How Do Industrial Robots Achieve Compliance
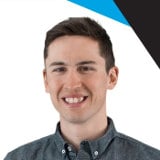
Posted on Feb 18, 2014 in Robots
3 min read time
In industrial robotics, the term compliance refers to flexibility and suppleness. To define what compliance is, the definition of non-compliance is useful. A non-compliant (stiff) robot end effector is a device which is designed to have predetermined positions or trajectories. No matter what kind of external force is exerted the robotic end effector will follow the exact same path each and every time. On the other hand, a compliant end effector can reach several positions and exert different forces on a given object. To make things clearer: a compliant robot gripper can grasp an egg without crushing it with the proper settings. A non-compliant gripper will crush the egg and continue its given operation. Compliance aims towards either process improvement (active) or human safety (passive).
Active compliance
Active compliance must be set by the user and will vary for each application process. It is commonly set up via software programming of the servo joints and uses sensors (vision sensors, force sensors, torque sensors, etc.). This family of compliance methods is aiming for better flexibility in the manufacturing process.
Passive compliance
Passive compliance is applied during the setup of the robotic cell and will always stay active in the background to fulfill its safety role. It may be inherent to the structure of the robot, like a torque limitation device on the end effector or a torque limitation on the joints. It can also be a form of collision detector that prevents collisions from occurring or prevents them from being harmful. These compliance devices are for safety purposes and are important when human-robot collaboration are intended.
Why use active compliance?
Many robotic industrial processes need flexibility, if not freedom of movement, in certain directions. For example, loading or unloading a machine will require freedom in two axes (to prevent crushing the pieces if they are misaligned) and no freedom in the loading/unloading direction. SCARA robots have been providing this flexibility for vertical assembly. The 6 or 7 axes now available on the SCARA robot arm provide even more flexibility and freedom for industrial processes.
You may also want to use active compliance for applications such as grinding, polishing, deburring, finishing, etc. Such processes need to have active compliance, because of the differences from one part to another. You don't want to use a non-compliant robot for a certain part and have a completely different result for the next part. PushCorp is developing devices for these kinds of robotic applications.
Examples of active compliance
“The robot is compliant in one direction only, which facilitates high accuracy and reliability.” It has the option of “free-float”, “spring mode” and “gravity compensation”. Stiffness and damping can also be adjusted.
Motoman’s Servo-Float:
The Servo-float manual says, “with the servo-float function, external force moves the manipulator since the torque control has priority over the position control.” The programming has two options, linked controls or linear controls. When using linked controls, the torque limit is set for each robot axis, while when using linear controls, the torque limit is set for particular Cartesian coordinates. Gravity compensation is automated.
Examples of passive compliance
Rethink's Baxter:
Working alongside humans, without any protection, requires an extreme level of passive compliance. Baxter's segments, being equipped with a large array of collision sensors, are designed to slow or stop with inadvertent contact (See an example in the following video at 1:09 min).
This type of compliance, however is regulated by ISO norms, which must be respected if the company wants to use the robot without any safety fences.
Leave a comment