How to Choose the Right Power Source for Robotic Welding Applications
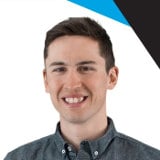
Posted on Feb 26, 2014 in Robotic Welding
4 min read time
Choosing the right robotic welding power source for your welding application can be confusing. There are not only many companies out there to choose from, but also several different models to decide between. Having the right power source for your robotic welding application is the key to a seamless integration of a welding robot. Before making a decision, you should first of all determine, document and analyze which welding operations you will use. This will determine what kind of welding will be matched to your power source. After that, the thickness of the material and the complexity of the part also have to be considered. By determining these parameters, you are indirectly determining the duty cycle required for this operation. You also need to consider other communication and electrical parameters and, of course, the physical dimensions of the power source. This analysis will be key to choosing the right power source for your robotic application in an industrial automation context. Here are the details of what you need to define to choose the right power source for your robotic welding application.
Types of robotic welding
First of all, choosing a power source is all about defining the work that has to be done with it. Make sure your source can be utilized for your robotic welding process.
Gas Metal Arc Welding (GMAW), also known as MIG, uses a spool of wire that is housed in the power source or fed by an external wire feeder. The solid metal wire is fed through a welding gun. The direct current power source is used to initiate and maintain the arc between the wire and the metal part that has to be welded. GMAW uses a shielding gas to protect the weld puddle from the atmosphere. Notice that this kind of welding can be used on most commercial metals and can be executed over a large range of material thicknesses.
Flux-Cored Arc Welding (FCAW) also uses a spool of wire that has to be housed in the power source or on an external wire feeder. The supply of wire is fed through a welding gun. The big difference between GMAW and FCAW is that the wire itself is different. In fact, as the name suggests, the hollow wire is filled with flux powder. Because of the flux powder, the use of gas to protect the weld is unnecessary. You should note that FCAW is mainly used on steels and stainless steels. This welding process can be used on a large range of material thicknesses and in any position.
Metal-Cored Arc Welding (MCAW) is a process that is very similar to the two previously mentioned processes. However, the difference is that MCAW operates over a wider range of shielding gases and offers more flexibility with alloy compositions than solid wire MIG. MCAW is mainly applied to welding carbon, carbon-manganese and alloy steels, but it may also be used for welding some stainless steel grades.
Submerged Arc Welding (SAW) uses a continuously fed wire with granular material (flux) to cover the weld area. This welding process is used on heavier plate applications, such as structural steel and on some specialized high speed welding applications. With this process, very little welding fume is produced, therefore the air in the shop is cleaner.
For all welding techniques, success hinges on the selection of the right consumables, power source, polarity on the power source, shielding gas and application technique. Be sure to use the right settings to reduce errors.
After determining the kind of work that has to be done, you want to calculate the effort that will be required by the machine. This effort is expressed in terms of duty cycle.
Duty Cycle, Welding Output, Input Power and Physical Dimensions
The duty cycle is the amount of arc-on time (welding time) calculated over a certain period of time at a rated output so as not to damage internal components. For example, a power source that is rated at a 50% duty cycle at 250 amps means that this machine can provide 250 amps for 5 minutes out of every 10 minutes. During the remaining 5 minutes, the machine is supposed to cool down. As a rule of thumb, for automatic welding applications, a machine rated at more than 290 amps at 100% is recommended. Note that all duty cycles are calculated for an ambient temperature of 40 degrees Celsius as per AS1966. Duty cycles must be reduced when the ambient temperature exceeds 40 degrees Celsius.
The welding output needed is directly related to the type of welding that has to be done. If you are looking for an automated system, the power source needs to have a welding current higher than 330 amps with a duty cycle from 50% to 100%.
The input power that is in the shop can influence the choice of your power source. Single phase 230/240 volt machines are necessary for lighter uses. For heavier uses, three-phase 415 volt machines are required.
The physical dimensions of the power source is also an important characteristic to consider. In fact, if you want to move your power source for any reason or if your environment is restricted you may want to check these geometric dimensions. Before buying your power source, make sure the dimensions and weight are suitable for your workshop.
Communication Protocols
Communication protocol is essentially the language between the power source and the robot. The protocol must be suitable for your type of industrial robot(s). Make sure to check these details before buying your power source.
By taking into account the suggested tips in this article, choosing between the different power sources will be easier. Choose a company that you trust and make sure that all the characteristics you need are present in the power source. To make your choices clearer, we have put together a comparison sheet with the different models from the most popular companies. Take a look at which power source suits you best.
Leave a comment