Best Practices For Cup Selection
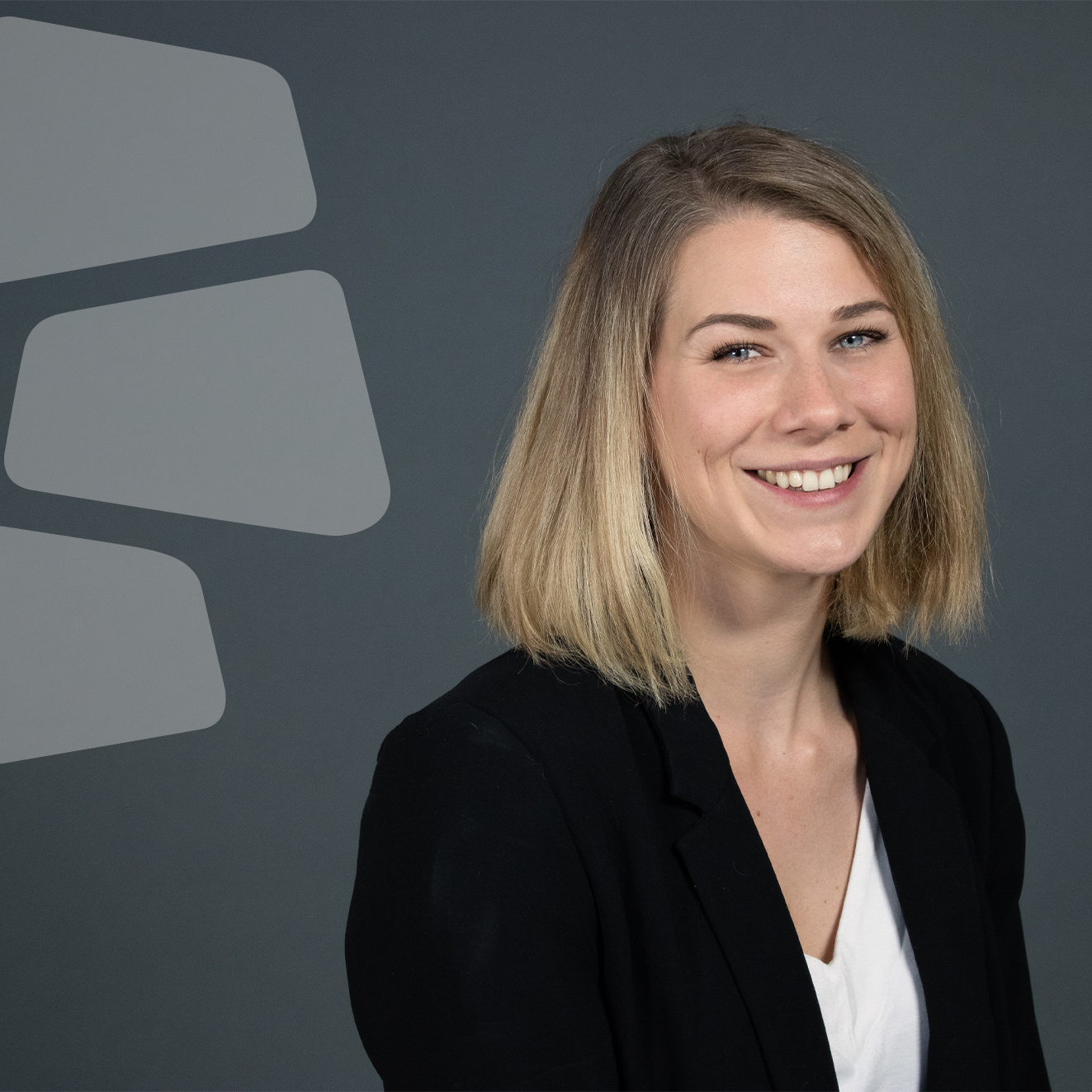
Posted on Oct 10, 2019 in Manufacturing
6 min read time
Linking the vacuum generator and the workpiece, vacuum suction cups play an essential role in the design of every vacuum-handling system. When selected correctly, vacuum suction cups can hold and manipulate a wide range of objects in many shapes, sizes and materials.
Festo offers a wide range of vacuum suction cups for use with Robotiq Vacuum Grippers. To get the most out of Vacuum Grippers like the EPick or AirPick, the size, number, and type of vacuum suction cups must be taken into consideration.
In this article, we cover five best practices for vacuum suction cup selection to help you get a grip on this complicated subject so you can make the right choice for your application.
1. Ease the Requirements on Your Vacuum Pump
Regardless of if you use the AirPick Vacuum Gripper, which can achieve a vacuum level of up to 85% using compressed air, or the EPick Vacuum Gripper, which operates without an air supply and can achieve a vacuum level of up to 80%, you should always use the largest vacuum suction cup possible to ease the requirements on your vacuum pump.
The lifting capacity of a vacuum suction cup can be determined using this simplified holding force formula:
F = P × A
where
- F = Weight of the object in pounds or grams
- P = Expected vacuum level in PSI or MPa
- A = Effective area of the vacuum suction cup measured by in2 or mm2 (Effective area will differ from area calculated directly from physical cup diameter. See manufacturers documentation. Some manufacturer’s like Festo, will provide holding force values directly at a reference pressure for a given cup)
By using a larger vacuum suction cup, it’s possible to manipulate a heavier object using the same pressure. Conversely, a smaller vacuum suction cup requires a greater vacuum level to lift the same object. Keeping the pressure low not only helps ensure long pump life, but it also greatly decreases energy requirements, since the vacuum force and the energy needed to produce that force don’t scale linearly.
