Robot Welding: How to get started? - Part 1
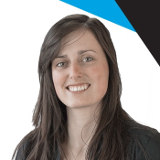
Posted on Jul 17, 2013 in Robotic Welding
4 min read time
One of the most used manufacturing processes to permanently join two parts is welding. Welding can be perform manually, i.e. done by humans, or automated, i.e. carried out by robots. These robots are called “Welding Robots”. In large manufacturing plants, they are becoming more and more popular, because they provide a lot of advantages to the production line. They are fast, consistent and do quality welds.
The principal welding processes that can be robotized are :
-
Arc Welding
-
MIG Welding
-
TIG Welding
-
Spot Welding
-
SMAW Welding
For more information about these processes, read : Industrial Arc Welding Processes
In order to robotize a welding process, the same necessary equipment and parameters already used in manual welding have to be considered. Here, we take the example of MIG welding.
Equipment
First, a power source is needed to supply constant-voltage. In order to produce high quality welds, constant-voltage and constant speed for the wire feeder are necessary. These items will enable the system to compensate for any variation in speed or distance of the welding gun in order to always produce a good welding arc.
Then, an electrode feeder is required in the welding process. It pulls the wire from a reel and puts it on the weld through a conduit in the welding torch. This unit can control the speed and tension of the wire in order to regulate the supply of filler material. On a robot welder, the reel may be installed externally on the robot arm, but this may cause obstructions with either the parts being welded, the robot itself or other devices around it. Modern welding robots have internal cabling to avoid these interferences.
The next necessary equipment is the welding torch also called a welding gun. It contains a contact to transmit current to the electrode and a tube to supply inert or semi-inert gas needed to protect the weld environment from any contamination.
Other equipment often used are jigs. In order to hold the parts in place during welding, jigs can be very useful. They are generally designed for a specific weld. In robotic applications, they are very useful because they also locate the parts for the robot. However, when it comes to high mix production, the number of jigs needed increases significantly the tooling cost. This is why Robotiq supplies great solutions, to get rid of these jigs, called flexible fixturing. Any robot using an adaptive end effector that can grab all types of pieces can replace all the necessary jigs. Even with a second robot and adaptive gripper, this new solution is cheaper than needing lots of customized jigs.
Here is a video of this application:
Parameters
The weld is affected by many parameters. A stable electric arc is important in this process and a positive direct current electrode is the best choice for current. This also produces low splatters, good weld geometry and the greatest depth penetration. Relatively low current can affect the quality of a weld through insufficient penetration.
The voltage is directly linked to the current and arc length. It also depends on the shielding gas and the electrode extension (electrode length). High arc voltage will make wide, flat welds. However too high or too low voltage will produce bad welds. So depending on which welding application you want to do, having the right combination of both the current and voltage is crucial.
The welding speed is also important to consider. Increasing the speed affects the heat transmitted to the base material. Having enough fast welding speed increases the weld penetration because the arc acts more directly on the material. However, excessive speed decreases penetration, because the heat is not high enough in the welding zone.
As stated before, the electrode length has an effect on voltage. Produced by the increased distance between the gun and the weld, the electrode length has a proportional effect on the melting rate of the electrode.
The inert or semi-inert gas used to protect the weld environment also influences the arc stability, weld shape and melting rate. The most common gases used are: argon, helium and carbon dioxide. Some mixes are also made to stabilize the welding arc, for example, argon and oxygen or carbon dioxide. Adding helium to argon will increase the heat input and the welding speed.
There are also many safety hazards in welding environments. Welders have to work with high-voltage electricity and are exposed to fumes and gases. Moreover, splatter may burn and injure workers around the welding cell. These facts class the welding process as a hazardous job. Robotic welding can be a great solution to prevent these injuries. Moreover, the lack of skilled welders has affected many industries in the past few years. Manufacturers, then, need to replace this workforce and robotic welding is the best solution for them.
To be continued...
In part 2 of this article, discover specific equipment and tools needed for robotic welding.
Leave a comment