How to re-grasp a part for perfect accuracy in a bin picking application?
In some bin picking application it is necessary to pick parts at a precise location to present it to the next processing step (CNC, stamping machine,...). This article present a technique to pick part at a precise location.
Objects are picked in the bin at an approximative location. The picking position may vary from one object to another.
This variation can have several causes:
- the object position is estimated by a vision system (3D camera, 2D camera,...) which have some positioning error
- The picking point setting allow some positioning flexibility to ease part access
If after the picking you have to place the part on a conveyor for example, an approximative picking position won't be an issue.
However if you have to place the part in a machine you will need more precision. In those cases a re-grasp jig can be use to correct the picking point position.
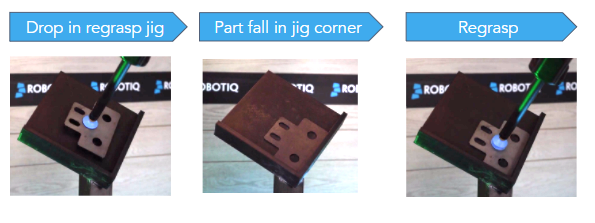
The process is to drop the part on the JIG. The part fall in the corner of the jig and the robot re-grasp the part at a precise position.
The design of the re-grasp JIG may vary demanding on part shape.
This method improve the precision of the picking position but it also take time. Here below is an example an estimation of the impact of this method on bin picking through put.

- Green is the possible throughput
- Yellow is challenging throughput
- Red is almost impossible throughput
It is possible to manage the variation of the picking position by positioning the part using force sensing software like Machine tending Copilot.