How Long to Payback my Robot Investment?
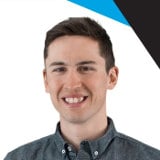
Posted on Mar 09, 2015 in Robots
6 min read time
We often get asked: ‘What is the cost of a robot?’. As there are a wide range of applications, robot brands, robot models and robot accessories out there, it is almost impossible to answer this question. The question I'm asking back is: How long will it be before your robot investment is paid back? At the end of the day, this is all that matters. If you invest half a million dollars in equipment, but the payback is completed in 6 months... it's worth it. It is the same situation for robotic devices. Here are some tricks and tips on how to calculate your return on investment (ROI) for a robotic cell.
The main limiting aspect of introducing a robot for a company is the starting investment and the learning curve necessary to get the most out of it. Depending on the project, you might be able to repay your project within a year. Aside from the financial aspects, you should also consider that the introduction of robots into a manufacturing process can also mean production enhancement. In fact, as the robot will help employees to achieve their work, there is less stress and more ''value added'' to jobs that can be done on the product. For example in machine tending applications, removing the employee from loading tasks allows him/her to do quality control, setups and machine maintenance. This will add value to your product without any supplementary effort.
Here is a simple calculation to determine how long it will take to pay off your robotic investment. Please recognize that this a rough calculation and should be considered as an estimation and not a precise calculation. To increase comprehension, an example will be used for each step of the analysis.
Baselines
The baselines are the actual data from your production. It consists of the costs related to the employee operating the machine or doing the potential robotic application. It also includes all the different costs related to the use of the machine.
- Yearly Cost = Employee [Unit] * Shift [Unit] * Salary [$] + Downtime [$] + Scrap [$] + Jig [$]
- Number of employees on a shift [Unit]
- Number of shifts per day [Unit]
- Employee yearly salary and benefits [$]
- Cost related to downtime [$]
- Cost related to scrap parts [$]
- Cost related to jig or process enhancements [$]
Example: If you want to analyze the situation of a single machine being fed by a robot, you will look at the data for this very machine. So there is 1 operator, working 40 hours per week at a cost about of $50,000 yearly. The machine is fed on two different shifts. In this case, the process cost $7,500 in downtime, $5,000 in scrap parts and $7,500 in jig and process improvement.
Yearly Cost = 1 (employee) * 2 (shift) * $50,000 (salary) + $7,500 (downtime) + $10,000 (scrap) + $7,500 (jig)
Yearly Cost = $125,000
Investment
The investment includes all the different peripherals for the robotic cell. The different costs related to transportation, taxes and integration are also included in the basic investment. Of course you want to get the lowest starting investment, but you also want to have good quality. Always keep in mind that most of the time, a higher quality robotic cell will be more reliable and will require less maintenance.
- Robot [$]
- Gripper [$]
- Parts presentation fixture [$]
- Vision system [$]
- Monitoring system [$]
- Other peripherals (Force-torque sensor, automatic measurement system, automatic door, automatic chuck, etc.) [$]
- Cleaning system [$]
- Physical barriers [$]
- Robot to machine interface [$]
- Integration [$]
- Taxes, transportation fees... [$]
- ...
Starting Investment = Robot [$] + Gripper [$] + Vision system [$] + ...
* Make sure to do a proper risk assessment when integrating a robot into a workshop. The analysis should be done in accordance with ISO-10218. You should also notice that there is a huge gap between the use of a collaborative robot and an industrial robot. In fact, collaborative robots will require very few external devices to work properly. In the case of an industrial robot, it will require fencing, external safety devices and it will occupy more space.
Example: This case will be using a Universal Robots (UR 5 model) that costs about $35,000, a Robotiq 2-Finger 85 Adaptive Gripper ($4,800) with a simple part presentation fixture ($1,000). A cleaning device ($800) some visual safety devices to prevent contact with the robot* ($500). Interfacing the robot to the machine will require an extra $1,000 and the integration price will be about $2,000, plus the applicable taxes and transportation fees which will ramp up to about $4,000.
Starting Investment = $49,100
Potential Scenario
The future situation is always an estimation. In fact, if you haven't experience a robotic integration in your career, it might be hard for you to evaluate this scenario. However, there are some good guidelines that can help you to figure out this situation using the same data as the baselines, however, now the values are different.
As a rule of thumb, the employee that was operating the machine or the working post will not be removed completely. In fact, the robot is there to do the redundant work and leave the more important tasks to the worker or to let him/her concentrate on other value added tasks like quality control. So instead of one employee using a machine, the employee can operate several machines at a time. The number of shifts and the employee salary will remain the same. The different costs can vary in accordance with the process enhancements.
- Number of employees on a shift [Unit]
- Number of shifts per day [Unit]
- Employee yearly salary [$]
- Cost related to downtime [$]
- Cost related to scrap parts [$]
- Cost related to jig or process enhancements [$]
Potential Scenario = Employee [Unit] * Shift [Unit] * Salary [$] + Downtime [$] + Scrap [$] + Jig [$]
The production enhancement is the prediction of the production increase over the following years. Since you are introducing a robot into your plant, you may be able to increase your production sometime soon. To accelerate the calculation process for example, you should evaluate the enhancement in dollars instead of number of parts.
Example: The same operator will be using 2 different machines. So there is 0.5 an operator, working 40 hours per week at a cost about of $50,000 yearly. The machine is fed on two different shifts. In the potential scenario, the process costs $1,000 in downtime, $2,000 in scrap parts and $10,000 in jig and process improvements.
Yearly Cost = 0.5 (employee) * 2 (shift) * $50,000 (salary) + $1,000 (downtime) + $2,000 (scrap) + $10,000 (jig)
Yearly Cost = $63,000
In this situation we really want to analyze the ROI without any production enhancement, so the price related to it would be 0$.
Savings
The savings are the difference between your actual situation and your potential situation. This is calculated by the current yearly cost minus the potential cost plus the production enhancement. This gives you the amount of money that you are saving per year. In a classic ROI calculation, your production income would be considered in the calculation. Since introducing a robot cell does not generate increased income, but rather savings, this is the data that will be used.
Savings= Yearly Cost [$] - Potential Scenario [$] + Production Enhancements [$]
Example: Savings = $125,000 - $63,000 + $0
Savings = $62,000
R.O.I.
Finally to know how long it's going to take for your investment payback, you only need to divide the investment by the savings.
ROI = Investment [$] / Savings [$] = Moment the investment is repaid [years]
Example: ROI= $49,100 / $62,000 = 0.8 years
Since the return on investment is done within a year, you can calculate this into months (0.8 years * 12 months/years) = 9.6 months. After the 9.6 months your return for the robot investment can be added to your bottom line as profit, hurray! Now this is why investing in robots is crucial, increased profits and keeping employment at home. Win – Win!
This article was about the calculation of the return on investment for a robotic cell. In other words, how to calculate the time before your investment is completely paid off due to the savings difference that has accumulated from your robotic production improvements. If the different steps have been followed correctly, your ROI should now be calculable. If you want to dig a little deeper into your ROI analysis, we have put together a calculator to help you analyze a wider range of parameters. This will help you confirm your hypothesis and refine your calculations.
Leave a comment