10 Common Sanding and Polishing Problems That Robots Eliminate
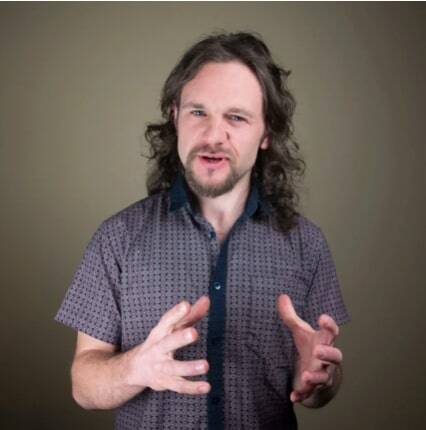
Sanding and polishing with power tools can be fraught with problems. Even highly skilled professionals aren't immune! But, robot finishing provides a solution that can eliminate these pesky problems.
You know how it is…
You start your sanding or polishing task with the best intentions. You think "This sanding is going to be flawless. I will be completely consistent and get the same quality over the entire workpiece surface…"
But then…
… minutes pass and your old wrist injury starts to hurt, you alter your grip to steady the tool…
… hours pass and your arms start to feel like jelly, you push harder to avoid shaking…
… after the 100th workpiece, you start forgetting which areas you've sanded.
It's practically impossible to be consistent when we do finishing tasks by hand. Even when we're highly skilled, it is a tedious and strenuous job. It's easy to lose concentration and stray from our usual high standards.
Robotic finishing is a great way to improve the quality (and reduce the boredom) of sanding and polishing tasks. Even better, it removes some of the most common sanding and polishing mistakes compared to doing the tasks by hand with a power tool.
Here are our top 10 problems that robots can eliminate:
1. Sanding syndrome
First, the worst of all sanding problems… the dreaded sanding syndrome!
Family Handyman magazine defines it like this:
"Sanding Syndrome is a psychological disorder caused by fussy attention to detail combined with brain-rotting boredom. Symptoms include drooling on the project, hearing voices in the whine of a belt sander and seeing cartoon characters in wood grain patterns."
The boredom of sanding and polishing tasks is the root cause of many of the rest of the problems. When we get bored and tired it can start to take its toll, especially as we're holding a noisy, dusty, vibrating sanding machine.
Robots never get bored. They just keep performing the exact same movements again and again.
2. Edge rounding
We've all done it. You run your sanding machine along the the edge of the workpiece. For a brief moment, the machine tilts away from being square on the surface and suddenly you've rounded the edge of the workpiece.
Unintentional edge rounding is especially common when sanding soft materials (e.g. wood or plastic) with a coarse grit. However, it can happen to some degree with any material and abrasive.
The solution is to keep the sanding tool exactly square with the material at all times. For us humans, that can be difficult. For a robot it's the easiest thing in the world!
3. Corner mistakes
Sure, it's easy to unintentionally round the edges of your workpiece. But, it's even easier to unintentionally round, cup, or otherwise mess up the corners.
Corner mistakes are especially problematic because they can happen so quickly. When you run an finishing tool around the corner, for a moment only a tiny part of the abrasive is in contact with the material. This means that a very high force is concentrated on a small area. As a result, material is removed very quickly.
Robotic solutions (like our Sanding Kit for UR robots) have force control, which means you can accurately reduce high forces and keep a consistent motion to avoid corner rounding.
4. Flaw fixation
In life, we humans often fixate on the flaws and ignore the good things. This is also true in finishing tasks. We focus on the areas of the workpiece with scratches, bulges, and other marks. This can have disastrous consequences.
When we give too much attention to the flaws, it often means that we neglect the other areas of the surface which can lead to an uneven finish. Robots will provide a consistent finish across the whole workpiece.
5. Sanding bias
It's easy for us to get lulled into sanding or polishing what is right in front of us. This can lead to "sanding bias" where we pay more attention to one face of the workpiece simply because it is most visible.
Robots do not have such a bias. They will follow the exact path that you have programmed.
6. Tilting edge
One of the most common mistakes when sanding by hand is to tilt the sanding tool onto its edge. We usually do this for a "good" reason: it gets rid of surface flaws quicker. Tilting the tool adds more pressure to one edge of the abrasive which means we can remove spot flaws quickly. However, it wears down the edge of the abrasive and (more importantly) causes an inconsistent finish.
A robot will always apply a consistent force onto the surface of the material, without tilting the tool.
7. Speeding up
As we get further into the finishing task, it's understandable that we often start to speed up. "Sanding syndrome" kicks in, we get tired, and unconsciously we start to think "Let's just get this task over with!"
Many finishing tools (e.g. random orbital sanders and polishers) are designed to be used very slowly. Speeding up is not a good strategy. It doesn't make the job end any sooner and it produces an inconsistent surface finish.
8. Inconsistent speed
An extension of the previous problem, inconsistent speed is very common when finishing by hand with a power tool. There are various reasons we might speed up or slow down, including: having to stretch to reach parts of the workpiece, giving ourselves a mini-rest, and (of course) boredom.
Robots will move at whatever speed you program into them and never get bored.
9. Pressing down
A sanding or polishing tool really doesn't need you to apply any more pressure onto the surface than the weight of the machine. However, we often have a tendency to press down on the surface, either to keep the machine steady as we get tired or in an attempt to speed up the job.
At best, this can lead to a bad surface finish. At worst, it can damage the motor of the tool.
The force control in robot sanding means that it will always provide a consistent force onto the workpiece.
10. Being human
Let's face it. The real root cause of all of the previous problems is just one thing: we are only human.
Sanding and polishing are tough tasks to do with a consistent level of quality because they basically require us to "work like a robot". To do them well, we need to move at a consistent speed, applying a consistent force, and following a consistent path… for hours and hours and hours.
Why not make things easy for ourselves? Just do them with a robot in the first place!
How would life be easier for you if you didn't have to do finishing tasks by hand? Tell us in the comments below or join the discussion on LinkedIn, Twitter, Facebook or the DoF professional robotics community.
Leave a comment