2. Add Safety to Your System
To lift and manipulate an object, a vacuum-generating device is used to reduce the atmospheric pressure inside the vacuum suction cup and create a partial vacuum. This pressure difference (when compared with the pressure of the air around the vacuum suction cup) pushes down on the cup, squashing it against the object, and, at the same time, pushing the object against the inner walls of the cup due to the lower pressure.
In the section above, we explained how to determine the lifting capacity of a vacuum suction cup—but be warned, this simple formula doesn’t take into consideration the numerous variables surrounding lifting applications.
To account for these and other external influences, we recommend including a safety factor of at least 1.5 for smooth objects, 2.0 for porous or oily objects, and as much as 4.0 when the vacuum suction cup face is in a vertical position. Use the following formula to:
F = (P × A) × S
where
- F = Weight of the object in pounds or grams
- P = Expected vacuum level in PSI or Kpa
- A = Effective area of the vacuum suction cup measured by in2 or mm2
- S = Safety factor
3. Don’t Forget to Consider Acceleration
With their quick response times, great precision, and remarkable versatility, Vacuum Grippers can handle a wide range of applications and greatly exceed the performance of human operators. In situations when high handling speeds are demanded, it’s paramount to consider another important factor when selecting the right vacuum suction cup: acceleration, or the change in velocity of a moving object with respect to time.
Acceleration is a vector, and its unit is meters per second squared, symbolized as “a.” Gravitational acceleration (symbolized as g) is approximately 9.8 m/s2, meaning that the speed of an object falling freely will increase by about 9.8 meters per second every second. The average acceleration can be calculated with the following formula:
Acceleration = Velocity / Time
To take into account both the acceleration of the vacuum-handling system and gravitational acceleration, the following holding-force formula can be used in situations with a horizontal vacuum suction cup and a vertical direction of force:
FH = m × (g + a) × S
where
- FH (theoretical holding force) = the required theoretical holding force acting perpendicular to the workpiece surface, in Newtons (N).
- m (mass) = Volume of the object multiplied by its material density, measured in grams.
- g (gravity) = Gravitational acceleration (9.8 m/s2).
- a (acceleration) = Change in velocity of a moving object with respect to time (m/s2).
- S (safety factor) = How much stronger the vacuum-handling system needs to be.
The safety factor in high-speed swinging or swiveling operations should be 2.5 or higher.
In situations with a horizontal direction of force and a horizontal vacuum suction cup, it’s also necessary to consider the relationship between friction force and normal force by including the friction coefficient (μ):
FH = m × (g + a/μ) × S
If the direction of force is vertical and the vacuum suction cup is also vertical, the friction coefficient can be included as follows:
FH = (m/μ) x (g + a) x S
The friction coefficient should be determined correctly through tests, but the following can be used as reference values:
- Oily surfaces = 0.1
- Wet surfaces = 0.2–0.3
- Rough surfaces = 0.6
- Wood, metal, glass, stone surfaces = 0.5
4. Use Smaller Cups to Lift Porous Materials
We’ve explained the advantages of using large vacuum suction cups, but there are some applications where smaller cups are better, such as when manipulating porous materials like corrugated fiberboard or textiles.
Smaller vacuum suction cups are less prone to leakage than larger cups, which can manipulate porous materials only when combined with a high-flow pump capable of compensating for their inherent leakage. By using smaller cups, you can achieve the same lifting capacity while saving compressed air and energy.
Another scenario when it’s better to use, say, four smaller vacuum suction cups instead of two larger cups involves the handling of thin metal plates and other delicate objects that could be bent or damaged if too much lifting force is concentrated in a single area.
5. Select the Right Cup Material for Your Application
Vacuum suction cups are available in many different materials, including polyurethane, butadiene rubber, nitrile rubber, silicone, and the synthetic rubber and fluoropolymer elastomer commonly known as Viton. Each of these materials has a different resistance to wear, tearing, deformation, extreme temperatures, and chemicals.
Polyurethane stands out with its oil resistance, which is why it’s readily used in the automobile industry. The antistatic properties of butadiene rubber make it a great choice for the electronics industry, where static electricity is a critical issue, causing an estimated $5 billion worth of damage each year to electronic devices.
Nitrile rubber is a versatile material suitable for conventional applications, and its main advantage is its low cost. Both Viton and silicone suction cups are resistant to temperatures, with the latter being approved for use in the food industry thanks to its non-reactive nature.
Conclusion
Despite their humble appearance, vacuum suction cups are just as important for the smooth operation of a vacuum-handling system as Vacuum Grippers themselves. Today, vacuum suction cups are available in a broad range of materials, shapes, and sizes, which must be carefully selected based on the intended application. In this article, we explained five best practices for successful vacuum suction cup selection. Keeping these best practices in mind when selecting Festo’s vacuum suction cups for use with the EPick and AirPick Vacuum Grippers from Robotiq is key to enabling the entire vacuum-handling system to operate in a safe, reliable, and efficient fashion.
Leave a comment