Changing Your Robot Programming to Enhance Dexterity
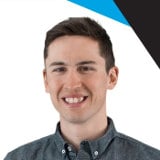
Posted on Sep 02, 2015 in Robot Programming
2 min read time
The main problem with robot grippers is that they cannot achieve the exact same tasks as a human hand. So in most cases you need to lower the level of complexity that can be achieved by your robot. However, even if robot grippers cannot reproduce exact human gestures you can use your robot motion to help your gripper improve its dexterity.
The idea came to me, and the R&D team at Robotiq, by watching this video from MIT where they demonstrate what they call, extrinsic dexterity. Take a look at the video, this isn't rocket science, but it can change your preconceived ideas on how to manipulate objects with your robotic cell.
So if we look at the situation without extrinsic dexterity; it is difficult to grab the rod precisely, since the 2 fingers of the gripper are grasping two round surfaces and the contact points are really minimal. This means that there is a higher likelihood of slippage or dropping the rod, especially if it bumps something or even jiggles on the way to your release point.
With extrinsic dexterity, in this particular case, the gripper rotates the rod until it can grab the rod by 2 flat surfaces which are much more stable than round surfaces. This improves the grippers hold on the rod. The rod’s position is then shifted in the gripper by using another fixed surface to readjust the rode in the gripper’s grasp at a precise point which will allow it to rotate the rod. Once the rod is well positioned in the gripper the robot simply needs to determine where to release the part. Using this method is a bit more complicated, but insures a better localization of the rod at the end of the process and increases the probability that the gripper will succeed in completing its task.
Since MIT is mainly a research lab, we thought it would be cool to help spread this idea. We wanted industrial robot users to see the different possibilities of this application using our Grippers, of course. So, we put together a demo that takes round shaped parts (hockey pucks) that are eventually turned 90 degrees while in the Gripper and stacks them. This program uses iterative processes to determine the position of the next puck to grab and how high to stack it.
An older video was released by Carnegie Mellon University (CMU) a couple years ago. They were pushing the limit of extrinsic dexterity and were able to reposition a part in the gripper using robot acceleration and other external features.
If you need further information on robot grippers or how to fit them on your robot, you might want to take a look at the link below that looks at the 2-Finger Adaptive Gripper and Universal Robots, and how well they fit together.
Leave a comment