why robot cable protection is so important
You can think of cables as being a bit like your robot's "lifelines."
If those lifelines are working properly, the robot will be "healthy" and function as intended. If they are damaged, the robot is compromised and there's a danger it could start to move erratically. This would make it a liability, either to itself and other equipment or to human workers.
There are 3 main types of cable you will find on a robot:
- Power cables — For electric robots, these provide electricity to power the robot and its tool.
- Communication cables — These carry communication signals to the robot and tool, as either digital or analog signals.
- Pipes — Some tools require extra fuel to operate. For example, Robotiq's EPick and AirPick vacuum grippers use pneumatics so they require pneumatic pipes. Other tools might require pipes for hydraulics, gas, or another fluid.
If any of these cables is compromised, it will likely impact your production. You will need to stop the robot, test it to identify the problem, and repair the damage. This takes valuable time.
As David Rochette, technical trainer at Robotiq, explains in our cable management course:
"Depending on your end of arm tooling, you can have multiple types and configurations of cables going to the robot's wrist. Installation of these cables is very important.
"You should be able to run your robot for production purposes and make sure not to experience any downtime caused by damage or unwanted breakage of cables."
6 common failures that can occur in a robot cable chain
According to IGUS, one of the world's leading manufacturers of robotic cabling solutions, there are 6 common causes of cable failure.
These 6 failures are:
- Loss of continuity — The electrical continuity of the cable is compromised. David explains that these defects usually occur over time, due to an accumulation of small misuses. They can be hard to troubleshoot as the effects are often intermittent.
- Insulation damage — The electrical insulation around each cable is damaged, which can lead to short-circuiting between two or more wires.
- Corkscrewing — The entire cable is twisted and deformed. This type of failure affects cables constructed in layers more than bundled cables.
- Jacket abrasion — The outer jacket of the cable wears through to the underlying cables or shielding. This can reduce the cable's resistance to both environmental components (such as dust or oil) and electrical interference.
- Jacket swelling/cracking — When the cable is exposed to the wrong oils, chemicals, or temperatures the jacket can swell and crack, reducing the protective properties of the jacket and potentially damaging the wires
- Shielding losses/EMI — When the electrical shielding of a cable is compromised, it can lead to Electromagnetic Interference (EMI) which can degrade the performance of the cable.
What effects do these failures have on the operation of your robot?
It varies. Sometimes, there will be no noticeable effect for a long time as the continuity of the cable is preserved. However, working with damaged cables is a ticking time bomb. At some point, the cable will fail.
Whenever you find that a cable has failed, you should replace or repair the cable and ensure that the same failure cannot happen again.
The most common mistake when routing robot cable
There are a few best practices when routing cable up the arm of a robot.
David describes how the most common mistake that we see people making when routing cables to Robotiq tool is when they use standard plastic cable ties:
"You'll want to have the cables tied up all the way from the robot's wrist to the controller so that they don't get in the way and the robot can still reach all possible positions without damaging them.
"The most common mistake when using cable ties is to tighten them too hard. This can cause internal damage to the cable or its jacket even if you don't see it."
Although cable ties are a very common way to fix cables to a robot arm, David explains that they are not the recommended solution.
He says:
"Velcro ties are a better alternative as they are less aggressive to the cable. Using cable clip holders is also an appropriate alternative.
"If you really have to use plastic cable ties, interlacing two of them — one around the arm and the other around the cable — is a safer option for the cable."
Check out our free course on robot cable management
Do you want to learn more practical tips on how to route your robot cable more efficiently?
David Rochette has a whole free course on robot cable management over on the Robotiq eLearning platform.
The course includes lessons including:
- The most important components of a robotic cable.
- A detailed view of the 6 common failure modes of a cable.
- How to choose the right solution for your needs.
- An overview of specific Robotiq cables.
- Practical recommendations for a clean installation
You can get instant access to David's course over on the eLearning platform.
What questions do you have about robot cable management? Tell us in the comments below or join the discussion on LinkedIn, Twitter, Facebook, or the DoF professional robotics community.
Leave a comment