10 Fundamental Factors for Superb Sanding and Polishing
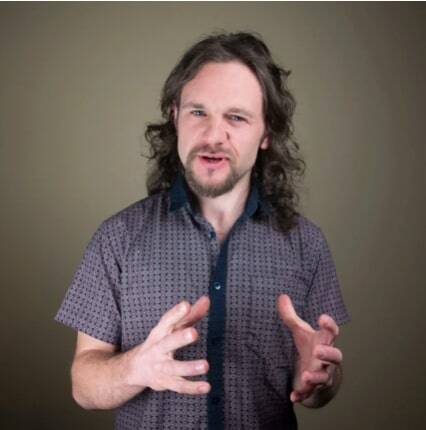
Posted on May 15, 2019 in Manufacturing
6 min read time
How can you ensure that your robot finishing application will be a success? Here are some fundamental factors which will affect both sanding and polishing.
Finishing tasks are a great way to use collaborative robots. Sanding and polishing are dreary, dusty, and dreadfully repetitive which makes them a perfect candidate for automation.
But, even when you have a dedicated sanding kit for cobots, there are some important factors which can affect the quality of your finishing task. Here are our top 10 fundamental factors that you should keep in mind for superb sanding and polishing.
Robotiq is a pioneer in collaborative robot finishing tasks
1. Finishing type
Are you doing sanding, polishing, or buffing?
All three of these surface finishing processes are compatible with cobots. They are all basically variations of the same process — using abrasive grit to remove surface defects (e.g. scratches) from a material — but with some slight differences.
The definition of each term varies depending on who is using it, but here are some basic definitions:
- Sanding — A reductive process aimed at removing large amounts of material to remove defects.
- Polishing — Uses smaller grit sizes to create a flat, defect-free surface when examined under a microscope.
- Buffing — Uses a soft material (e.g. fabric cloth) with an abrasive compound.
2. Workpiece material
A range of materials are compatible with cobot sanding. For example, the Robotiq Sanding Kit supports wood, plastic, metal, fiberglass, solid surface (e.g. marble), and carbon fiber.
Each material will respond differently to sanding and polishing. Some will require special abrasive media, others will just require a different sanding/polishing strategy.
3. Abrasive/polishing media
The choice of abrasive media (e.g sandpaper) probably has the biggest effect on the type and quality of sanding/polishing that you can achieve.
4. Strategy
Finishing processes rely on a clear, consistent strategy.
What pattern will you use to move the abrasive media across the workpiece? Examples include: row by row, with the grain, circular motions, etc.
Which different grit sizes will you use for each progressive pass of the sanding tool? With each progressive grit, you should gradually remove smaller and smaller amounts of material. As a result, the recommended strategy is to start with the coarsest grit and get finer with each pass.
Will you change the type of abrasive media between different passes? For example, you might change from a coated abrasive, then to a non-woven abrasive, then to a buffing fabric.
5. Speed
There are two speeds that affect the quality of a sanding or polishing task:
- The speed of the sanding tool, e.g. how quickly an orbital sanding tool spins.
- The speed that the robot moves across the surface of the material.
Both of these speeds should remain consistent across the entire surface of the material. Robots are actually better keeping a consistent speed than humans.
6. Force
The robot needs to apply a force onto the material to keep the sanding media in contact with the surface. This is achieved by using a force sensor and is programmed using force control.
The key here is not to "push hard" onto the surface — in fact, a common tip for sanding by hand is to use only the weight of the sanding machine to provide the downward force. Instead, the robot just needs to provide a consistent force as it moves across the material.
7. Material removal rate
All five of the previous factors (material, media, strategy, speed, and force) combine together to get the material removal rate (MRR).
As the name suggests, this refers to how quickly material is removed by the abrasive media. The property can be given as "material volume per minute" or "material weight per minute."
Here's how the previous factors affect MRR:
- Material — Softer materials will be removed more quickly than harder materials.
- Abrasive media — Coarser grits (which usually have a lower rating number) will remove material faster than finer grits, but will also leave more pronounced lines in the material.
- Strategy — Ineffective patterns may lead to some areas of the workpiece receiving more attention than others, which increases MRR in those areas.
- Speed — When the sanding tool spins faster, it removes material more quickly. When the robot moves faster, however, the MRR in any specific area of the workpiece will be lower.
- Force — The more force that is applied, the quicker material will be removed. However, high forces can lead to inconsistent sanding/polishing and wears down the abrasive media faster.
8. Wear rate
The wear rate refers to how quickly the abrasive media wears down. In other words, how often you need to change it.
This factor doesn't really affect the quality of the finishing task, but it can affect the efficiency of the whole task. If you have to change the sanding pad every 10 minutes, it will make less sense to use robot sanding than if you only have to change it once every 2 hours.
The wear rate will depend on many of the previous factors, but mostly on the choice of abrasive media and the workpiece material. If you have a high wear rate, try changing the abrasive media.
9. Connection to robot
In order for robotic sanding and polishing to make sense for your business, it should be easy to add the capability to your collaborative robot. You shouldn't have to spend a lot of time and money to integrate a sanding tool with the robot.
Before committing to robotic sanding or polishing, you should make sure that there is a solution which is easy to integrate with your collaborative robot. For example, the Robotiq Sanding Kit is designed to be used with Universal Robots.
10. Programming ease
In the past, possibly the biggest roadblock to robotic sanding was the difficulty of programming. Because it needs force control, it has traditionally been challenging to implement sanding strategies in robot controllers. Programming used to take hours, if not days.
But, with the right solution your sanding application can be programmed within a matter of minutes!
Which factors are most important to your sanding tasks? Tell us in the comments below or join the discussion on LinkedIn, Twitter, Facebook or the DoF professional robotics community.
Leave a comment