5 Factors to Consider Before Moving to a Robotic Welding Process
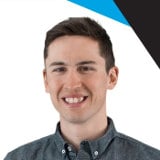
Posted on Apr 02, 2014 in Robotic Welding
5 min read time
Incorporating an industrial automation operation into a manufacturing process can be a scary investment to make. In fact, the money down is quite extensive and the payback must be rigorously calculated. If you want to make sure that you have a good return on investment (ROI), take a look at the 5 factors you should consider before switching to an automated welding system for your manufacturing process.
What kind of welding am I doing?
You should always keep in mind that whatever robotic welding method you are using, robotic welding will be slightly faster than traditional welding methods. However, factors other than speed should also be considered when looking for an automated welding method. In fact, aspects such as: gaps between parts, clamping methods and complexity should play a role in your choice. Having parts with large gaps and complex clamping methods should continue to be done by a manual operator. Jobs with parts that are easier to install on a clamping system and with a standard gap are far more favorable to robotic welding.
When analyzing a robotic welding method, work closely with your robot integrator and determine together if a robotic welding process is sustainable for your parts. In other words, provide a CAD blueprint of the part(s) you wish to weld and look for a reliable solution. Doing this will improve the quality of the planned weld and will determine how the parts and tooling can be well integrated into the robotic cell.
Keep in mind that if you want to relieve a bottleneck or a production problem in your workshop by using a welding robot, you should make sure that the upstream part flow is accurate. For example, if the incoming parts have a high poor quality rate, the welding robot won’t be able to help reduce production problems. Make sure to control your upstream processes before integrating automation.
Have you thought about planning?
Transitioning to automation can dramatically increase production, so you have to be ready to react to such a big change. It may seem strange but, increasing production has to be done after a certain amount of reflection. Once reaching peak production, it might be tempting to buy a bigger industrial robot and a lot of new equipment, but this kind of investment is quite expensive and must be done wisely. Once again, get in touch with your robot manufacturer or robotic systems integrator and discuss your short and long term expansion plans.
Planning can also be seen in terms of short, immediate preparation. For example, do your customers need a sporadic high volume of production or does your production run need to be changed frequently? Fixture preparation, programming, material and consumable ordering should be scheduled to reduce downtime once the production is ready to be started.
Can my plant accommodate a robot?
When considering a robotic implementation, the amount of space available can be critical. In fact, the welding robot itself can be massive and furthermore, the protection around it can also take up a lot of space. Hardware such as welding power sources and consumable dispensing systems should be considered in the footprint of the robotic welding cell. Don’t forget to leave space for the parts to enter and exit the cell. You should also consider working with a robotic systems integrator to understand the safety regulations and norms that apply in your region.
Electricity parameters should also be considered. Look at your robotic welder spec sheet, as well as your power sources spec sheet to know what your needs are. You may want to consider the duty cycle for your application and make sure your building is up to date for these specifications. Most of the time, if you already possess welding machines, electricity should not be a big concern.
Do I have the proper staff to make this robot work?
To achieve production quality and to maintain it once it is launched, you need to have an experienced welder that can judge and recalibrate the robotic welding. In fact, having an employee with substantial experience can be the key to success in a good welding process. As programming methods continue to become simpler, this experienced welder can program or reprogram the robot if needed. With programming methods such as Kinetiq Teaching, the operator training time is short and the welding robot can be reprogrammed very quickly.
Initial training can be key to successful implementation. In fact, welding robot manufacturers usually provide training after buying a robot. Training can last 1 to 3 weeks and it is probably the best way to get your cell in working order in the shortest amount of time. Once your robot has been implanted, make sure to stay up to date with the industrial robot world to get the latest programming methods. Get your staff involved in continuous training and software updates.
How do I justify the expense?
Evaluate the volume of parts that can be welded by the robot in the first year and evaluate the labor time savings equivalent to this production. Keep in mind that most of the economic savings that are made by using an automated welding cell are the result of reductions in labor. If a welder is replaced by an automatic welder, he can be sent to another work station or even upgraded to a supervisory post. Calculate your payback in terms of the amount of time that you are saving by switching from a regular welding method to an automated welding method. You should take note that; small companies that automate their processes can achieve a complete payback in as short as 12 to 15 months.
Finally, implanting a robotic cell is all about planning. Plan your production, material, training, etc. Work with a trusted robot manufacturer or robotic systems integrator to have a reliable welding process. Keep in mind that your robot can be reprogrammed easily and that it’s less and less necessary to have dedicated robots, as the robots today are much more flexible than their predecessors. Look at what your options are and take a look at the link at the bottom of this page for to see how the new Robotiq Kinetic Teaching can be incorporated into your robotic welding cell.
Leave a comment