The Future of the Robot Teach Pendant
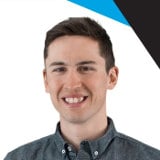
Posted on Mar 09, 2015 in Robot Programming
7 min read time
As we have seen a lot of improvements in the robotic market over the last few years, some may ask; 'What's next?'. In fact, with more user friendly robots, more elaborate geometries and convenient software, the robotic market is constantly evolving. Here is my take on the Webinar titled ''Smartphone simplicity for the next generation of robot users'' given by Bertil Thorvaldsson, a global product manager for software products in the Robotics Business Unit of ABB.
High tech processes such as robotics are constantly evolving. The first teach pendants attached to robots were pretty primitive. In fact, they had an array of buttons, but only a limited number of actions that could be performed with them. With time, pendants reduced the number of buttons, incorporated bigger screens and increase the possibilities of what was capable of being programmed through them. Nowadays teach pendants have very few buttons they are basically just one big touch screen. The possibilities are also virtually infinite. As we follow this evolution in time you might ask yourself, what is the limit for reducing the number of buttons? Have we reach a certain plateau where we have reduced the size of everything and this is what we are going to work with for the next 25 years? Tablets? Smartphones? Really?
ABB thinks it is not just a question of how technology is evolving, but perhaps how we, the users, are evolving. In fact, the next generation of workers (I guess my generation) have grown up using devices such as smartphones, computers and tablets. They are more likely to understand and want these devices in there everyday jobs. Using a big awkward teach pendant is now so old school. New technologies have to be brought to the market to fit the users' needs. Because after all it is still humans who are programming robots, right? Robot companies are now working on technologies to advance the robotic market. Here is a short list of what is 'apparently' going to happen in the near future.
Clouds
Cloud, yes the cloud. The thing that seems to be the next big technology is about to hit the robotic market. With the use of wireless devices such as smartphones, tablets and laptops, the use of the cloud seems logical. Now instead of having a teach pendant connected to a robot, the cloud will be the interface between the user and the robot. This gives people the opportunity to work in a remote location (from your desk or even during business trips). You will be able to monitor and also to communicate with your robot
The use of the cloud can sometimes be controversial, since a lot of people have access, this means that eventually viruses could be put into the system. Work is being done to 'bullet proof' the cloud, so that users can confidently have secure access to it. However another more positive aspect of the cloud is that it allows a community to be built up around robots. Sharing robot programming like ROS or ROS Industrial allows robot programs to be enhanced by community knowledge and experience. In fact, comparing data or programming methods from other users can be a key aspect of this technology. By doing so, imagine that the robot can compare itself to other robots in its community and see if it needs maintenance or can learn a better method of doing something, depending on its use... the possibilities are infinite.
All-inclusive Packages
Since you don't want to have several modules to maintain, program, manage and monitor your robot, manufacturers are creating all inclusive packages to combine as many different technologies as possible into the package.
Engineering: With the virtual elimination of the robot teach pendant, programming can be done from anywhere. In fact, the engineers or robot programmers or even factory workers can program using a 3D modeling interface instead of programming manually. This interface can monitor safety parameters, the interaction between the worker and the robot, collision, or any number of other factors. This is the first step in the process of robot programming and is already used by some robot companies.
Commissioning: This where the logical aspects of robot programs come together. You can sometimes run the program virtually to see the interaction between all the devices and eventually between the robots themselves. This can be a very critical operation, you don't want to launch a production process without knowing if there is a risk of collision or mismatched production speeds and outputs. This aspect is also already used by some industrial robot companies.
Start-Up: This is where the new technology kicks in. With the introduction of smart devices on the work floor, no more need of the teach pendant, except for the e-stop! In my opinion this aspect has to be looked at very carefully. In fact, you can't launch a robot without having an e-stop directly connected to the robot. Can you really trust these smart devices for emergencies? Perhaps other smaller teach pendants can be added to the setup for the e-stop, but if you jog the robot with your tablet and have to stop it, are you going to have enough hands to work the tablet and the pendant? The tablets are cheaper, more compact and more powerful than teach pendants. Additional applications can be fitted on them which then allows you to do a lot different things with them. But are they secure enough?
Supervision: With the use of smart devices and the introduction of clouds, it is then possible to monitor your robotic system from anywhere. So, you can also 'write' to your robot from anywhere. In other words you can have access to the robot program or parameters from your remote location. This would allow you to make adjustments on the fly. Sounds good.
What's Next?
With the constant quest to reduce the size of things and the number of buttons, the next iteration would seem to be the elimination of the device itself. In fact, enhanced reality was introduced in this Webinar and we can interpret this to mean that some robot manufacturers are starting to play with this technology in their R&D departments.
In fact, enhanced reality is just around the corner and could be very practical for the robotic industry. First to program (no need to touch the robot or any devices), then to visualize the safety parameters and eventually to adjust the robot on the fly, as long as your changes remain within the preset security parameters.
We are still in the very beginning of enhanced reality but the next iteration, in the next 10 to 15 years or perhaps even sooner than this, should allow us to move things virtually without any touch devices. This will allow you to liberate your hands and be able to direct a lot of different operations. By following this path, you reduce the number of buttons necessary and you exponentially increase the possibilities of what you can do with your robot.
Let's see what robot manufacturers have to offer in the near future. The thing that I am most excited about is not seeing the development of the technology itself, but rather how fast it will trickle or explode onto the robotic market. Even if the market is always aware of new technologies, so far product life cycles have been quite long. It is not rare to see a robot that has the same look for 7-8 years in a row. Will this technology be retrofitted to older robots... who knows! How much will be invested in this technology? We still have a lot of questions concerning what kinds of robotic improvements will be taken up by industry in the future, but it is fun to be in a field where you can look forward to what is coming and know that these improvements will surely have a positive impact on people and industry.
Leave a comment