Unconventional Robotic Applications in Manufacturing: Road Bike Carbon Frame
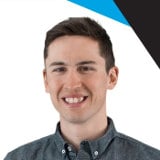
Posted on Mar 05, 2014 in Manufacturing
4 min read time
These days, robotic applications are becoming popular in every aspect of manufacturing. Processes that were completely manual a couple of years ago are now becoming robotized. Two main reasons for robotizing a process are either to enhance productivity or to increase quality and repeatability. For the Swiss company, BMC, the robotic step was more a question of quality than productivity. This relatively young company was established in 1986 because of a crazy idea by Mr. Bob Bigelow. Back then, the Swiss businessman was manufacturing mostly commuting bikes. In 2001, the company decided to support a pro cycling team called PHONAK.
From that point on, the Swiss company decided to change their way of thinking and started to invest in R&D and engineering. Their goal was to produce and sell the best bike on the market. This bike needed to be light to climb mountains, stiff to sprint and comfortable to hit the cobblestones of Belgium. Since then, BMC bikes have won different stages and general classifications in big cycling events such as Le Tour de France. Most of the production is now done outside of Switzerland, but the most high-end bike frame of their line is produced in the Alps. The BMC Impec has a complete production line dedicated to high quality and high precision bike frame manufacturing. This process is unique worldwide and it might be the first step in fully automated carbon frame manufacturing.
Braiding
If you are familiar with cycling you might already know that on a bike frame some tubes must be super stiff for maximum rigidity. On the other hand, some other tubes need to be really flexible and relatively thin to give a certain comfort to the cyclist. In the manufacturing of the BMC Impec, each tube is braided with specific carbon fiber orientation. This gives engineers the opportunity to design super stiff frames for quick acceleration and efficiency which keeps the ride super smooth. In this part of the process, an industrial robot brings a polymer tube into a carbon fiber array. The carbon wires are wrapped around the tube to get an optimized tube section depending on the specific load that will be applied. By doing this, engineers find the perfect combination of light and durable tubes. After this step, the tube is relatively flexible.
Tube molding
When the carbon fiber tubes are transferred to the next step, the hardness and the shape of each tube is now determined. As each tube on a bike frame is different, the system has to recognize the type of carbon braiding that has just happened in the last step of the process. The robot now brings the tube to an external mold where a polymer internal mold is inserted and the resin is injected. This process is similar to an application of glue between and around the fibers. The resin needs to dry out and can after be transferred to the next station.
Trimming
Once the shape has been set, the length of the tube needs to be determined. Once the tube is posed on the jig, the robot slowly removes the internal mold and the polymer tube. With those two objects being removed, the tube itself can be cut to the right length. For this process, a diamond blade is used in a closed area. Using such precautions is done to eliminate the risk of chipping the tube and to reduce carbon dust that is harmful to workers’ lungs.
Injection molding
Now that the tubes are produced, joints need to be manufactured to have a proper assembly! Using an injection method, carbon particles are injected at a high temperature and pressure. This process gives a specific shape to the joint. As this part is critical for the stiffness and security of the bike, specific attention is given to the structural propriety of the carbon once it’s molded. Parts such as the head tube (front of the frame), seat tube (where the seat is fixed), dropouts (where the back wheel is fixed) and bottom bracket (where the crank set is installed) are produced with this technique.
Paint job
BMC wanted to have the leading edge with their precise painting method, therefore they chose to use robots to apply paint. This step is critical in terms of customer satisfaction, as the repeatability and the smoothness of the robot are an added value. All the tubes and joints are painted by this method which means that every part is precisely painted on the same path. Since paint can have a harmful effect on humans, several industries prefer to use robots to paint their parts to prevent lung disease. The Swiss company, being extremely concerned about their working environment, uses a waterfall behind the painted part. As most paint rooms are equipped with big fans, this process can catch the extra paint dust and leave the air completely pure.
Printing
Once again, to be the best, you need to have a controlled process. This is one of the reasons why BMC uses robotic printers instead of stickers to register their brand name on the bike. By using this method, all of the inscriptions are at equal height and orientation when bikes are being displayed in the showroom or under the team tent.
Assembly
Since great effort is put into the manufacturing of all the different parts, the assembly is a critical step in this factory. A 6-axis industrial robot applies adhesive to a defined position to make sure all the parts are well jointed. To make sure that the adhesive is well applied, an infrared camera is used. The parts are then put together on a jig. Once the bike is "completed’’, the conveyer brings the jig under a press where the joints are pressed against a tube. After this step, all the parts form an extremely competitive bike frame.
Although the Swiss may have a reputation of having fancy and elaborate manufacturing processes, I hope that this article can give you some ideas about assembly methods. Keeping an eye out for robotic applications in manufacturing around you can be a good way to get some new ideas for your production line. I actually thought about doing this article when I saw a tweet of a pro cyclist I’m following. So get out there, look for interesting applications around you and follow us on Twitter and Facebook.
Leave a comment