Boeing Is Modernizing Its Production With Robots
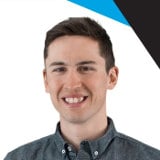
Posted on Aug 14, 2015 in Robots
5 min read time
A couple days ago I was reading this article from Humanoids.io about the introduction of robots in the Boeing manufacturing line. It made me realize that aircraft manufacturers were a couple of years (let’s not say decades) behind the automotive industry. Why would a multi-billion dollar industry leave robots on the sideline for all this time?
The Boeing cell
The robotic cell that will be integrated into Boeing’s manufacturing process is using 3 KUKA robots to achieve fastener installation. The robot located on the outside of the fuselage is drilling holes for fasteners while the two robots inside the fuselage are installing the fasteners. The external and internal robots are aligned during the operation to have a greater accuracy in the process. As you have probably notice in the picture, the robots are fitted on mobile platforms that allow them to cover the total surface area of the fuselage.
55 years after the integration of the first robot in an automotive plant, Boeing is introducing robotic cells in its manufacturing process. Minus the fact that external operations are done with robots, what can explain the gap between the two industries. Is the aircraft manufacturing process too complex to use robots? Are planes too big for robots? Was the accuracy of robots not good enough?
I just want to say that I do not intend to demean Boeing or anything like this. I am just using this example to represent the lack of automation which is rampant in manufacturing processes around the globe. I imagine that even as Boeing has experienced the reluctance to implement robots, other aircraft manufacturers and also manufacturers of other products are experiencing the same problematic.
Production rate
When comparing aircraft markets and automotive markets there is a major difference in terms of volume. A regular automotive plant will produce 40-80 cars a day and a company like Boeing will produce 8.3 planes per months. So if the automotive assembly line wants to achieve this rate, it has to be fine-tuned, have a lot of robots and have suppliers that will work with just-in-time methods using fast and easy materials. For aerospace, it is different, there are still a lot of human operations and an exotic array of parts that need to be produced in small batches because of different constraints, including stiff regulations.
But reading the following sentence: ''These robots drill the plane’s fuselages and place the 50 000 fasteners usually installed manually''. I was amazed. Then I realized that the reason why the automotive industry is so fast is because they are automated, aircraft manufacturers (even if they have a smaller production in terms of numbers produced) still have to hurry up and deliver their planes as fast as possible and then be able to make more planes if they want to be profitable (money rules everything).
The fact that cars are also cheaper to produce and that a higher volume has to be produced to make a bigger margin explains the faster automation rate. This way, car manufacturers could produce more, lower their price and increase their margin.
Size matters!
Yeah, I have to admit that the scale is really not the same with cars as with planes. In automotive plants, robots can be fixed on the ground while the car frames pass underneath them. In the aircraft manufacturing process it is quite different. The plane is mostly stable for several days or weeks and people are working around and inside it. Same for the robots. They have to be able to access all sides of the aircraft’s fuselage and work within the complex geometries of a plane. A lot of vision and other sensing devices, plus advanced algorithms have to be involved to make sure that the fasteners are place at the right spots. To respect different quality standards the job has to be done right and precisely. This is not the same situation in the automotive industry where the vehicle will still work if air enters the cabin, nobody will die. All the potential dangers have to be covered in the aerospace industry and it's probably one of the main reasons why it has taken so much time to close the gap. The manufacturing process has to be proven as being flawless and that's a huge step.
Aerospace is slow
I used to work for a machine shop that was manufacturing propeller parts for an aircraft engine manufacturer and I can tell you that the aerospace industry is really slow. The standards are high and time isn't an actual limitation. They would rather have something done well than something done fast (which I am always thankful for when my plane lands safely). To make a long story short, when the first floor manager had the idea to introduce robots on the manufacturing line, a lot of steps have to be crossed. He has to get approval for the idea, make sure that the budgets are approved, ask the safety department if this is ok with them, ask for the R&D to install a fake cell and do some testing, do some training with the employees and finally install the cell. This whole process (in my own opinion) can be a 2 year process. Adding the fact that the robots are working without any fencing, it might be hard to get approved from the safety department or the labor union.
Safety requirements
Companies like Boeing are gigantic multinationals with more than 165,000 employees and with a lot of rules to protect them. At that size the rules have to be strictly applied. Safety is a huge part of these rules. Introducing a robot can be quite complex for these organizations. Since the robots are working without fencing and employees are nearby, special safety features have to be set so the whole operation is safe. By following the 4 kinds of human-robot safety collaboration, the robots are probably distance and speed limited. This means that if an operator comes close to it, it will slow down and eventually stop to protect the worker from any type of harm. This process can be quite long and complex to be approve with a company of this scale, this might be another reason why it took some time to get integrated. Although, automotive companies are probably as severe as the aircraft ones, so I can't really see the correlation between the size of the enterprise and the fact that it took so much time to introduce robots to the assembly line.
While Boeing is introducing big industrial robots, some other companies are using light weight robots to achieve smaller applications. Collaborative robots are becoming more and more popular in manufacturing processes and in global companies. We have created an eBook on how to introduce these robots in a global company, you might want to take a look.
Leave a comment